Contents
- What is Kaizen?
- Why is Kaizen important in business?
- How does Kaizen differ from Traditional Improvement methods?
- What are the Benefits of Implementing Kaizen in your organisation?
- Kaizen Principles
- Kaizen and PDCA cycle
- 5S and Kaizen in Lean Process Improvement
- How is Kaizen related to Lean Six Sigma?
- Which business processes require strict adherence to Kaizen processes ?
- How can businesses implement Kaizen in their operations?
- What Tools are commonly used in Kaizen processes?
- Is Kaizen applicable to all industries?
- Kaizen Event
- Overcoming Challenges for successful Kaizen Implementation
- What is Gemba Kaizen?
- Kaizen and Kanban
- Examples of Kaizen in Action
What is Kaizen?
Kaizen, in Japanese, is a continuous improvement philosophy that centres on making incremental changes to enhance efficiency, quality, and operational processes over time.
The five elements of Kaizen include:
- Quality circles
- Teamwork
- Improved morale
- Suggestions for improvement
- Personal discipline
Kaizen manifests in various types. Each type of Kaizen plays a distinct role on the shop floor, contributing to the overall efficiency, organisation, and continuous improvement of organisational processes.
- Point Kaizen: Swift and targeted, Point Kaizen rapidly improves specific workstations with minimal planning. While changes are small and easily implemented, there's a potential boomerang effect, where positive alterations in one area may slightly affect another.
- System Kaizen: Organised and strategic, System Kaizen tackles overall system issues with upper-level planning, leading to scheduled events over an extended period. In contrast to Point Kaizen's immediacy, System Kaizen adopts a long-term, planned strategy for continuous improvement.
- Line Kaizen: Resembling a model line process, Line Kaizen focuses on structured enhancements, like simultaneous improvements in procurement and planning. Going beyond Point Kaizen, it aligns improvements with the flow of processes, making effects visible along a line of operations.
- Plane Kaizen: A step beyond Line Kaizen, Plane Kaizen connects multiple lines or processes, creating a value stream. In modern terms, organisations are structured into product lines, enabling changes in one line to influence several others. This approach envisions a more integrated and interconnected improvement process.
- Cube Kaizen: At the most comprehensive level, Cube Kaizen ensures interconnected improvements with no disconnection between processes. It represents a scenario where Lean principles spread throughout the organisation, extending even to suppliers and customers. This type of Kaizen necessitates changes in standard business processes, ensuring improvements impact the entire organisational structure.
The three pillars of Kaizen are 5S, waste elimination, and standardisation, which form the foundation for sustained improvement.
Why is Kaizen important in business?
Kaizen is crucial for businesses as it fosters a culture of continuous improvement, driving enhanced efficiency, quality, and productivity. By encouraging small, incremental process changes, Kaizen empowers employees to identify and address issues, leading to a more streamlined and agile operation. This approach reduces waste and promotes innovation and adaptability in the face of evolving market demands. Kaizen is instrumental in creating a proactive and engaged workforce, aligning business practices with customer needs and industry best practices, ultimately contributing to sustained growth and competitiveness.
How does Kaizen differ from Traditional Improvement methods?
Kaizen differs significantly from traditional improvement methods in its approach and philosophy. While traditional methods often involve large-scale, infrequent changes, Kaizen emphasises small, continuous, and incremental improvements. Traditional methods focus on fixing major issues after they occur, whereas Kaizen encourages proactive problem identification and solution implementation by all employees. Moreover, Kaizen promotes a culture of employee engagement and empowerment, encouraging individuals at all levels to contribute ideas for improvement. Traditional methods may be rigid and top-down, while Kaizen is flexible and adaptive and seeks input from those directly involved in the processes.
What are the Benefits of Implementing Kaizen in your organisation?
- Minimise Waste and Optimise Efficiency
- Simplify and Streamline Work Processes
- Improve Safety in Operations and Rectify Potential Hazards
- Ensure Employee Satisfaction and Boosts Morale
- Improve Customer Satisfaction
- Enhance Quality Management
- Boosting Innovation
- Increasing Productivity
- Enhance Project Management
- Save Costs
- Enhance Communication
- Gain Competitive Advantage
- Ensure Long-Term Sustainability
Schedule a Demo to understand how Kaizen can benefit your organisation.
Kaizen Principles
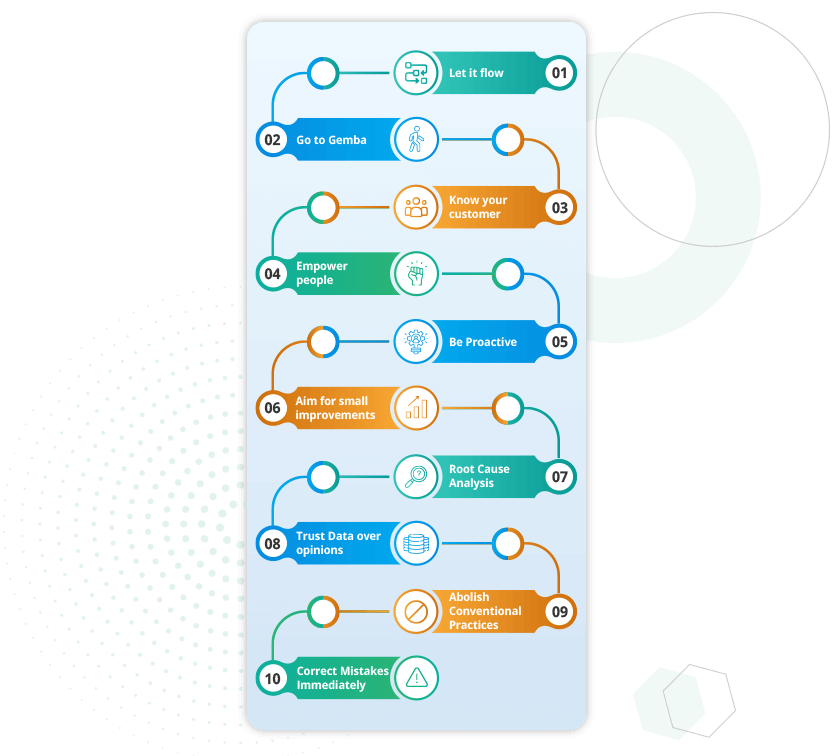
- Let it flow: Focuses on optimising processes to achieve a smooth and continuous workflow, minimising interruptions and eliminating waste.
- Go to Gemba: Encourages leaders and decision-makers to go to the actual workplace to observe and understand processes, fostering firsthand knowledge and insights.
- Know your customer: Emphasises understanding customer needs and expectations to align processes with delivering value, ensuring customer satisfaction.
- Empower people: Promotes a culture of empowerment, transparency, and open communication, allowing employees to contribute ideas and solutions for improvement.
- Be proactive: Encourages a proactive approach to problem-solving and improvement, addressing issues before they become major challenges.
- Aim for small improvements: Advocates for continuous, incremental improvements rather than waiting for ideal solutions, recognising that small changes can lead to significant progress over time.
- Root Cause Analysis: Encourages a systematic approach to problem-solving by identifying and addressing the root causes rather than just treating symptoms.
- Trust Data over opinions: Prioritises data-driven decision-making, relying on factual information and analysis rather than subjective opinions.
- Abolish Conventional Practices: Challenges the status quo by questioning and eliminating outdated or inefficient practices, creating innovative and more effective methods.
- Correct Mistakes Immediately: Stresses the importance of swift corrective actions when mistakes occur, preventing the recurrence of issues and fostering a culture of continuous learning and improvement.
Kaizen and PDCA cycle
The PDCA cycle, also known as the Deming Wheel or Shewhart Cycle, provides a systematic framework for organisations to identify, implement, and refine improvements cyclically, ensuring sustained progress in pursuit of excellence. The PDCA (Plan-Do-Check-Act) cycle is integral to the Kaizen philosophy, supporting continuous improvement processes within an organisation. The cycle starts with planning (Plan), where goals and processes are outlined, then moves to implementation (Do), followed by a thorough evaluation (Check) of outcomes against objectives. Subsequently, adjustments are made as needed (Act). This iterative nature aligns with Kaizen's essence, fostering a culture of continuous improvement, efficiency, and adaptability.
5S and Kaizen in Lean Process Improvement
In business process improvement, the combination of 5S and Kaizen plays a crucial role in Lean methodologies. The 5S principles (Sort, Set in order, Shine, Standardise, and Sustain) form a foundational framework for organising and optimising the workplace. When integrated with Kaizen, which focuses on continuous improvement, these principles become catalysts for efficiency and quality enhancements. The disciplined approach of 5S ensures a clutter-free, standardised, and visually managed workspace, laying the groundwork for Kaizen's continuous improvement initiatives. Together, 5S and Kaizen foster a culture of sustained excellence in lean process improvement, enhancing operational performance and driving long-term success.
Which business processes require strict adherence to Kaizen processes ?
Kaizen is particularly relevant in production lines, supply chain management, and customer service, where incremental enhancements lead to significant operational excellence. It is applied across all organisational levels, encouraging frontline employees and management alike to participate in identifying and implementing improvements. Kaizen's user base extends to all levels of an organisation, emphasising that anyone, from frontline workers to executives, should actively pursue continuous improvement. The strict adherence to Kaizen processes ensures a dynamic and responsive approach to evolving business challenges, promoting adaptability and long-term success.
How can businesses implement Kaizen in their operations?
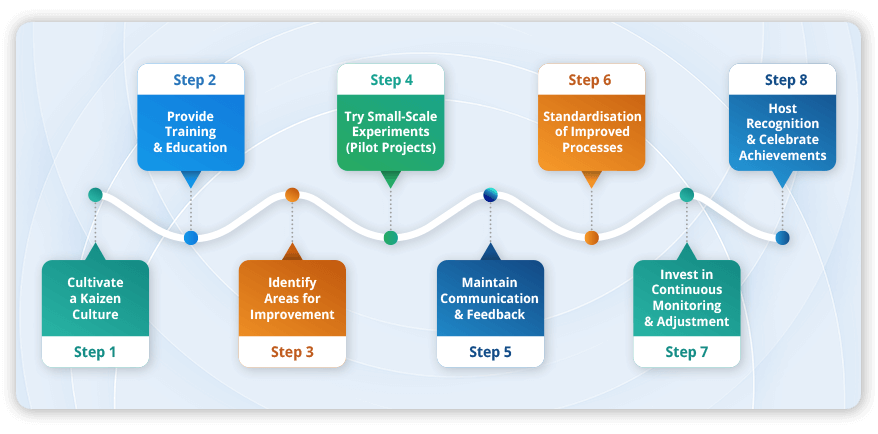
If you understand how Kaizen works for your business, the next step you should take is to implement Kaizen for process enhancement.
Steps to implement Kaizen in your organisation include:
-
Step 1: Cultivate a Kaizen Culture
- Foster a mindset of continuous improvement at all levels of the organisation.
- Encourage employees to actively participate in identifying areas for enhancement.
-
Step 2: Provide Training and Education
- Provide comprehensive training on Kaizen principles and methodologies.
- Ensure that employees understand the importance of small, incremental changes.
-
Step 3: Identify Areas for Improvement
- Conduct regular assessments of business processes to pinpoint areas for optimisation.
- Involve employees in identifying bottlenecks, inefficiencies, or opportunities for improvement.
-
Step 4: Try Small-Scale Experiments (Pilot Projects)
- Initiate small-scale Kaizen projects to test and implement proposed changes.
- Monitor the impact of these changes on efficiency and quality.
-
Step 5: Maintain Communication and Feedback
- Establish open channels for feedback and communication.
- Encourage your employees to share ideas and insights for continuous improvement.
-
Step 6: Standardisation of Improved Processes
- Once successful changes are identified, standardise these improvements.
- Develop guidelines and procedures to ensure the sustainability of positive changes.
-
Step 7: Invest in Continuous Monitoring and Adjustment
- Implement systems like Tcards for monitoring the status of shop floor processes.
- Adjust and refine procedures based on real-time feedback and performance data.
-
Step 8: Host Recognition and Celebrate Achievements
- Acknowledge and celebrate the achievements resulting from Kaizen efforts.
- Recognise and reward individuals or teams contributing to continuous improvement.
What Tools are commonly used in Kaizen processes?
The advantages of using Kaizen tools in a lean manufacturing environment include:
- Improved process visibility
- Enhanced communication
- Identify and eliminate waste
Kaizen tools empower organisations to streamline operations, reduce costs, and continuously enhance product quality. Commonly used tools in Kaizen processes include:
- Kanban Board: Kanban is a visual management tool that helps teams track work progress, promote collaboration, and maintain a smooth workflow by visualising tasks on cards that move across the board.
- Kaizen Software: The Kaizen software is designed to facilitate the implementation and tracking of Kaizen initiatives, providing a digital platform for collaboration, data analysis, and measuring continuous improvement efforts.
- Tcard: Digital T cards facilitate the systematic implementation of continuous improvement initiatives by providing a digital platform for collaboration, data analysis, and project tracking. It enhances communication and centralises information, fostering efficiency and organisation in the Kaizen process.
- Kaizen Board: A Kaizen Board is a visual management tool that displays ongoing Kaizen initiatives, progress, and action items. It enhances communication and collaboration among team members, ensuring a collective focus on continuous improvement goals.
- Value Stream Mapping (VSM): A process visualisation tool that illustrates the steps and information flow required to deliver a product or service, enabling organisations to identify and eliminate non-value-added activities.
- 5S: A set of workplace organisation techniques (Sort, Set in order, Shine, Standardise, Sustain) designed to improve efficiency, safety, and overall work environment, forming the foundation for Kaizen initiatives.
- PDCA Cycle: A structured problem-solving approach comprising Plan, Do, Check, and Act stages, providing a systematic method for continuous improvement and problem resolution.
- Poka Yoke: This technique focuses on error-proofing devices or mechanisms that prevent mistakes or defects during the production process, ensuring higher quality and efficiency.
- JIT Manufacturing (Just-in-Time): An inventory management approach that aims to produce and deliver goods exactly when they are needed, minimising waste and excess inventory while improving overall efficiency.
Is Kaizen applicable to all industries?
Yes, Kaizen is a comprehensive and versatile solution that can be implemented across diverse industries, irrespective of size or operational processes. Kaizen principles of continuous improvement and waste reduction make it universally applicable. In manufacturing, Kaizen optimises production processes; in healthcare, it enhances patient care workflows; in logistics, it streamlines supply chain operations. From service industries like finance and IT to education and construction, Kaizen effectively fosters a culture of ongoing improvement. Its adaptability ensures relevance in retail and hospitality sectors, making Kaizen a valuable methodology for any industry committed to sustainable growth and efficiency.
Kaizen Event
Kaizen, a fundamental pillar of the Toyota Production System, traces its roots to post-World War II Japan and the visionary efforts of Masaaki Imai, often regarded as the father of Kaizen. Kaizen Event, also known as a Kaizen Blitz, is a targeted and efficient approach to process improvement, carried out in three distinct stages.
-
Pre-Kaizen Preparation
- This stage involves identifying immediate issues, defining the scope of the problem, and setting SMART objectives (Specific, Measurable, Achievable, Relevant, and Time-bound) that generally last 14-45 days.
- Steps include selecting a team leader and members, collecting relevant data, and gaining sponsorship from top management.
-
Kaizen Event
- Taking place over 2-10 days, this is the core phase where the team focuses on improving specific business processes.
- Activities range from training members on the blitz process, reviewing the current situation, and identifying key issues to developing impactful solutions, gaining stakeholder input, and presenting recommendations for approval.
-
Implementation (Follow-Up)
- The implementation or follow-up stage involves continuous improvement by implementing solutions, coordinating process changes, and measuring project success, lasting 0- 60 days.
- Achievements are submitted to sponsors or top management, ensuring that the benefits of the Kaizen Blitz are sustained and contribute to the overall goal of continuous improvement in the business process.
Overcoming Challenges for successful Kaizen Implementation
- Provide comprehensive training on Kaizen principles and methodologies.
- Set realistic and achievable goals for continuous improvement.
- Establish strong leadership support and commitment.
- Encourage a mindset of adaptability and flexibility.
- Address resistance to change through effective communication.
- Regularly measure and communicate the benefits of Kaizen initiatives.
- Recognize and celebrate small victories and improvements.
- Ensure cross-functional collaboration and teamwork.
- Utilise data-driven decision-making for process improvements.
- Continuously refine and optimise Kaizen processes based on feedback.
What is Gemba Kaizen?
Gemba Kaizen is a Japanese term that translates to "continuous improvement at the workplace" or "real place improvement." It emphasises the practice of making small, incremental changes to processes directly at the location where the work is done or value is created through direct observation of shop floor processes, known as the "Gemba." Leadership commitment is a critical aspect of Gemba Kaizen, as it involves leaders actively engaging with frontline employees to understand their challenges and opportunities for improvement. T card and Kanban boards are commonly used tools in Gemba Kaizen, aiding in visual management and implementing improvements. T cards signal the need for replenishment or actions to be taken, while Kanban boards provide a visual representation of the workflow, enabling teams to track and manage tasks in real-time. By combining leadership commitment with these tools, Gemba Kaizen promotes a culture of continuous improvement and efficiency directly where the work happens, ensuring sustained progress and excellence.
Kaizen and Kanban
Kanban, a visual management tool, is pivotal in facilitating the systematic implementation of Kaizen principles. Kanban enhances transparency by providing a clear and visual representation of tasks, stages, and workflow, allowing teams to identify inefficiencies, reduce waste, and continuously optimise processes. The dynamic synergy between Kaizen and Kanban ensures that incremental improvements are identified and seamlessly integrated into the workflow, fostering a culture of continuous enhancement within the organisation.
Examples of Kaizen in Action
-
Manufacturing Industry
A manufacturing company implemented Kaizen to improve the efficiency of its production line.
- Identifying the problems: The Kaizen team identifies a bottleneck in the assembly process that slows down overall production.
- Implementing Standardised Actions for achieving optimal results: Through a series of small-scale experiments, they reorganise workstations, standardise operational procedures, and implement visual cues. This leads to a significant reduction in production time, increased output, and improved overall efficiency.
-
Automotive Industry
In the automobile industry, a Kaizen initiative focused on reducing defects in the painting process.
- Identifying the issue: The Kaizen team systematically analysed the painting procedures, identified areas prone to imperfections, and introduced Poka Yoke (error-proofing) mechanisms.
- Implementing Standardised Actions for achieving optimal results: The company successfully reduces the occurrence of paint defects, enhancing the overall quality of the finished vehicles by implementing quality checks at each stage and incorporating employee suggestions.
-
Service Industry
In a service-oriented business, Kaizen is applied to enhance response times and customer satisfaction.
- Identifying the issues: The Kaizen team examined the existing customer service process, identified communication bottlenecks, and introduced a Kanban system for task management.
- Implementing Standardised Actions for achieving optimal Results: Now, the service team has reduced response times, improved issue resolution, and heightened customer satisfaction levels through proper employee scheduling and real-time monitoring of tasks and making necessary adjustments when needed.
Take the First Step toward Continuous Improvement with Kaizen
Empower your organisation with Kaizen's principles to enhance efficiency, streamline processes, and foster a culture of collaboration and improvement.