Mapping Value Streams with a Kanban System
Kanban boards can effectively visualise and analyse your entire value stream, from production to product delivery.
Start Free Trial Watch VideoContents
- What is meant by Value Stream Mapping?
- What is Kanban in Value Stream Mapping?
- Why use Kanban for Value Stream Mapping?
- How to create a Value Stream Map using a Kanban board?
- What are the key benefits of using Kanban for Value Stream Mapping?
- Five best tips for implementing Kanban in Value Stream Mapping
- Why integrate Kanban with Value Stream Mapping for process improvement?
- Is Kanban a versatile tool applicable across diverse industries for Value Stream Mapping?
- How can Kanban boards be customised to fit the unique needs of my value stream?
- What should you do before transitioning to a Kanban-based Value Stream Mapping system?
- Overcoming common challenges faced while implementing Kanban for Value Stream Mapping
- Differences between Traditional Value Stream Mapping and Kanban approach in Value Stream Mapping
What is meant by Value Stream Mapping?
VSM (Value Stream Mapping) is a lean management approach to visualise, analyse, and optimise the information flow and materials throughout production. This strategic tool employs visual mapping to identify and eliminate inefficiencies, reduce waste, and enhance overall process efficiency. By capturing key data sources, such as lead times and cycle times, Value Stream Mapping provides a complete overview of the current state of operations, facilitating continuous improvement efforts and helping organisations achieve a more streamlined and customer-centric production workflow. The types of Value Stream Mapping include:
- Current State Value Stream Mapping: Analyses and visually represents the existing processes and workflows within a system, highlighting inefficiencies, bottlenecks, and improvement areas. It provides a baseline for analysing the current state of operations.
- Ideal State Value Stream Mapping: Envisions the optimal or ideal future state of the value stream by eliminating identified inefficiencies and implementing improvements. It serves as a goal-setting tool for organisations striving for enhanced productivity and reduced waste.
- Future State Value Stream Mapping: Outlines the planned and achievable improvements based on the ideal state, incorporating practical steps and strategies to transition from the current state to the desired future state. Guides organisations in implementing changes and achieving continuous improvement.
What is Kanban in Value Stream Mapping?
Kanban Value Stream Mapping (Kanban VSM) is a lean management methodology that combines the principles of Kanban and Value Stream Mapping to optimise workflow efficiency. It involves visual tools, such as Kanban boards and Kanban cards, to map and analyse the entire value stream, from production to delivery. Kanban Value Stream Mapping focuses on real-time visibility, allowing teams to identify bottlenecks, and improve overall process flow using Kanban Boards. By integrating Kanban's pull-based system with Value Stream Mapping techniques, organisations gain a holistic view of their processes, enabling continuous improvement and fostering a more responsive and adaptive approach to production.
Why use Kanban for Value Stream Mapping?
Kanban Value Stream Mapping (Kanban VSM) is crucial for manufacturers as it combines the efficiency of Kanban's visual management system with the analytical power of Value Stream Mapping. This integration provides a real-time, transparent view of the production process, enabling manufacturers to identify and address inefficiencies promptly. Kanban VSM aids in minimising waste, optimising production cycles, and enhancing collaboration among team members. The visual representation of workflows facilitates quick decision-making, improving overall process efficiency. By using Kanban VSM, manufacturers can achieve a leaner, more responsive production system, resulting in reduced lead times, increased flexibility, and continuous improvement in their operations.
How to create a Value Stream Map using a Kanban board?
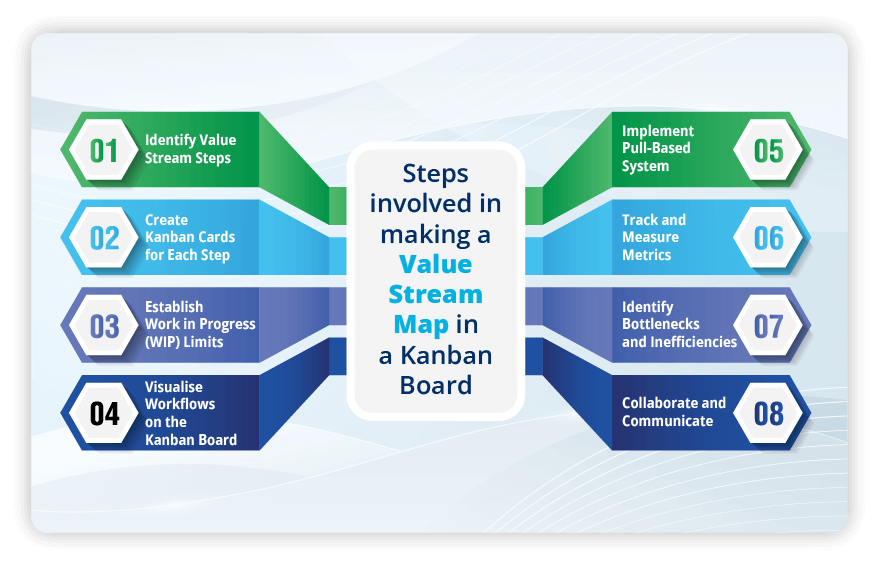
Let's discuss the various steps involved in making a Value Stream Map in a Kanban Board to improve production processes.
-
Step 1: Identify Value Stream Steps
- Begin by defining the key steps in your manufacturing process. This includes everything from raw material acquisition to the delivery of the final product.
-
Step 2: Create Kanban Cards for Each Step
- Represent each identified step with Kanban cards on the Kanban board. Include essential information on the cards, such as work items, cycle times, and dependencies.
-
Step 3: Establish Work in Progress (WIP) Limits
- Set WIP limits for each column on the Kanban board to control the amount of work at each stage. This prevents overloading and helps maintain a smooth flow through the value stream.
-
Step 4: Visualise Workflows on the Kanban Board
- Arrange the Kanban cards on the board to visually depict the workflow through the value stream. Use different columns to represent different stages in the production process.
-
Step 5: Implement Pull-Based System
- Embrace the pull-based system by allowing work to be pulled only when there is capacity. It ensures effective resource utilisation and prevents overproduction.
-
Step 6: Track and Measure Metrics
- Regularly monitor and update metrics associated with each step, such as lead times and cycle times. This data provides insights into the performance of the value stream and identifies improvement areas.
-
Step 7: Identify Bottlenecks and Inefficiencies
- Use the Kanban board to identify bottlenecks and inefficiencies in the value stream. Visual cues help teams quickly spot issues and take corrective actions to improve overall workflow.
-
Step 8: Collaborate and Communicate
- Foster collaboration among team members by encouraging real-time communication through the Kanban board. This ensures that everyone is informed about the status of work items and can contribute to problem-solving.
What are the key benefits of using Kanban for Value Stream Mapping?
- Visualising Workflow: Kanban provides a visual representation of the entire workflow, allowing teams to quickly identify bottlenecks, Work in Progress (WIP), and overall process efficiency. This visual aspect aids in quickly understanding the value stream.
- Real-Time Monitoring: Through Kanban boards, teams can monitor the status of tasks and stages in real-time. This quickly identifies delays or issues, facilitating prompt corrective actions and continuous improvement.
- WIP Limits for Flow Control: Kanban uses Work In Progress (WIP) limits to control the number of tasks in each process stage. This prevents overloading and ensures a steady flow, optimising resource utilisation and reducing lead times.
- Continuous Improvement: Kanban emphasises continuous improvement through regular retrospectives. This iterative feedback loop enables teams to analyse their processes, pinpoint improvement areas, and implement changes gradually, fostering a culture of constant growth.
- Flexibility and Adaptability: Kanban is highly flexible and adaptive, making it suitable for dynamic and evolving workflows. Teams can easily accommodate changes in priorities, tasks, or requirements, ensuring that the value stream remains responsive to shifting demands.
- Customer Focus: Kanban helps teams align their efforts with customer needs and expectations by visualising the entire value stream. This customer-centric approach ensures that the value stream is optimised to deliver maximum value, meeting or exceeding customer requirements.
- Reduced Waste: Kanban helps identify and eliminate waste in the value stream. By streamlining processes, reducing unnecessary tasks, and optimising resource usage, teams can minimise wasted time and resources, ultimately improving overall efficiency.
- Predictable Delivery: Using WIP limits and continuous monitoring, Kanban enables teams to establish a predictable and reliable delivery cadence. This predictability enhances planning accuracy and allows for better management of customer expectations.
Five best tips for implementing Kanban in Value Stream Mapping
- Clearly define workflow stages and visualise them on a Kanban board to provide a transparent overview of the entire value stream.
- Set and enforce WIP limits at each stage to optimise flow, prevent overloading, and maintain a balanced workload.
- Foster a continuous improvement culture by regularly reviewing and refining the Kanban process through feedback loops and retrospectives.
- Prioritise customer needs by aligning tasks with customer requirements, ensuring that the value stream consistently delivers maximum value.
- Empower teams by encouraging collaboration, autonomy, and active participation in refining their workflows within the Kanban framework.
Why integrate Kanban with Value Stream Mapping for process improvement?
Integrating Kanban with Value Stream Mapping aids process improvement by providing a visual and dynamic framework. Kanban's visual boards offer real-time visibility into workflow stages, allowing teams to identify bottlenecks, optimise resource utilisation, and set Work In Progress (WIP) limits for efficient flow. Combined with Value Stream Mapping, it offers a holistic perspective, enabling organisations to analyse end-to-end processes, reduce lead times, and eliminate waste. This integration fosters an improvement culture which aligns tasks with customer needs and empowers teams to adapt swiftly to changing requirements.
Is Kanban a versatile tool applicable across diverse industries for Value Stream Mapping?
Kanban Value Stream Mapping exhibits versatile applicability, transcending industry boundaries. Its effectiveness extends across diverse sectors such as
Manufacturing,
Automotive,
Plant hire, Energy,
Construction,
HVAC,
Pharma, Healthcare, and beyond. The principles of visualising workflows, setting WIP limits, and fostering continuous improvement are universally adaptable, making Kanban a valuable tool for optimising processes, reducing lead times, and enhancing overall efficiency in various industries.
Let’s discuss an example of
Kanban Value Stream Mapping in an Automotive Industry
to understand its industrial application in general:
- Identify Value Stream Steps: Identifying Value Stream steps such as designing, sourcing materials, assembly, quality control, and shipping.
- Create Kanban Cards for Each Step: Kanban Cards are created for each step in the value stream. These cards could represent specific components or tasks such as engine assembly, body painting, or quality inspections in the automotive sector.
- Establish Work in Progress (WIP) Limits: Work in Progress (WIP) limits are established at this stage. For example, setting a particular limit on the number of cars in the assembly line to ensure efficient workflow and resource allocation.
- Visualise Workflows on the Kanban Board: This involves visualising workflows on the Kanban Board. In an automotive scenario, this could be a digital or physical board displaying the progress of each vehicle through the manufacturing process, from raw materials to the finished product.
- Implement Pull-Based System: A pull-based system is implemented, where subsequent stages only commence work when there is a demand, aligning with the Just-in-Time production philosophy prevalent in the automotive industry.
- Track and Measure Metrics: Tracking and measuring metrics are crucial in the manufacturing sectors. This might involve monitoring production cycle times, defect rates, and inventory levels to ensure optimal performance.
- Identify Bottlenecks and Inefficiencies: Identifying bottlenecks and inefficiencies is necessary for quality production. For instance, discovering delays in the supply chain for specific components or identifying areas of the assembly line where work accumulates can help streamline the overall process.
- Collaborate and Communicate: In the automotive sector, effective collaboration between design, manufacturing, and quality control teams is essential to address issues promptly and ensure a smooth workflow through the entire value stream. Proper communication ensures everyone is aligned with the goals of minimising waste, optimising resources, and efficiently delivering high-quality vehicles.
Get a Personalised Demo for your VSM with Kanban Boards!
How can Kanban boards be customised to fit the unique needs of my value stream?
Customising Kanban boards to suit the unique needs of your value stream involves tailoring the board's structure, columns, and visual elements. The flexibility of Kanban allows you to adapt the board continuously, accommodating changes in your value stream and ensuring the board remains a dynamic tool tailored to the specific demands of your industry. You can customise Kanban Boards by following these simple guidelines:
- Identify specific workflow stages in your value stream and design columns to represent these stages on the Kanban board.
- Integrate custom fields or labels to provide additional context or categorise tasks based on your industry's requirements.
- Adjust the board layout to align with the sequence of your unique processes, and incorporate colour-coded cards or tags to signify priority or task type.
What should you do before transitioning to a Kanban-based Value Stream Mapping system?
It's essential to evaluate your current organisation's processes thoroughly before implementing a Kanban-based Value Stream Mapping system. This thorough preparation lays the foundation for a successful integration, fostering a culture of continuous improvement and efficiency within your organisation.
- Engage stakeholders to gather insights into their perspectives and expectations. Establish clear goals and objectives for the Kanban system, aligning them with overall business objectives.
- Train teams on Kanban principles and practices to ensure a shared understanding of the methodology.
- Define Key Performance Indicators that align with your business goals, providing a baseline for measuring the success of the Kanban-based Value Stream Mapping implementation.
Overcoming common challenges faced while implementing Kanban for Value Stream Mapping
- Lack of Visual Management Understanding: Provide clear explanations and training on visual management concepts. Illustrate how Kanban boards visually represent workflows, making it easier for teams to comprehend and manage their tasks effectively.
- Inadequate Training and Knowledge: Invest in comprehensive training programs to ensure teams understand Kanban principles and practices.
- Failure to Set WIP Limits: Emphasise setting and respecting Work In Progress (WIP) limits. Communicate the impact of exceeding limits on the overall flow and quality of work, ensuring adherence to optimised performance.
- Poorly Defined Value Stream Steps: Conduct a thorough analysis to identify and define value stream steps accurately. Collaboration with cross-functional teams ensures a comprehensive understanding, facilitating a more accurate representation of the Kanban board.
- Lack of Regular Feedback and Improvement: Establish a feedback loop through regular retrospectives and reviews. Promote an environment of ongoing improvement by fostering open communication to pinpoint areas for enhancement and gradually implement changes. This approach cultivates a continuous improvement culture within the organisation.
- Failure to Track and Measure Metrics: Establishing KPIs that align with business objectives and monitoring and analysing relevant metrics is essential. Use this data to identify patterns, measure efficiency, and make data-driven decisions for continuous improvement.
Differences between Traditional Value Stream Mapping and Kanban approach in Value Stream Mapping
Traditional Value Stream Mapping | Kanban approach in Value Stream Mapping |
---|---|
Traditional VSM provides a comprehensive, static visual representation. | Kanban VSM is dynamic, emphasising real-time visualisation and continuous improvement. |
Traditional VSM typically uses process maps and diagrams. | Kanban VSM incorporates Kanban boards and cards for dynamic workflow representation. |
Traditional VSM focuses on surface-level analysis and planning. | Kanban VSM prioritises adaptability, in-depth analysis and ongoing process optimisation. |
Traditional VSM may be less adaptable to dynamic changes in processes. | Kanban VSM embraces change, fostering a culture of continuous improvement. |
Transform your VSM Processes Today
Start your journey toward efficiency and operational excellence with TCard solutions.