What is a Kanban Board?
Kanban boards enhance workflow visibility, enabling efficient bottleneck detection, progress tracking, and task prioritisation.
Try Kanban for Free Watch VideoContents
- What are Kanban Boards?
- Kanban System
- History of Kanban Systems
- Kanban Principles
- Kanban Practices
- Kanban Board features and components
- Types of Kanban Boards
- Top 5 benefits of using a Kanban board
- How to create a Kanban Board?
- Kanban in Lean Manufacturing
- How to choose the right Kanban board software?
- How can the Kanban board affect your ROI?
- How does Online Kanban Board help remote or distributed teams?
- How does a Kanban board work?
- Kanban List View
- Workflow management with Kanban
- How do I create a Workflow in Kanban Board?
- Personal Kanban
- What Metrics can be tracked and measured using Kanban Tool?
- How do you Track Progress in Kanban?
- What is the difference between Cycle time and Lead time in Kanban?
- Kanban Reports
- How to use Kanban Boards?
- Kanban Template
- Kanban Visual Systems
- Kanban Project Management
- Kanban Inventory Management
- Kanban Board Examples
What are Kanban Boards?
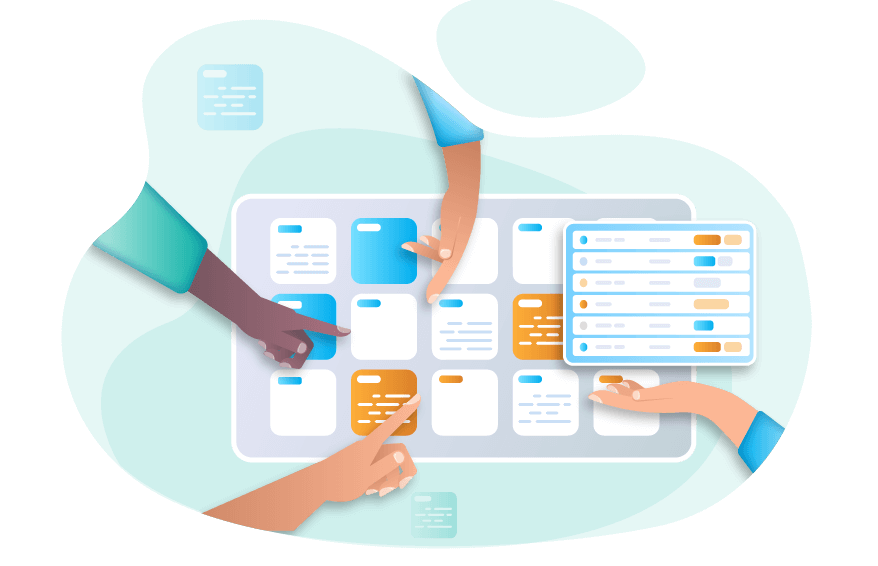
The Kanban board is a lean project management tool designed to enhance task management by providing a visual representation of work items, limiting Work-in-Progress (WIP), and optimising efficiency and flow. The Kanban system optimises the work delivery across multiple teams in a single Kanban board. Digital Kanban boards visually depict work items using Kanban Cards and Kanban columns to represent each stage of the task progress. By providing a visual system for the teams, kanban boards can manage the project tasks and streamline communication, giving a bigger picture of your workflow.
Kanban System
Kanban means "Cards you can see". You can also define Kanban as a popular Lean visual workflow method that can help you track the workflow and get informed about the progress of each task. Kanban marks the available capacity to work. The digital Kanban system is linked to the lean concept of Just in Time(JIT) production, where the schedules tell you what to produce when and in what quantity. Project management Kanban tool visualises the operational workflow and the actual work being carried out in the process. By identifying the bottlenecks in the processes and helping to fix them, the Kanban framework ensures smooth operations at Throughput and lower delivery Lead times.
History of Kanban Systems
The Kanban system was introduced by Taiichi Ohno at Toyota Automotive, Japan,
in the 1940s. Ohno tried eliminating the overproduction by introducing new inventory only when
it was absolutely necessary. The factories were reorganised to make the production and assembly
of the parts happen at the same rate- the Just in Time method. He introduced paper-based
physical Kanban boards where the cards could be sent back to the production of the parts once
the material was used, and this would indicate to the team what material was used and how many
more should be restocked.
Kanban systems evolved to control the entire value chain from the supplier to the end user. By
utilising the Kanban system for inventory management, supply disruption and overstocking were
avoided at every stage of the manufacturing process. The Kanban system thus became popular in a
variety of production environments. Over time, Kanban lean manufacturing started being used in
different industries that needed to visualise a large volume of Work in Progress.
Kanban Principles
Kanban Change Management Principles include :
-
Start With What You Do Now:
The existing workflows, systems, processes and things already in place are not disturbed. Kanban is directly applied to the current workflow. With minimum disruption, the issues to be addressed and need plan changes are addressed gradually over a period of time at the pace the team is comfortable with. -
Agree to pursue Incremental, Evolutionary Change:
Designed to cause minimal resistance, Kanban boards encourage small, continuous, incremental changes in the currently running process. Significant changes in the process flow are discouraged, as they may be highly resistant and likely to be hard to implement. -
Respect the Current Processes, Roles, Responsibilities and Job Titles:
Kanban does not implement organisational changes, so changing the existing roles and processes may not be required. Team collaboration can identify and implement the changes as needed. -
Encourage leadership acts at all levels in the organisation:
Kanban view encourages team members to collaborate, take ownership of issues, and address them accordingly. Through a culture of safety, Kanban allows the team to take the lead in actions, fix issues, and grow professionally.
Kanban Practices
Carefully executing these steps can help you implement the Kanban method in your organisation.

-
Visualise the Workflow:
Kanban systems visualise workflow with the help of a Kanban board with Kanban cards and Kanban columns. Each Kanban column on the Kanban board represents a step in the workflow, and each card represents a work item for which the task status is easily understood. The digital Kanban board forms the visual representation of the actual workflow of the processes with all its risks and specifications. Kanban boards can vary from simple to complex, depending on the operational complexity. A Simple Kanban board contains three stages: To Do, In Progress, and Done. This sequence across the work stages is referred to as the workflow. The Kanban system visualises the work items, its flow and the business risks. Moving from left to right in the Kanban board gives an idea about workflow stages. By examining the details of each card and monitoring the process status, businesses can visualise risks and identify bottlenecks within the workflow stages, streamlining workflow management and mitigating potential obstacles. -
Limit Work in Progress(WIP):
Understanding the fact that switching the team's focus half way through can harm their productivity and multitasking is not going to do any good. Limiting the Work in Progress (WIP) ensures that the right amount of Kanban cards are on the Kanban board and that the available resources can handle the right amount of work. This can be achieved by implementing a pull system where the new work is only pulled when there is enough Kanban capacity to deal with it. For the proper working of it, limits to the Work in Progress (WIP) should be set and adjusted accordingly. Thereby Kanban view ensures that only a manageable number of active items are in progress at any point of time. No WIP, no Kanban flow. Setting the number of work items or tasks per stage helps them manage the pulling of the Kanban cards in the subsequent step when there is an available capacity. -
Manage Flow:
Managing the flow refers to moving work items across the production processes, as represented in the Kanban board, at a predictable and sustainable pace. To create a smooth and healthy workflow, the workflow should be managed with visibility on blocks, bottlenecks, and risks. Instead of micromanaging the people and keeping them busy all the time, the work process should be managed so that the workflow is efficient and moves faster through the system. Blocked cards indicate blocked tasks on the workflow, which could impact the subsequent workflow stage or project delivery. -
Make the policies explicit:
Understanding something can help improve it. To do this, you need to define your process, publish it, and socialise it. When the team's common goals are defined, it becomes easier for them to work towards them and make progress. The Kanban explicit policies can guide your workflow and enhance decision-making. -
Feedback Loops:
Gathering feedback at different process stages ensures that the organisation adequately responds to potential changes and enables knowledge sharing between stakeholders. However, without clear communication channels, your team may miss important feedback. Therefore, implementing team-level Kanban cadences or Kanban meetings is essential to facilitate structured discussions and feedback loops. Kanban meetings can be tailored according to the context, team size, or discussion topic, fostering a collaborative environment and ensuring that all voices are heard. -
Improve Collaboratively:
Implementing changes using Kanban board software, feedback, and Kanban metrics can continuously improve an organisation. Tracking metrics like Throughput and Lead Time can identify bottlenecks, streamline workflows, and enhance overall efficiency, leading to sustained improvements in performance and productivity.
Kanban Board features and components
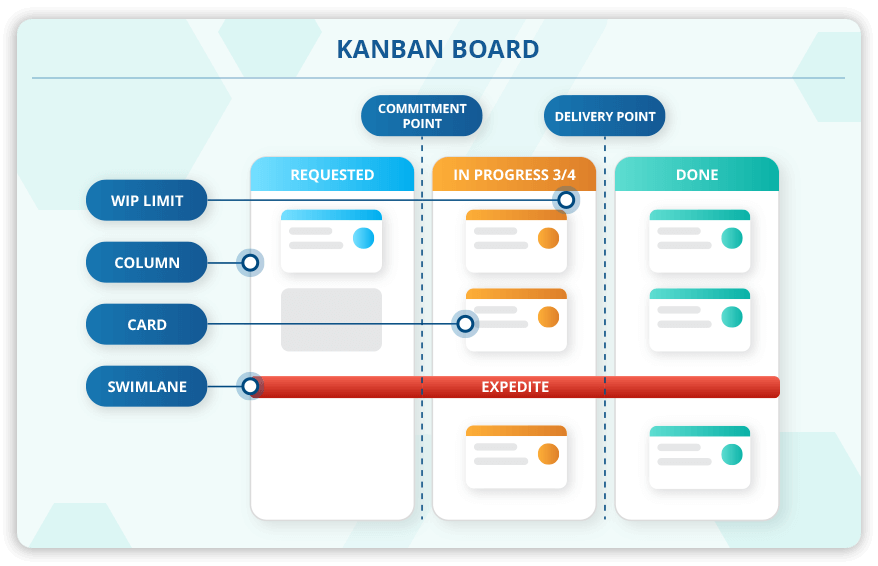
David Anderson identified five key components of Kanban boards: Visual signals, Columns, Work-in-Progress (WIP) limits, a Commitment point, and a Delivery point. Kanban Cards are visual signals that depict various tasks. Additionally, Kanban Swimlanes help organise tasks and enhance visual clarity.
-
Kanban Cards:
A visual representation of tasks, the Kanban cards contain information about the tasks, such as to whom is assigned, the deadline and the task description. -
Kanban Columns:
The Kanban column on the board represents the different stages in the workflow. Every Kanban card goes through these workflows until they are completed. -
Work in Progress Limits:
WIP limits restrict the number of tasks in the different workflow stages. By helping the teams focus on the current tasks and not overloading them helps to finish the tasks faster and more effectively. -
Kanban Swimlanes:
These horizontal lanes help organise similar tasks and visually separate the different work types. -
Commitment Point:
The work item in the work process is ready to be pulled into the system at this point. -
Delivery Point:
The final stage in the workflow where the work items are considered completed.
Experience your Kanban Features here !
Types of Kanban Boards
-
Physical Kanban Boards:
Physical Kanban board is the basic version of the Kanban board where the teams use paper cards representing the tasks on a whiteboard. As the work progresses, the cards placed in the work stages represented by the columns move from one stage to the next. -
Digital Kanban Boards:
Kanban software possesses additional features than physical Kanban boards. By bringing more visibility into work progress, the digital Kanban boards are accessible virtually from anywhere, anytime. These platforms also provide the flexibility of tracking multiple workflows in different categories and organising them accordingly.
Top 5 benefits of using a Kanban board
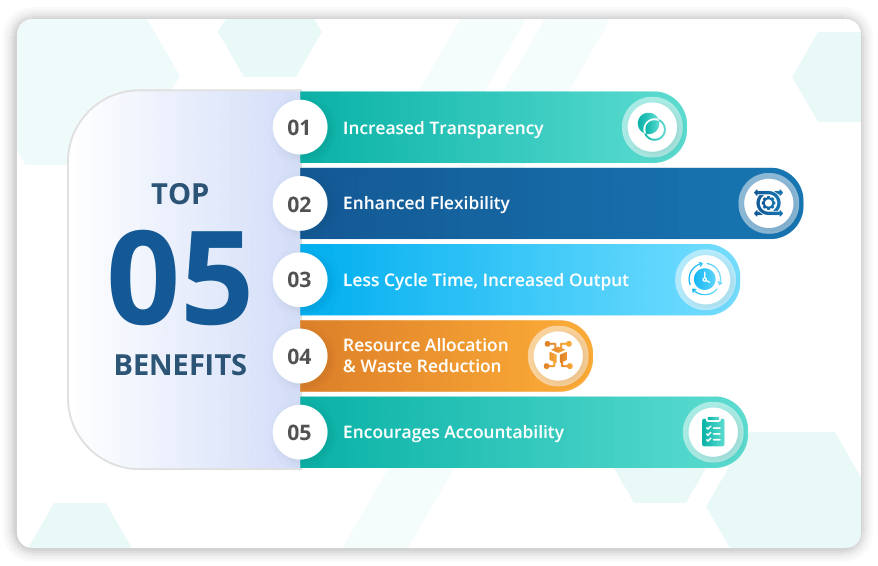
-
Increased transparency:
The visual representation of the work progress helps the teams better understand the workflow and progress. Team collaboration and team communication get better. Kanban boards also help identify roadblocks slowing down the processes and improving the team's productivity. -
Enhanced Flexibility:
Kanban boards focus on the task in progress and add work only according to the capacity allocation. Kanban boards, thus, can be introduced without disrupting the existing workflow and processes that are running successfully. The Kanban software offers easy configuration options, allowing the team to evaluate the strategies and improve workflow. The board evolves as the process evolves. -
Less Cycle time, increased output:
In the Kanban system, everyone in the team is responsible for a smooth workflow throughout the process. Cycle Time in Kanban refers to the amount of time elapsed between the start and end of the task. Optimising the cycle time can help the team adjust the work accordingly, and the team's productivity is increased. -
Resource Allocation and Waste Reduction:
Kanban, a lean tool, is often associated with resource allocation and waste reduction. The visibility into the workflow helps make it easier to identify how the team members are performing and understand the wasteful processes and bottlenecks. -
Encourages Accountability:
The Kanban board displays the deliverable state of the task, the task dependencies and the completion date. This increases the accountability of the process by moving the tasks across the board by listing who is working on what and how much has been completed is visible to everyone involved in the project.
How to create a Kanban Board?
-
step 1
Create a basic Kanban board version.
Choose the best Kanban board software that aligns with your organisational goals and processes. Name your Kanban board and create columns with TO DO or READY TO START, IN PROGRESS and DONE.
TO DO/ READY TO START - This column lists all the committed work orders.
IN PROGRESS - The work items move to this list from the TO DO list once the team commits to completing the task.
DONE - All the completed work orders are listed here in the Kanban cards.
The Commitment Point in the board illustrates the point in your work processes where the teams signal whether the work is ready to be started.
-
step 2
Define and Map the Workflow.
Map all additional columns that will further define your workflow, and these columns will mirror the organisation's workflow step by step. Choose the Kanban columns through which the work items are likely to move, and this should make sense to the team. Identification of the problems can be made easy with this. Let's look at this with an example: Moving the task's progress from In Progress to Waiting creates an additional step that shows the task needs to take additional steps or needs further action.
-
step 3
Visualise all the Work.
Visualising with the help of a Kanban card or note represents every work item on the Kanban board. Every assignment that should be done but not yet started can be listed in the Backlog column. This way, Kanban boards visualise all the works.
-
step 4
Work Policies made clear.
For the proper functioning of every Kanban board, you need to establish the rules for executing the process. Making these policies and guidelines visible to everyone and keeping them in an accessible place will make it easier for the team to understand. This helps establish a common understanding of using the work categories, defining when the new work will be starting, when a task needs to be completed in the Kanban process etc.
Do not rush to overdo this. Make sure only a few work policies are created the first time. By defining and keeping your policies simple, you can make them visible and open for discussion and continuous improvement. -
step 5
Adding Work in Progress(WIP) Limits.
In the Kanban system, there is a continuous flow of work. To ensure a smooth workflow, the capacity to do the work must be considered. By limiting the WIP, a limit is placed on the capacity of a column on the Kanban board. The more work items in the process, the slower the delivery becomes. For instance, you can define that one person should not be working on more than the assigned task at the time. Before finishing this work, he must not accept any more item in the column as it exceeds his WIP limits. Limiting WIP also counts the number of pending or unfinished items on the list before accepting new ones.
-
step 6
Feedback friendly atmosphere.
As time changes, the Kanban process also evolves or changes accordingly. Being open to the team and the stakeholder's suggestions can help you understand these changes and adjust your Kanban flow accordingly.
Create your Kanban Board
Now !
Kanban in Lean Manufacturing
In lean manufacturing processes, Kanban is a scheduling system utilised to optimise production and minimise waste, playing a pivotal role in the Kanban lean manufacturing practices. The Kanban tool facilitates Just-in-Time (JIT) production, ensuring what is needed is produced when needed and in the required quantity. In manufacturing, Kanban approach minimises waste, reduces inventory levels, and enhances efficiency and quality. The Kanban production system involves each work centre or production cell having a card or signal indicating when more parts or materials are required. These signals prompt upstream work centres or suppliers, helping implement Kanban scheduling boards to produce and deliver the necessary components to downstream work centres. In operations management, Kanban guarantees the timely availability of the correct parts and materials, mitigating overproduction and excess inventory. It fosters continuous improvement by identifying bottlenecks and aligning with Kanban and lean principles. Kanban is a cornerstone tool in the lean manufacturing toolbox, contributing to streamlined operations and enhanced competitiveness. Additionally, the Kanban tool's compatibility with agile methodologies further highlights the value in modern production environments and supply chain management.
How to choose the right Kanban Board Software?
Choosing the best kanban board software for your organisation is really important for any team looking to adopt the Kanban methodology. Here are some factors to consider when selecting the right Online Kanban board software or Free kanban boards.
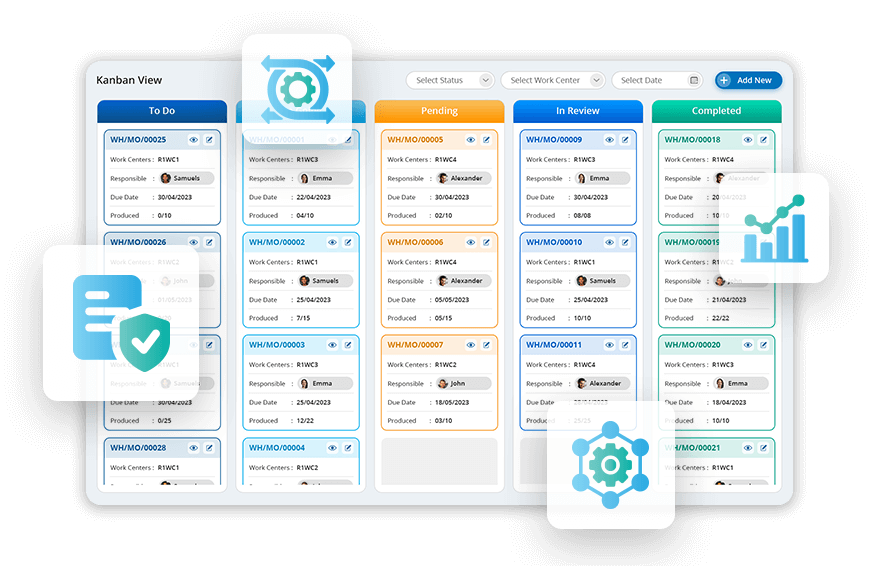
-
User Interface and Ease of Use:
The Kanban software should have a user-friendly interface that is easy to navigate and use, with a clean and organised layout. -
Customisation options:
Kanban templates, including Kanban card template and Kanban board template, serve as foundational tools for organising tasks and managing workflow effectively. Customisation options are crucial in optimising Kanban templates to align with your team's unique requirements. Look for a Kanban software that allows you to customise your Kanban board tool to meet your team's specific needs, which includes adding custom fields, Kanban swimlanes, or columns, ensuring seamless adaptation to your workflow processes. -
Integration with other tools:
If your team uses other project management tools or software, choosing a Kanban board software that integrates with those tools is essential. Kanban online systems avoids duplicate data entry and streamlines your workflows. -
Collaboration features:
Kanban approach is all about teamwork, so choosing software with collaboration features such as real-time updates and notifications is important. -
Analytics and reporting:
To track progress and make data-driven decisions, analytics and reporting features are a must. Look for a Kanban software that provides useful Kanban metrics and Kanban reports. -
Security and data privacy:
Make sure your chosen Kanban software meets your company's security and data privacy standards. This includes data encryption, secure login, and access control. -
Pricing and licensing:
Finally, consider the pricing and licensing options of the software. Look for a Kanban software that fits your budget and offers flexible licensing options.
Considering these factors, you can choose the right Kanban board online software for your team and get the most out of your Kanban implementation.
How can the Kanban board affect your ROI?
A task manager Kanban has many applications and can positively impact your ROI (Return on Investment) in several ways:
-
Increased productivity:
eKanban (electronic kanban) board helps teams to visualise their workflow and identify bottlenecks, which leads to an increased productivity with faster delivery of projects and a higher ROI. -
Improved communication:
The use of a Kanban board tool enables team members to improve their communication and collaboration with one another. Improve your Return on Investment with a better understanding of project goals and faster resolution of issues. -
Reduced waste:
Identifying the areas of waste and inefficiencies in the workflow can help the teams to eliminate the waste, reduce costs and improve ROI. -
Better resource utilisation:
With a to-do list Kanban, teams can identify the most important tasks and prioritise accordingly. This helps to optimise resource utilisation, leading to better ROI. -
Increased customer satisfaction:
The Kanban board used in project management helps teams deliver projects faster and with higher quality by visualising and tracking the workflow. Thus, the Kanban application in workflows increases loyalty and customer satisfaction, positively impacting ROI in your organisation.
How does Online Kanban Board help remote or distributed teams?
The implementation of an online Kanban board with swimlanes revolutionises the efficiency of remote or distributed teams. By utilising a virtual Kanban system, teams can seamlessly collaborate and manage tasks regardless of geographical location. An online Kanban board offers real-time visibility into task status, ensuring transparency and alignment among team members. The electronic Kanban board task management facilitates easy progress tracking, identifying bottlenecks, and prioritising work items. A digital Kanban board with swimlanes can categorise tasks based on various criteria, facilitating better organisation and workflow management. Adopting an online Kanban board tool enhances communication, fosters teamwork, and ultimately boosts productivity for remote or distributed teams. Additionally, a Kanban app or Kanban board app helps teams use Kanban software from any device, anywhere, establishing a consistent Kanban flow.
How does a Kanban Board work?
The physical Kanban board works by mapping the individual work items to the sticky notes placed into the vertical columns on a large white or black board. The columns on the board represent different stages of the workflow, such as "To Do," "In Progress," and "Done." As tasks progress, their corresponding cards or sticky notes are moved across the columns by a responsible team member, providing a clear and immediate visual representation of progress, bottlenecks, and workload distribution.
Digital Kanban boards visually represent tasks as Kanban cards that move through workflow stages or Kanban stages using drag-and-drop functionality . They provide real-time updates, manage access, support integration, calculate Kanban metrics, and generate Kanban reports. Operating as a pull-based system with WIP limits, they ensure efficient workflow and continuous improvement. This is how a digital Kanban board works:
-
Visual Representation:
Tasks and work items are represented as Kanban cards. Each card should contain essential information, such as a task description, due date, assignee, and any relevant attachments or links. -
Progress Tracking:
Kanban Cards are moved through lanes representing Kanban stages of the workflow. -
Drag-and-Drop Functionality:
Drag and drop Kanban cards from one Kanban column to the next as work progresses. For example, a task can move from "To Do" to "In Progress" and eventually to "Done." -
Real-Time Updates:
The online Kanban board tool provides real-time updates so team members can see changes instantly. This is particularly useful for remote or distributed teams. -
Access Management:
Setting up of the user privileges enhances the task management. -
Integration with other Systems:
Integrate your virtual Kanban board with other tools and services you use, such as project management software, calendars, and file-sharing platforms. This streamlines your workflow and reduces manual data entry. -
Automatic Metrics Calculation:
Tracks important Kanban metrics like Throughput and Lead Time. -
Insightful Kanban Reports:
Provides reports for identifying bottlenecks and monitoring performance. -
Pull-Based System:
Work is pulled based on demand to maintain a steady workflow. Team members should only pull work into the "In Progress" column when they can work on it. This ensures that tasks are started and completed at a sustainable pace. Once the team completes their current tasks, they can select the next task from backlogs and avoid waiting time. -
WIP Limits:
Limit the number of Kanban cards allowed in the "In Progress" column to prevent overloading team members and maintain a smooth workflow. Adjust this limit based on your team's capacity. -
Collaborate and Communicate:
Use the comments and notes on Kanban cards to facilitate collaboration and communication. You can discuss tasks, ask questions, and provide updates directly on the Kanban cards.
Get Started with Kanban Board
Kanban List View
A Kanban list view serves as a helpful visual summary of records, providing a clear overview of items in progress and facilitating effective work monitoring. It enables users to easily update a record's status by employing drag-and-drop functionality, streamlining workflow management. This intuitive approach enhances task visibility, promotes collaboration, and fosters efficient tracking of work items, ensuring teams stay organised and productive. Kanban list views are valuable in project management, task tracking, and process improvements across various industries and operations.
Workflow Management with Kanban
Kanban workflow management emphasises continuous delivery and flexibility in the development process to deliver a service or product efficiently. It involves visually managing tasks as Kanban cards, which are moved through different workflow stages using drag-and-drop functionality on a digital Kanban board. Real-time updates, access management, integration of other project management tools, and automatic metrics calculation enhance the Kanban system's effectiveness. By operating as a pull-based system with Work-In-Progress (WIP) limits, the Kanban method ensures a smooth, uninterrupted flow, enabling teams to identify and resolve bottlenecks quickly, thus maintaining a steady and efficient workflow.
How do I create a Workflow in Kanban Board?
Creating a Kanban workflow involves setting up a visual system for managing and tracking work progress. Kanban methodology can be adapted to various situations, whether you're managing software development, manufacturing, marketing, or any other project. Here are the steps to create a Kanban workflow:
- Understand the Basics of Kanban: Before you start, ensure you understand What is a Kanban, Kanban's core principles, which include visualising work, limiting work in progress (WIP), making process explicit policies, and continually improving.
- Identify your Kanban Processes: Clearly define the process you want to manage with Kanban dashboard. This could be software development, customer support, marketing campaigns, or any other workflow.
- Visualise Your Workflow: Create your workflow visual representation with a physical kanban whiteboard or using digital Kanban tools. The basic structure includes columns that represent different stages of your process. Common columns have "To Do," "In Progress," and "Done," but you can customise them to fit your process.
- Create Work Items (Kanban Cards or Tickets): A Kanban card or ticket should represent each task or work item in your process. These cards should be placed in the appropriate column on your virtual Kanban board based on their current status in the workflow.
- Set WIP Limits: Determine the maximum number of work items in progress at each workflow stage. This helps prevent overloading and bottlenecks.
- Manage and Prioritise Work Items: As work progresses, move cards from one column to the next in the Kanban dashboard. Ensure that you prioritise work items and pull new items into the "In Progress" column only when there's available capacity, as per your WIP limits.
- Visualise Blockers and Issues: Use visual cues like red flags or specific symbols to indicate blockers or issues that need attention. This allows for quick problem identification and resolution.
- Regularly Review and Improve: Hold regular virtual Kanban board review meetings to discuss the work's state and identify improvement areas. Continuous improvement is a fundamental aspect of Kanban planner.
- Make Policies Explicit: Document the policies and rules that govern how work moves through the eKanban system. This makes expectations clear for everyone involved.
- Use Metrics and Analytics: Measure and analyse your workflow using metrics like lead time (the time it takes to complete a work item) and cycle time (the time it takes to move a work item from one stage to another). This data can help you make informed decisions and further optimise your process.
- Adapt and Evolve: Be open to making changes based on feedback and data analysis. The task manager Kanban is all about adaptability and continuous improvement.
- Train Your Team: Ensure that the team understands what is a Kanban board, the Kanban process and its principles. Provide training and support as needed.
Remember that a Kanban workflow should be tailored to your needs and continuously improved based on your team's experiences and feedback. It's a flexible approach that can be adapted to fit various processes and industries.
Start Mapping Your Workflow in Kanban
Personal Kanban
Personal Kanban is a simplified version of the Kanban methodology designed for individual use. It helps individuals manage their tasks and work visually and efficiently. Personal Kanban improves productivity, prioritises work, and reduces stress. A Kanban board for personal use is a simple and effective way to manage your work, increase visibility into your tasks, and reduce the feeling of being overwhelmed by your to-do list. Kanban planner encourages a continuous improvement mindset and helps you increase productivity while reducing stress.
What Metrics can be tracked and measured using Kanban Tool?
- Throughput: Measures the rate at which tasks are completed over a specific time period, indicating the team's productivity and efficiency.
- Lead Time: The duration from task initiation to completion provides insights into the workflow's overall efficiency and helps identify improvement opportunities.
- Cycle Time: The time taken to complete a single task from start to finish, highlighting the efficiency of individual processes and aiding in workload management.
- Work-In-Progress (WIP): Tracks the number of tasks currently in progress, ensuring that team members do not overload themselves and helping maintain a balanced workflow.
- Queues: Monitors the number of tasks waiting to be processed at each stage of the workflow, identifying potential areas of congestion and opportunities to streamline the process.
How do you Track Progress in Kanban?
Tracking progress using the Kanban tool is crucial for maintaining efficiency and ensuring continuous improvement in workflow processes. By monitoring key metrics and visualising task progress in the Kanban dashboards, teams can quickly identify bottlenecks, balance workloads, and make informed decisions to enhance productivity. Using Kanban Charts, such as Cumulative Flow Diagrams and Cycle Time Scatter Plots, teams can easily visualise progress in their workflow and generate Kanban reports, pinpointing improvement areas. Additionally, the Kanban timeline enhances clarity in due dates and manages workflow accordingly, ensuring tasks are completed on time and facilitating effective resource management. Let's understand more on the Kanban charts and Kanban timeline used for measuring productivity:
-
Cumulative Flow Diagrams:
These diagrams visually represent the number of tasks in each workflow stage over time, helping identify bottlenecks and ensuring a steady workflow. -
Cycle Time Scatter Plot:
This chart displays the time taken to complete individual tasks, allowing teams to analyse variations and trends in cycle times, thus identifying areas for improvement. -
WIP Chart:
The Work-In-Progress (WIP) chart tracks the number of tasks in progress at any given time, helping teams maintain WIP limits and ensuring a balanced workflow. -
Distribution Chart:
A distribution chart shows the distribution of tasks across different workflow stages, providing insights into workload distribution and helping to balance team efforts. -
Block Resolution Chart:
This chart tracks the number and duration of task blockages, helping teams understand and address the causes of workflow delays. -
Kanban Timeline:
A timeline view of tasks that provides a chronological perspective, helping teams track progress, get a sense of schedule, forecast completion dates with start and end dates, and plan future work efficiently.
What is the difference between Cycle time and Lead time in Kanban?
Kanban Lead Time and Kanban Cycle Time are two essential metrics used in Kanban to measure and analyse the flow and efficiency of work within a system. These metrics provide insights into how long it takes for a work item to move through a process and help identify bottlenecks and areas for improvement.
-
Kanban Lead Time:
Kanban Lead Time, also known as "Lead Time" or "Delivery Time," is the total time it takes for a work item to move from the moment it's requested or enters the Kan ban system until it's completed and delivered to the customer or stakeholder. Lead Time starts when a work item is added to the "To-Do" or the first column on the Kanban board and ends when it is marked as "Done" or reaches the final stage. Lead Time is a customer-centric metric that helps set realistic expectations for delivery times. It measures the end-to-end time from request to delivery, which is valuable for assessing customer satisfaction and predicting delivery times. -
Kanban Cycle Time:
Kanban Cycle Time is the time it takes for a work item to move through the active or working stages of a Kanban process. It excludes any time spent waiting or in queues. Cycle Time measures the time a task is being actively worked on. It is typically calculated as the time from when the work item enters the "In Progress" column until it reaches the "Done" column. Cycle Time is a process-centric metric that helps teams identify bottlenecks and inefficiencies in their workflow. It helps make process improvements and optimise the flow of work. Reducing Cycle Time often leads to improved productivity.
Kanban Reports
Kanban reports are essential for visualising and analysing workflow or Kanban data to support decision-making and process improvement. Kanban reports, generated from Kanban boards, provide insights into key metrics such as throughput, cycle time, and work-in-progress. The Kanban reporting feature enables teams to track progress, identify bottlenecks, and optimise workflow efficiency. Kanban meetings often utilise these reports to facilitate discussions on performance, prioritise tasks, and adjust the workflow as needed, ensuring continuous improvement and alignment with organisational goals.
How to use Kanban Boards?
Kanban boards are versatile tools for visualising, managing, tracking and optimising workflows in various contexts, from software development to personal task management. Here's how to use Kanban boards effectively for task management:
-
Understand Your Workflow:
Start by clearly defining the stages and steps of your workflow. Understand how work moves from the initial request or idea to completion. This is the foundation of your Kanban task board. -
Visualise Workflow Stages:
Arrange kanban cards representing tasks into Kanban columns representing different work stages, providing clarity on task progress. -
Identify and Address Workflow bottlenecks:
Monitor task flow through the Kanbanboard to pinpoint areas where tasks accumulate, allowing for timely intervention and optimisation. -
Utilise the Kanban board to set WIP limits:
Establish limits on the number of tasks allowed in progress at each stage to prevent overloading and ensure steady workflow progression and focus. -
Save time by using the Kanban Dashboard:
Display key metrics and task statuses on the kanban dashboard, enabling quick access to information and reducing the need for lengthy status update meetings. -
Visualise and Address Work Blockers promptly:
Prioritise tasks that are or are blocked and are visualised as blocked cards, facilitating swift resolution to keep workflow moving smoothly. -
Automate Work Processes on your digital Kanban Board:
Integrate automation tools or workflows to streamline repetitive tasks and enhance overall efficiency, allowing teams to focus on higher-value work. -
Regularly Review and Reflect:
Periodically review your Kanban task board. Ask questions like:- Are tasks moving smoothly through the workflow?
- Are there bottlenecks or delays?
- Is the team adhering to WIP limits?
- Are priorities being managed effectively?
-
Adapt and Improve:
Use your reflections to make adjustments to your Kanban system. If you consistently face specific issues or find your WIP limits too high or low, adapt your process accordingly. -
Complete and Archive:
When a task is finished, move it to the "Done" column. After a while, you can archive or remove completed tasks from the board to keep it clean and focused. -
Collaborate and Communicate:
Use your Kanban planner as a tool for team collaboration and communication. Team members can see the status of work items and help address issues as they arise. -
Stay Flexible:
Kanban is all about flexibility. It allows you to adapt to changing priorities and manage your workload effectively. -
Feedback Loop:
Gather feedback from team members and stakeholders about the efficiency and effectiveness of the Kanban board and use this input to make improvements.
Kanban task boards can be used in various contexts, from software development to project management and personal productivity. The key is to tailor your Kanban system to your specific needs and continually improve it based on your experiences and feedback.
Kanban Template
A Kanban template is a structured tool designed to facilitate the implementation of Kanban methodology in managing workflows. A Kanban board template provides a visual framework for organising tasks into columns such as "To Do," "In Progress," and "Done," ensuring clarity and transparency in project management. Within this board, a Kanban card template helps detail individual tasks, including descriptions, assignees, deadlines, and progress status. Using a Kanban template streamlines task management, enhances team collaboration, and improves productivity by providing a clear overview of work stages and ensuring that tasks move smoothly through the workflow.
Download Kanban Board Template
Kanban Visual Systems
Kanban visual systems utilise visual cues such as Kanban cards and Kanban boards to represent tasks and workflow stages, providing a clear and intuitive way to manage work processes. By visually organising tasks and workflow stages using a Kanban project management tool, teams can easily track progress, identify bottlenecks, and prioritise tasks effectively. Kanban visual systems promote transparency, collaboration, and efficiency, enabling teams to optimise their workflow and deliver high-quality results consistently.
Kanban Project Management
Kanban project management software emphasises efficiency and flexibility in managing project schedules across various industries such as manufacturing, healthcare, automotive, construction, electronics, energy, hospitality, HVAC, plant hire, pharmaceuticals, FMCG, IT, government, and more. Utilising a Kanban timeline, teams can visualise project timelines, track progress, and ensure the timely completion of tasks. Project schedules are effectively managed through Kanban boards, where tasks are represented as Kanban cards and organised according to priority and workflow stages. Card timers are employed to track the time spent on individual tasks, enabling teams to optimise their time management strategies and improve productivity. Kanban planning and Kanban task management are integral components, allowing teams to structure their work efficiently and adapt to changes seamlessly. With Kanban's focus on continuous improvement, teams can implement effective Kanban management strategies to enhance workflow efficiency and project outcomes.
Kanban Inventory Management
The Kanban system for inventory management is a lean approach that enables businesses to optimise inventory levels and minimise waste. By implementing a Kanban inventory system, companies can establish visual signals, or Kanban cards, to replenish inventory items as they are consumed. The Kanban inventory system ensures that inventory levels are aligned with actual demand, preventing overstocking or stockouts. With Kanban inventory management, businesses can improve efficiency, reduce carrying costs, and enhance overall supply chain performance through continuous monitoring and replenishment of inventory based on actual usage and demand signals.
Kanban Board Examples
Kanban boards come in various forms and can be adapted to suit your team's or project's specific needs. Here are some common Kanban board examples to give you an idea of how they can be structured:
-
Basic Kanban Board:
This is a simple Kanban board with the primary three columns. Tasks move from "To-Do" to "In Progress" and finally to "Done" as they are completed.
- Columns:To-Do, In Progress, Done
- Cards:Task cards representing individual work items.
-
Personal Kanban Board:
Personal Kanban boards are often used for managing individual tasks and daily priorities. The simplicity of this board is well-suited for personal use.
- Columns:To-Do, Doing, Done
- Cards:Personal tasks and commitments.
-
Software Development Kanban Board:
A Kanban board for software development typically includes more stages, reflecting the various steps in the development process, including code review and testing.
- Columns:Backlog, Ready, In Progress, Code Review, Testing, Done
- Cards:User stories, bugs, features.
-
Marketing Campaign Kanban Board:
A marketing campaign board reflects the various stages of planning and executing marketing initiatives.
- Columns:Ideas, Planning, Design, Copywriting, Review, Approval, Publishing, Analysis
- Cards:Marketing tasks, ad campaigns, content creation
-
Manufacturing Kanban Board:
A Kanban board can help visualise the production planning and master production schedule from raw materials to shipment in manufacturing.
- Columns:Raw Materials, In Production, Quality Control, Packaging, Ready for Shipment
- Cards:Product orders, inventory items
-
Service Desk Kanban Board:
Service desk teams use Kanban boards to manage and track customer support requests and incidents.
- Columns:New Requests, In Progress, Waiting for Customer, Resolved, Closed
- Cards:Customer support tickets
-
Content Creation Kanban Board:
Content teams can use Kanban boards to streamline the creation and publication of content.
- Columns:Ideas, Research, Writing, Editing, Review, Design, Publishing, Promotion
- Cards:Blog posts, articles, videos, social media updates
-
Agile Kanban Board (with Epics and Stories):
Agile project management with Kanban allows agile development teams to manage high-level Epics and granular User Stories in a single workflow.
- Columns:Backlog, Ready, In Progress, Code Review, Testing, Done
- Cards:Epics (more significant initiatives) and User Stories
-
Event Planning Kanban Board
Event planners can use Kanban task boards to organise and execute event planning tasks.
- Columns:Idea, Planning, Venue Booking, Marketing, Execution, Evaluation
- Cards:Tasks related to event planning
-
Research Project Kanban Board
Researchers can utilise Kanban to manage the complex process of research projects.
- Columns:Research Proposal, Data Collection, Analysis, Report Writing, Review, Presentation
- Cards:Research tasks, data analysis, and report writing tasks
-
Scrum Kanban Board
Scrumban board combines Kanban's flexibility with Scrum's structured planning, facilitating efficient workflow management and task prioritisation throughout the project schedule.
- Columns:Product Backlog, Sprint Backlog, To-Do, In Progress, Testing
- Cards:User Stories, Bugs, Enhancements
Remember that these are just examples, and you can customise your Kanban task board to match your specific workflow, industry, or team's needs. The key is to create a visual representation of your work and process that helps you manage, track, and optimise your tasks effectively.
Enhance Operational Efficiency with LTS Digital Kanban Boards
LTS Kanban Boards revolutionise production and workflow management with its intuitive digital solution, seamlessly integrating with Lean and Just-in-Time methodologies to optimise operational processes. Visualise production workflows, track inventory levels, manage supply chains, and empower your team to identify bottlenecks, prioritise tasks efficiently, and enhance overall operational efficiency. Explore a comprehensive suite of features including Work Order Management, Digital Work Instructions, Quality Inspections, Asset Management, Virtual Gembas, Project Management, Scheduling and Resource Management, Manufacturing Workflow Management, Process Confirmation Audits, Lean Daily Management System and Leader Standard Work. Elevate your operational excellence today with industry-focused LTS Digital Kanban Boards.
Know more about Kanban Applications And Processes
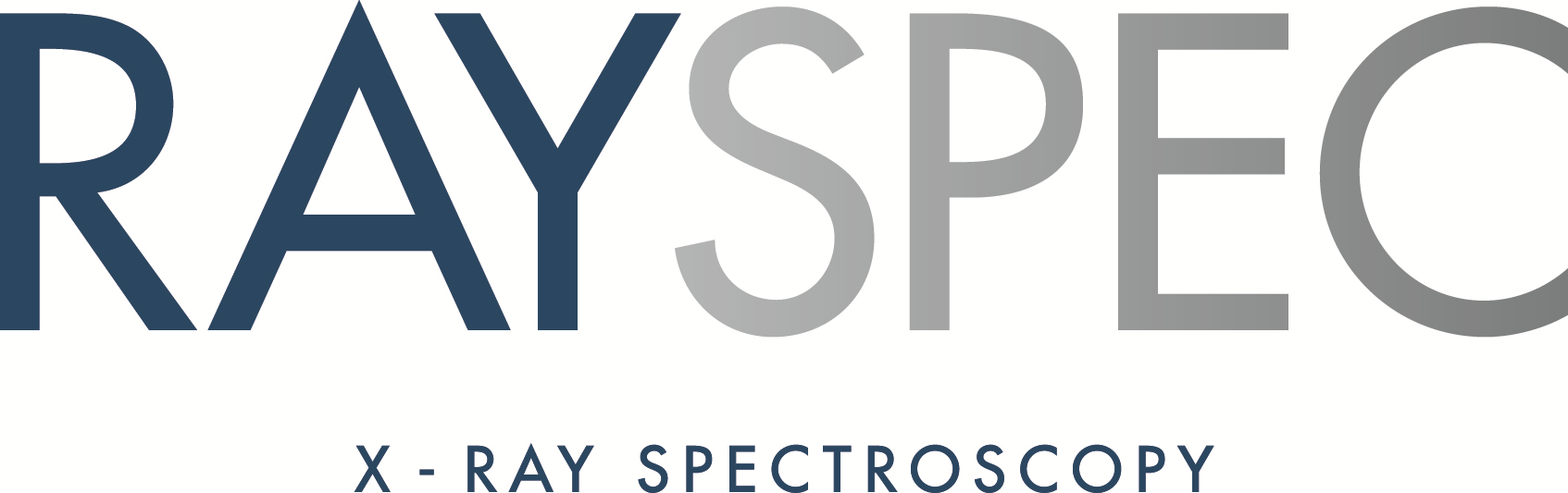
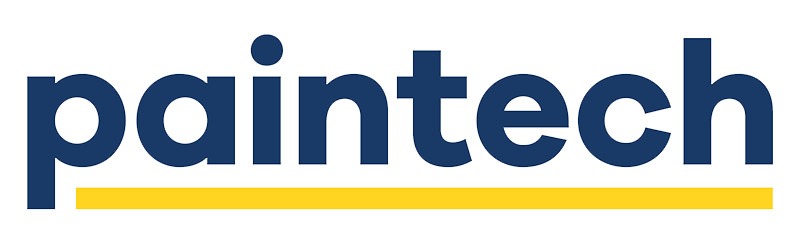
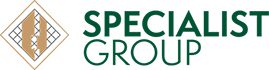
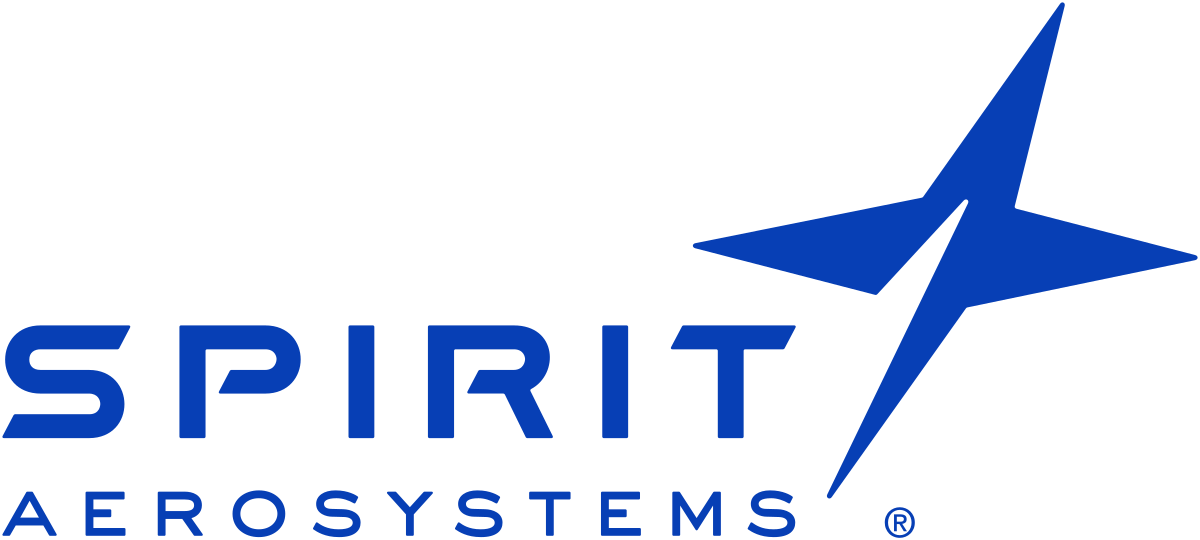
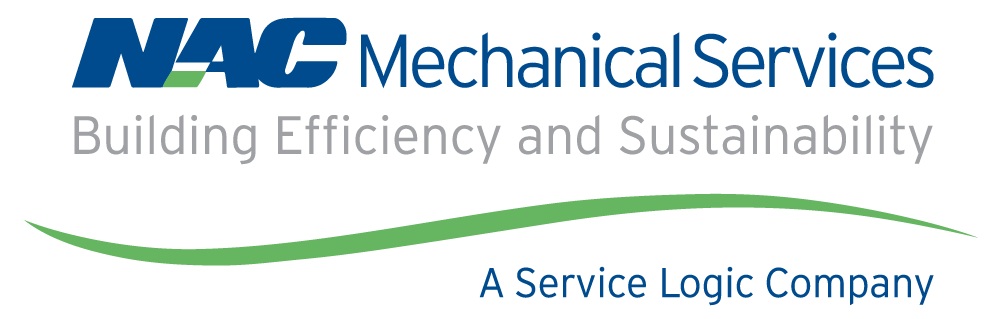
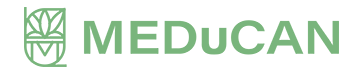

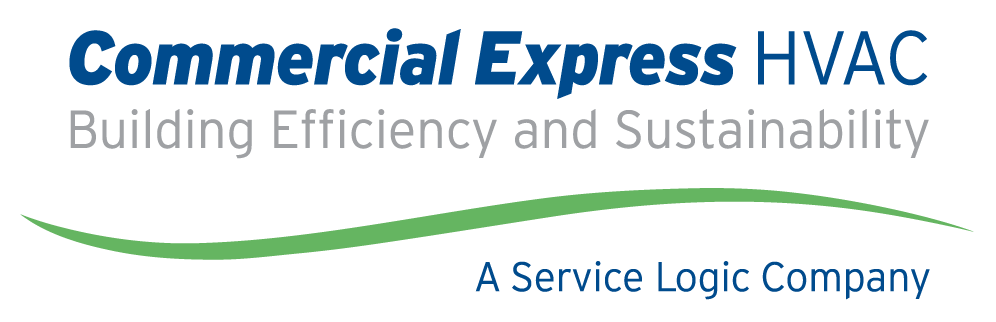
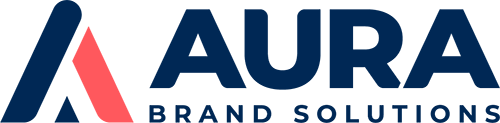
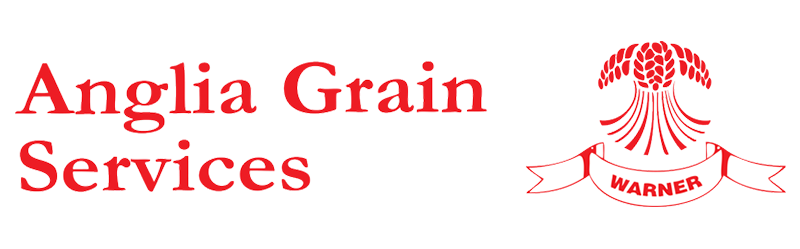