Contents
- What is a Gemba Walk?
- What are the different types of Gemba walk?
- How often should Gemba Walks be conducted?
- What are the benefits of Gemba?
- How can you make a Gemba walk checklist?
- Gemba Walk Template
- Gemba walk example
- Is Gemba Walk an audit?
- How do you write a Gemba report?
- How long is a Gemba walk?
- What tools are used in Gemba walk?
- How to execute a successful Gemba?
- How to Conduct a Gemba Walk for Root Cause Problem Solving?
- How to Overcome the common challenges faced during Gemba Walks?
- What are the advantages of Gemba Walks over Management By Wandering Around (MBWA) ?
- Can Gemba Walks be conducted in virtual or remote work settings?
- Genchi Genbutsu vs Gemba
- Gemba Walks and Process Confirmation Audits
- Best practices for a Successful Gemba
- Gemba Walk applications in various industries
- How do you follow up and implement the improvements identified from a Gemba walk?
What is a Gemba Walk?
A Gemba Walk is a fundamental practice in lean management, emphasising direct observation of work processes in their actual environment to gain insights, identify inefficiencies, and foster a culture of continuous improvement.
Gemba Walk involves three essential elements:
-
Go See:
This principle emphasises the importance of physically going to the location where work is being done, whether it's a factory floor, an office space, or any other operational area. By being present at the actual site, managers can understand the processes deeply, identify bottlenecks, and observe the work environment firsthand. -
Ask Why:
Asking probing questions is crucial during a Gemba Walk. It involves engaging with the employees and understanding the reasons behind certain processes or issues. By repeatedly asking "why", managers can uncover root causes and gain valuable insights into the challenges faced by the workforce, enabling them to address issues at their source. -
Show Respect:
Respecting the knowledge and expertise of the employees working in the Gemba is essential. Acknowledging their insights, involving them in problem-solving discussions, and appreciating their efforts fosters a positive and collaborative atmosphere. Respectful communication encourages employees to share their observations and suggestions freely, promoting a culture of continuous learning and improvement.
The Gemba principles include:
-
Go to Gemba:
When an abnormality is detected, ‘Go to Gemba’ emphasises the importance of taking immediate action to address the issue. When a problem arises, managers and workers go directly to the location (Gemba) to understand the situation firsthand. -
Check the Gembutsu:
‘Gembutsu’ refers to the actual product or machine involved in the problem. Professionals inspect equipment, products, or tools related to the situation to understand the circumstances better. For instance, this could mean examining a faulty machine to understand its issues in manufacturing. -
Take Countermeasures on the spot:
This principle emphasises swift action. Once at Gemba and after inspecting the issue (Gembutsu), immediate corrective actions are taken on the spot to address the problem, preventing its escalation. -
Find out the Root Causes:
To solve problems at their core, asking "why" multiple times helps identify the root cause. This methodical questioning goes deep into the problem's origin, ensuring that solutions address fundamental issues, not just observed deviations. -
Standardise to prevent reoccurrence:
After identifying the root cause, standardising processes and implementing best practices prevent the problem from recurring. Standardisation ensures that the improvements are sustained over time.
The 3 P's of Gemba Walk - Purpose, Process, and People - guide these initiatives. The purpose ensures that the walk has clear objectives, whether it's improving a specific process, addressing safety concerns, or enhancing overall efficiency. The process emphasises gaining diverse viewpoints, involving employees from different roles and levels to gather comprehensive insights into the workflow and operational procedures.
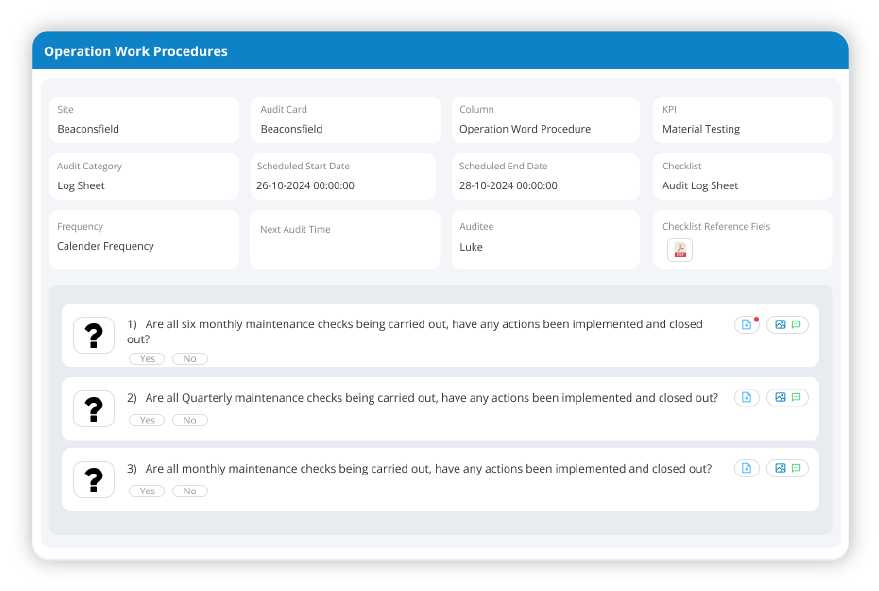
What are the different types of Gemba walk?
-
Personal Gemba:
Personal Gemba is conducted by an individual leader in one or more specific areas to understand the work processes better and identify areas for improvement. Such a Gemba walk is unplanned, and the leader doesn't rely on the team's preparations for performing it. Personal Gemba helps you get new ideas before setting new targets or challenges for your team. -
Leadership Gemba:
Leadership Gemba is led by a team of senior managers or leaders. Senior leaders engage with frontline employees during such a Gemba to gain insights into shop floor operations. This helps them demonstrate leadership commitment to continuous improvement, identify opportunities for organisational growth, and guide the team in operational processes. -
Daily Gemba Walk:
Daily Gemba Walks are conducted regularly, often daily, inside departments by departmental leaders to monitor routine operations and ensure that processes align with organisational goals. This type of Gemba Walk emphasises real-time observation, allowing managers to address issues promptly and make quick decisions. Organisations can respond swiftly by identifying deviations from standard procedures or unexpected challenges, ensuring operational efficiency. Daily Gemba Walks help maintain consistency, improve communication, and ensure the organisation stays on track toward its objectives. -
Impromptu Gemba Walk:
Impromptu Gemba Walks are unplanned initiatives triggered by sudden incidents, employee concerns, or unexpected workplace issues. These walks are immediate responses to urgent matters that require swift attention. Impromptu Gemba Walks allow managers to assess the situation firsthand, enabling quick problem-solving. By addressing issues promptly, organisations can prevent potential escalation of problems and maintain a smooth workflow. -
Scheduled Gemba Walk:
Scheduled Gemba Walks are planned in advance and occur regularly, providing a structured approach to process improvement. During these walks, a team of observers systematically evaluates processes, collects data, and analyses the information gathered. Scheduled Gemba Walks focus on long-term process improvements and strategic alignment with organisational goals. Organisations can identify patterns, trends, and areas for significant enhancements by examining processes methodically.
How often should Gemba Walks be conducted?
Gemba Walks should be conducted regularly, ideally daily or weekly, to maintain an organisation's continuous improvement mindset. These walks are typically led by managers, supervisors, or team leaders who directly understand the processes being observed. Ideally, participants in Gemba Walks should include cross-functional teams involving employees from various roles and levels.
The goal of Gemba walk is to gather diverse perspectives and insights. It fosters a culture of continuous improvement within organisations by identifying inefficiencies, reducing waste, enhancing productivity, and optimising processes. Hence organisations can create an environment where problems are opportunities for improvement, leading to increased efficiency, higher quality, and overall operational excellence. In some cases, Gemba Walks can be structured as Gemba meetings, allowing for collaborative problem-solving and fostering a culture of shared responsibility for process improvement.
What are the benefits of Gemba?
-
Real-Time Insights:
Gemba provides firsthand, real-time observations of processes, allowing immediate understanding of workflow efficiency and challenges. -
Employee Engagement:
Involves employees directly, fostering a sense of ownership, accountability, and active participation in problem-solving. -
Continuous Improvement:
Identifies areas for enhancement, enabling organisations to implement immediate and long-term changes. -
Waste Reduction:
Helps pinpointing and eliminating wasteful activities, resources, and time, enhancing Overall Operational Efficiency (OOE). -
Enhanced Communication:
Encourages open dialogue, ensuring effective communication between management and employees, leading to streamlined processes. -
Quality Improvement:
Facilitates the identification of defects or issues, enabling organisations to promptly enhance product or service quality. -
Cultivates a Learning Culture:
Promotes a culture of continuous learning and adaptation, encouraging employees to adapt to changing circumstances and improve their skills. -
Higher Productivity:
Gemba contributes to increased organisational productivity and output by addressing inefficiencies and optimising workflows.
Experience the benefits of Gemba
How can you make a Gemba walk checklist?

Creating a Gemba Walk checklist involves outlining key areas and processes to be observed during the walk, ensuring a systematic approach to gathering insights.The Gemba walk checklist acts as a structured guide, ensuring that crucial processes aren't missed during the Gemba observations.
- Begin by pinpointing clear objectives that align with organisational goals like process efficiency, safety protocols, or quality standards.
- Divide these objectives into actionable items specifying what to observe, ask, and document during the Gemba Walk.
- Organise these items into categories based on the aspects of the workplace to be assessed.
- Develop relevant Gemba questions for each category, guiding observers on what to focus on and inquire about during the Gemba Walk.
- Provide clear instructions to observers, outlining the categories, questions, and specific details to look for during the walk.
- Instruct observers to document their observations, responses to questions, and any issues identified during the Gemba Walk.
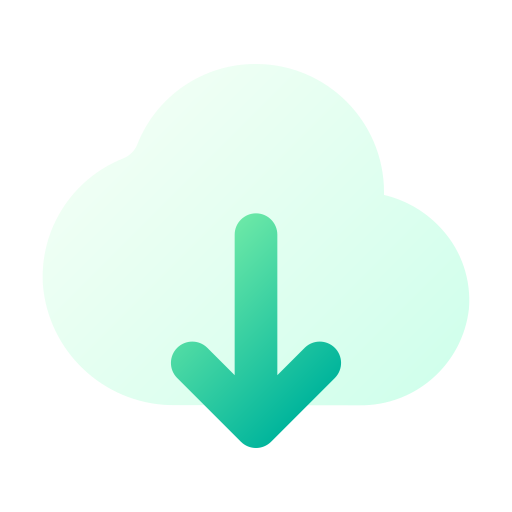
Download Gemba Walk Template Here
Download TemplateStart Creating your Gemba Checklist
Gemba Walk Template
A Gemba Walk template provides a roadmap for leaders and teams to conduct Gemba Walks, which involve going to the "gemba" to observe and engage with employees, processes, and the work environment. The template typically outlines key elements to focus on during the walk, such as safety, quality, productivity, and employee morale. Using a Gemba Walk template, organisations can standardise their approach, enhance communication, and promote a culture of continuous improvement, leading to more effective problem-solving and increased operational excellence.
Gemba walk example
Let's consider a Gemba Walk example in a manufacturing plant.
An automobile manufacturing plant has been experiencing production delays leading to missed deadlines. On the Gemba walk, the plant manager's direct observation and engagement with employees helps him identify specific issues, which enables problem-solving and long-term process improvements, ultimately enhancing production efficiency.
-
Gemba Walk Objective:
Root cause identification of the production delays. -
Preparation:
The Plant manager prepares the checklists for observing the machine operations, employee performance and material flow. -
Observation:
On the shopfloor the plant manager observes the following details:- How the assembly line works?
- How machines are operated?
- How effectively the raw materials are used?
- Employee shift output.
-
Engaging with Employees:
The plant manager interacts with frontline workers, discussing tasks, challenges, and improvement ideas. Employees voice concerns leading to production delays. -
Identifying Issues:
The plant manager identifies the underlying issues in this stage:- Machine Malfunction
- Delay in the material flow from the warehouse to the assembly line
-
Problem-Solving on the Spot:
The plant manager initiates quick actions to resolve the issue:- Reporting the breakdown maintenance to the maintenance management team for repairs.
- Escalating the issue of delay in material delivery to the logistics team.
-
Root Cause Analysis:
In the Post Gemba Walk, the detailed Root Cause Analysis reveals the root causes as failure to adhere to the planned maintenance and inaccurate inventory recordings. -
Action Plans:
The following action plans were taken as the following steps:- Evaluating the current maintenance procedures to identify any inefficiencies or areas prone to failure. Standardise maintenance protocols and create clear, documented processes for scheduling, executing, and recording maintenance tasks.
- Improving the inventory management processes by implementing an efficient inventory tracking system. Utilising technology like RFID, barcoding, or advanced software to enhance accuracy in inventory recording.
-
Documentation:
The plant manager records issues identified in the RCA and the action plans implemented to address them as logs for the further reference and improvement actions. -
Follow-Up:
The plant manager follows up with the responsible team members by taking the following steps:- Regularly meet with the maintenance and inventory teams, track Key Performance Indicators, and audit records to ensure the implementation of standardised maintenance protocols and efficient inventory management technologies.
- Continuously gather feedback and address issues to maintain the effectiveness of these improvements and sustain operational efficiency.
Is Gemba Walk an audit?
A Gemba Walk is not simply an audit; it goes beyond traditional inspection methods. While audits often involve assessing compliance with predetermined standards, Gemba Walk takes leaders to the real place where work happens, fostering direct observation and engagement with employees. Gemba Walks emphasises employee engagement, continuous improvement, and problem-solving by involving workers at the frontline, ensuring their active participation.
Unlike audits, which can sometimes create a sense of fear or resistance, Gemba Walks foster a collaborative atmosphere where employees are encouraged to share their perspectives openly. A Gemba Walk aims to identify inefficiencies, eliminate waste, and enhance overall productivity and quality, making it a dynamic and interactive approach distinct from traditional audits.
How do you write a Gemba report?
-
Define Purpose and Objectives:
Clearly state the aim of the Gemba report, whether it's process improvement, identifying inefficiencies, or enhancing quality. -
Identify Specific Areas to Observe:
Outline the key areas to focus on during the Gemba Walk, such as workflows, employee interactions, or equipment usage. -
Document Observations:
Record both strengths and areas needing improvement observed during the walk. Use clear language and be specific about what processes were observed. -
Support with Data and Examples:
Back up observations with real-life examples. This provides context and makes the report more convincing. -
Provide Actionable Recommendations:
Offer practical solutions for the identified issues. It is important to highlight how these changes will affect the project's efficiency, quality, and safety aspects. -
Incorporate Visual Aids:
Use visual tools like quad charts, process flow charts, or images to illustrate key points. Visual aids enhance understanding and make the report more engaging. -
Highlight Employee Contributions:
Acknowledge and showcase employee input and feedback. This recognises their efforts and fosters a sense of ownership and motivation for improvement. -
Emphasise Continuous Improvement:
Conclude the report by stressing the importance of ongoing improvement efforts. This creates process enhancement within the organisation.
How long is a Gemba walk?
The duration of a Gemba Walk can vary based on the specific objectives, the size of the organisation, and the complexity of the observed processes. Typically, a Gemba Walk on the shop floor lasts 30 minutes to an hour. This time frame allows managers and team leaders to engage in direct, focused observations, allowing them to interact with employees and understand workflows without significantly disrupting the ongoing operations. The concise duration ensures that the Gemba Walk is efficient, allowing for regular, systematic observations and discussions facilitating continuous improvement initiatives within the organisation.
What tools are used in Gemba walk?
During Gemba Walks, various tools, technologies or software can enhance the observation and data documentation process, ensuring a comprehensive understanding of the operational environment.
-
Gemba Board:
Gemba Boards provide a visual representation of the workplace, helping teams track tasks, issues, and progress. They are instrumental in promoting transparency and facilitating on-site problem-solving. -
Kanban Boards:
Kanban boards visualise workflow, allowing teams to track tasks, identify bottlenecks, and enhance process efficiency. They provide a clear visual representation of work stages, aiding real-time observation and problem-solving. -
Kamishibai Boards:
Kamishibai boards are visual management tools used for process audits. They help schedule and track regular checks, ensuring standard procedures are followed. During Gemba Walks, these boards facilitate monitoring adherence to processes. -
Mobile Devices and Applications:
Mobile devices with specific applications enable real-time data collection, photo capturing, and note-taking during Gemba Walks. These applications streamline information gathering and enhance communication among team members. -
Video Recording Devices and Camera:
Cameras and video recording devices can capture visual evidence of processes and operations. They serve as powerful tools for review, analysis, and training purposes, providing a detailed understanding of workflow dynamics.
How to execute a successful Gemba?
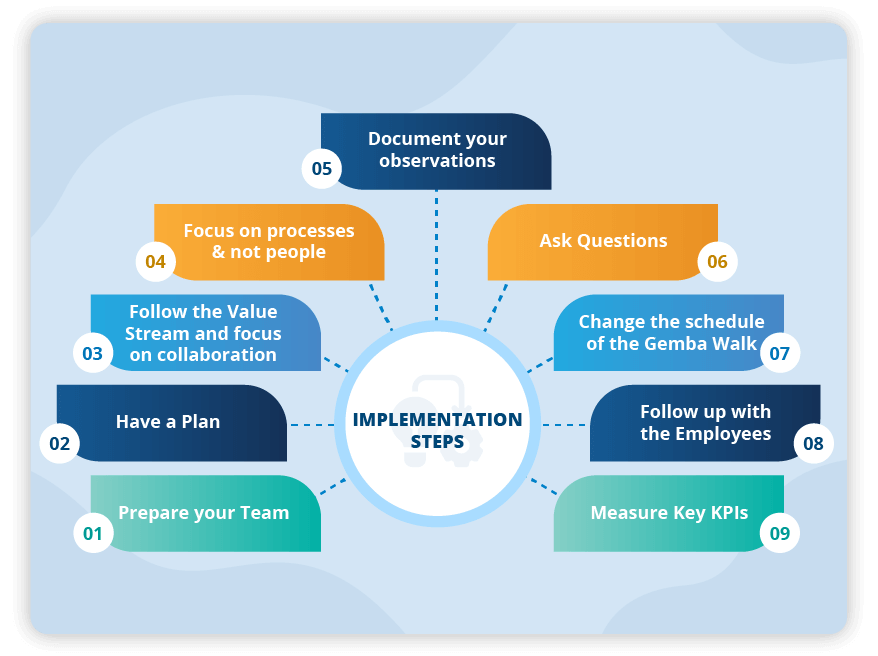
The Gemba walk typically involves nine steps, emphasising the practice of going to the location where work is done to truly understand processes, identify issues, and foster continuous improvement. Each step is crucial in promoting a culture of continuous improvement within an organisation, ensuring that decisions are grounded in firsthand knowledge and real-world observations.
Pre Gemba Phase:
- Prepare the team
- Have a plan
- Follow Value stream maps or process flows
Gemba Walk:
- Focus on processes and not on people
- Document your observations
- Ask questions
Post Gemba Phase:
- Mix up the schedules of your Gemba walk
- Follow up with employees
- Measure key KPIs
Book a Personalised session as to how to make Gemba walk effective.
How to Conduct a Gemba Walk for Root Cause Problem Solving?
In Root Cause Analysis (RCA), conducting a Gemba Walk is vital for identifying and resolving underlying issues. By physically being on the workplace floor, Gemba Walks enable firsthand observation of processes, pinpointing waste, inefficiencies, and errors. This direct engagement with the work environment allows for a deeper understanding of the problems at their source. It facilitates the identification of root causes, leading to targeted solutions that address the core issues, thus enhancing overall efficiency and productivity. Gemba Walks in RCA provide valuable insights for effective problem-solving and continuous process improvement.
How to Overcome the common challenges faced during Gemba Walks?
-
Lack of Employee Engagement:
Create an open, non-judgmental environment which encourages active participation of employees. Implement suggestions promptly to show their contributions matter. -
Superficial Observations:
Provide training on deep analysis techniques like the 5 Whys. Encourage asking probing questions and emphasise digging beyond surface issues to find root causes. -
Time Constraints:
Efficiently plan Gemba Walks, scheduling during low-activity periods. Focus on critical processes. Rotate team members to cover various areas, ensuring comprehensive observations despite limited time. -
Resistance to Change:
Involve employees in decision-making. Clearly communicate reasons for changes, highlighting benefits. Offer training and support during implementation. Recognise and reward successful adoption to motivate employees. -
Inadequate Follow-up:
Establish a robust tracking system. Assign responsibilities, set clear deadlines, and review progress in team meetings. Celebrate achievements to reinforce the positive impact of Gemba Walk solutions. Use visual management tools like Kanban boards, Huddle boards or Kamishibai boards for better discussions based on real-time data. -
Cultural Barriers:
Facilitate cross-cultural team-building activities. Use visuals and demonstrations to enhance communication clarity. Promote patience and active listening among team members.
What are the advantages of Gemba Walks over Management By Wandering Around (MBWA) ?
Unlike MBWA, Gemba Walks specifically focus on direct observation at the workplace, encouraging a hands-on understanding of processes and challenges. By being physically present in the Gemba (real place of work), managers gain firsthand insights into operations, employee engagement, and workflow efficiency. Gemba Walks promote continuous improvement by solving problems on-site. This approach ensures immediate issue identification and resolution, enhancing productivity, reducing waste, and a safer work environment. In contrast, while MBWA involves informal interactions, Gemba Walks emphasises real-time observation, making it a more targeted and action-oriented method for driving operational excellence and fostering employee engagement. Hence Gemba Walks offer advantages over Management By Wandering Around (MBWA) by emphasising direct observation, employee engagement, and problem-solving at the workplace.
Can Gemba Walks be conducted in virtual or remote work settings?
In Virtual Gemba Walks, managers use digital tools like video conferencing, screen sharing, and visual management boards to observe remote work processes, interact with team members, and gain insights into their challenges and successes. Visual management tools play a prominent role in Virtual Gemba. Digital softwares like Kanban boards, Kamishibai boards, and T cards enable remote teams to visualise tasks, task status, and potential issues in real-time. When integrated into the digital Gemba walk process, Kamishibai Boards facilitate scheduled audits, ensuring adherence to processes even in remote settings. T cards offer a clear overview of tasks, making it easier for team members to optimise their workflow. These visual aids bridge the gap in executing Gemba Walks virtually, ensuring effective communication and continuous improvement in remote work environments. Additionally, Gemba Walk software facilitates real-time workplace observation and efficiency with global accessibility.
Read MoreGenchi Genbutsu vs Gemba
Genchi Genbutsu and Gemba Walks both emphasise firsthand observation but differ in scope. Genchi Genbutsu, a Japanese term meaning "go and see for yourself," involves top-level executives visiting the actual location of a problem or situation, encouraging them to understand the shop floor processes. On the other hand, Gemba Walks refer to regular, structured walks taken by managers and supervisors to observe processes, engage with employees, and identify issues within the workplace. While Genchi Genbutsu focuses on high-level executives gaining profound insights, Gemba Walks involves continuous, on-the-ground engagement, empowering managers at various levels to identify and address issues promptly, fostering a culture of continuous improvement within the organisation.
Gemba Walks and Process Confirmation Audits
Gemba Walks involves managers and supervisors physically inspecting the workplace to validate standard operating procedures, ensuring alignment with organisational goals. These walks are essential for verifying that processes are being executed as planned and identifying any deviations or inefficiencies. The Kamishibai board can be considered an essential tool for process confirmation audits, providing a structured format to display tasks and processes visually. Using Kamishibai boards during Gemba Walks, teams can confirm process adherence, track progress, and address inefficiencies, improving efficiency and quality control.
Read MoreBest practices for a Successful Gemba
Let’s understand the best practices for a successful Gemba walk and deviations that make it ineffective.
Ineffective Gemba
Effective Gemba
Gemba Walk applications in various industries
While they originated in manufacturing, Gemba Walks have been successfully adapted to various sectors like healthcare, service, automotive, plant hire, HVAC, construction and office environments. In these contexts, Gemba Walks involve observing processes, engaging with employees, and identifying areas for improvement within administrative tasks, customer service procedures, healthcare practices, and other non-manufacturing processes. The principles of direct observation, employee engagement, and continuous improvement are universally valuable, making Gemba Walks relevant and effective across diverse industries.
How do you follow up and implement the improvements identified from a Gemba walk?
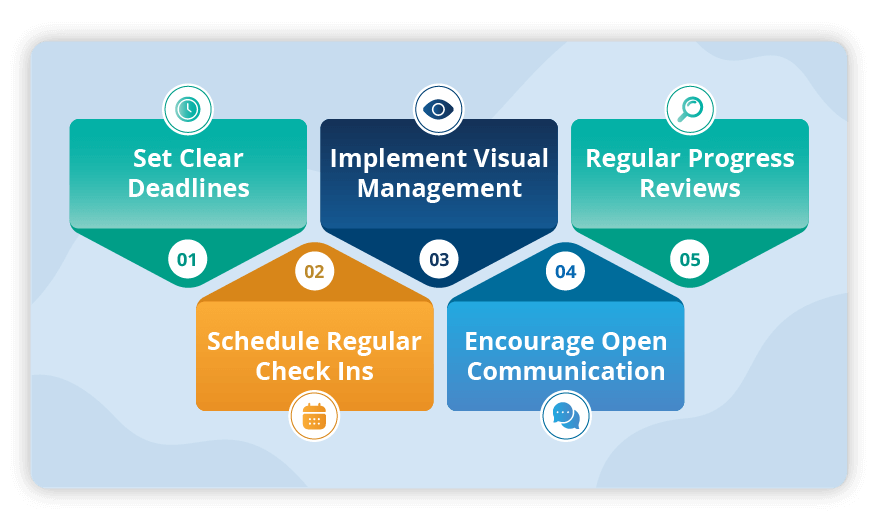
Following a Gemba Walk, it's crucial to establish a systematic follow-up process.
-
Set Clear Deadlines:
Clear timeframes for the identified improvements ensures timely completion. -
Schedule Regular Check Ins:
Tracking action plans real time allows for necessary adjustments to be made in it. -
Implement Visual Management:
Utilise visual tools such as Kanban boards to monitor the status of improvement tasks. Visual cues enhance transparency, making it easier to assess the progress of each task at a glance. -
Encourage Open Communication:
When team members feel comfortable sharing ideas, concerns, and feedback openly, promoting transparency and collaboration within the organisation. -
Regular Progress Reviews:
Conduct periodic reviews with both leadership and team members. These provide opportunities to assess the overall progress, identify areas needing additional attention, and ensure sustained improvement aligning with organisational goals and growth strategies.
Gemba Kaizen integrates real work principles of Gemba and continuous improvement principles of Kaizen, emphasising observation and employee engagement. The 5S of Gemba Kaizen - Sort, Set in Order, Shine, Standardise, and Sustain - organises workplaces for efficiency, reducing waste, enhancing productivity, and ensuring safety.
Gemba Kanri aligns perfectly with this approach, focusing on empowering employees and fostering a sense of responsibility. Actively involving employees in process development enhances individual performance and contributes to operational excellence, resulting in improved quality, reduced costs, minimised inventory, and streamlined lead times while effectively meeting delivery requirements.
Ready to implement improvements from your Gemba walk?
Learn More about Gemba Walks :
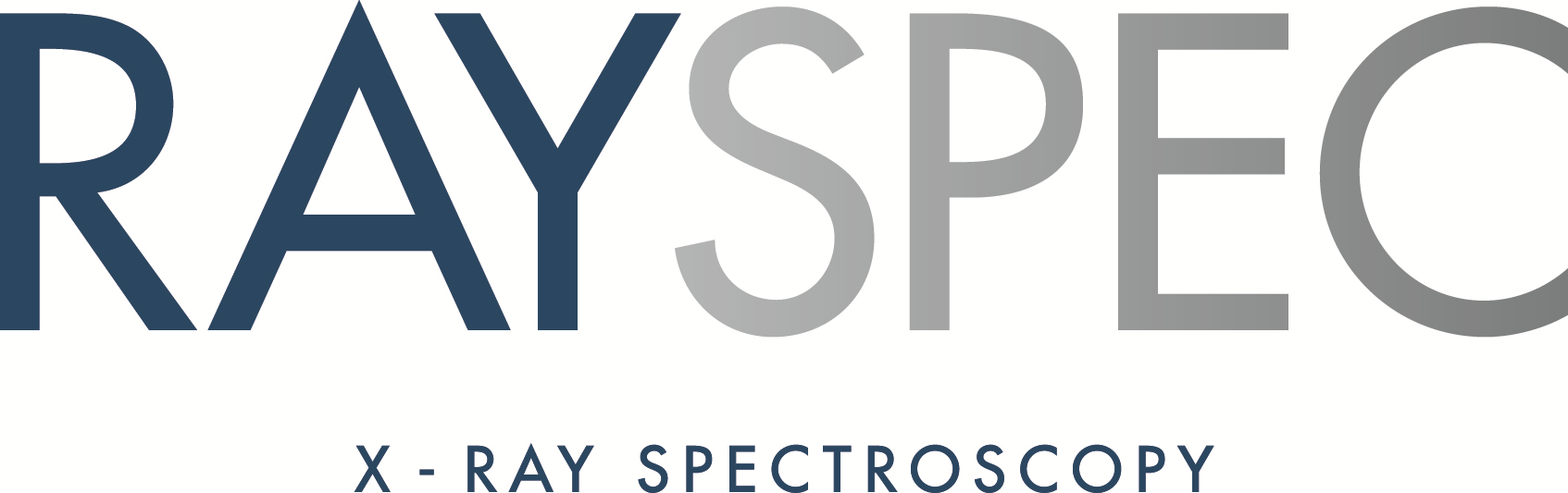
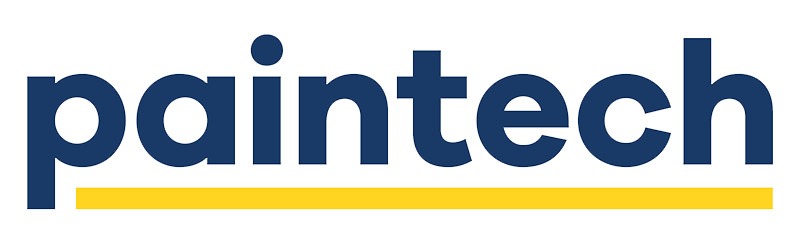
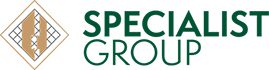
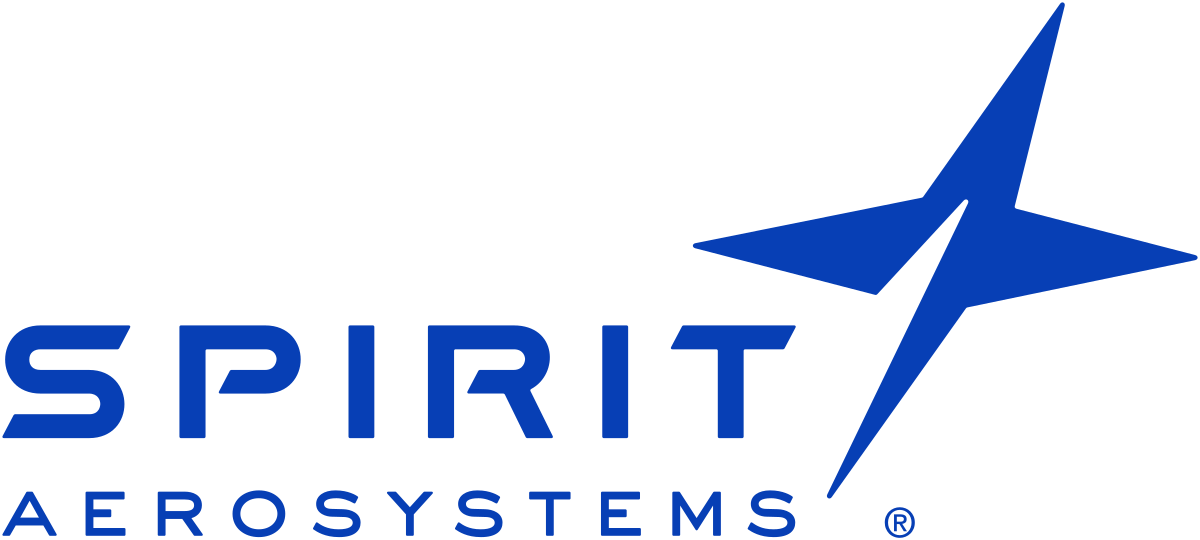
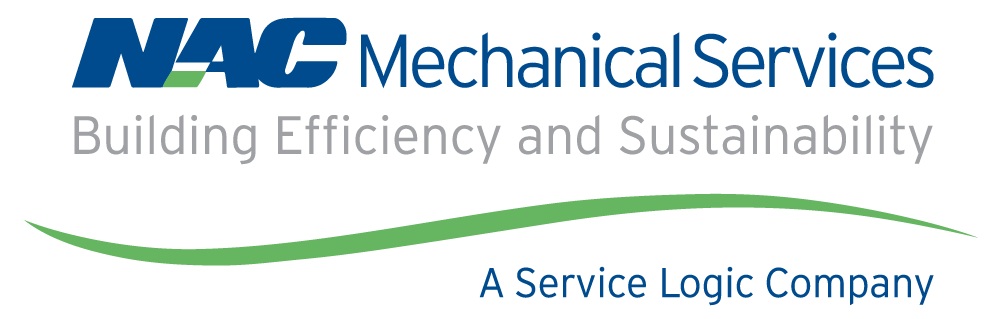
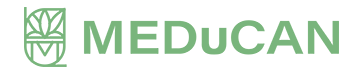

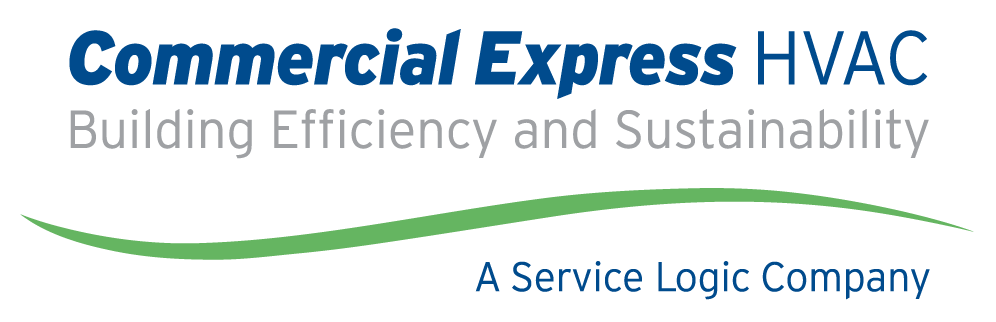
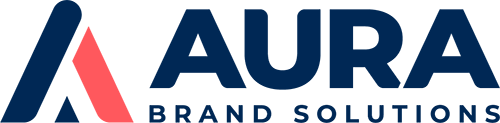
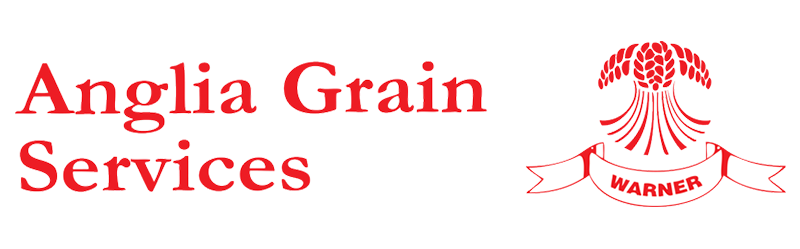
Maximise Efficiency with Gemba Walks
Ready to identify inefficiencies and improve your shop floor operations? Start implementing Gemba Walks now and enhance your team’s performance.