Contents
- What is Leader Standard Work (LSW)?
- Why should organisations Implement Leader Standard Work?
- How does Leader Standard Work differ from other Management approaches?
- What Benefits can organisations expect from Implementing Leader Standard Work?
- Steps to Implement Leader Standard Work effectively
- How Digital Solutions enhance the Implementation of Leader Standard Work?
- Key Practices within Leader Standard Work
- How often should Leader Standard Work be performed?
- What are the Benefits of Standardising a Manager’s Daily Work?
- Is Leader Standard Work Applicable for various Industries?
- Is Leader Standard Work only for Top-level executives?
- Overcoming potential Challenges while Implementing Leader Standard Work
- Example for Leader Standard Work
What is Leader Standard Work (LSW)?
Leader Standard Work (LSW) is a fundamental component of Lean management, encompassing the routine tasks or activities that leaders at all levels perform to ensure operational excellence. It aligns perfectly with the Lean philosophy of continuous improvement and the Six Sigma methodology's focus on process efficiency and quality. The real purpose behind Leader Standard Work is the systematic creation and adherence to Standard Operating Procedures (SOPs) to promote uniformity, accountability and consistency in each task. Leader Standard Work empowers leaders to actively engage with frontline processes, monitor performance metrics, and identify opportunities for improvement within leadership processes. Organisations can cultivate a culture of continuous improvement, boost leadership effectiveness, and enhance operational efficiency by incorporating LSW into daily practices.
The 5 Principles of Leader Standard Work include:
- Offering immediate coaching and guidance
- Building from the foundation
- Establishing standardised processes
- Enhancing visibility across operations
- Upholding and maintaining initiated practices
Why should organisations Implement Leader Standard Work?
Leader Standard Work establishes standardised practices, promoting consistency, transparency, and accountability in daily operations. LSW contributes to adaptability, employee engagement, and sustained excellence by actively involving leaders in daily routines. It aligns leadership activities with organisational goals, emphasising data-driven decision-making and providing a structured approach for ongoing refinement. Ultimately, LSW is a strategic tool that optimises current operations and positions organisations to thrive in dynamic and competitive environments through sustained improvement and effective leadership.
How does Leader Standard Work differ from other Management approaches?
Leader Standard Work (LSW) distinguishes itself from other management approaches by emphasising the direct involvement of leaders in daily operational routines. Unlike traditional top-down management, LSW fosters a culture of continuous improvement by having leaders actively engage with frontline processes. This approach prioritises real-time observation, problem-solving, and coaching, promoting consistency and accountability. LSW aligns with Lean principles, emphasising standardised processes and direct leadership involvement in sustaining excellence. This sets it apart from conventional management styles, making it a dynamic and proactive methodology tailored to enhance operational efficiency and leadership effectiveness.
What Benefits can organisations expect from Implementing Leader Standard Work?
- Operational Consistency: Leader Standard Work establishes and enforces standardised processes, ensuring consistency and reliability in daily operations.
- Continuous Improvement: Through real-time engagement, LSW fosters a culture of continuous improvement, allowing for the identification and implementation of enhancements.
- Enhanced Leadership Effectiveness: Leader Standard Work empowers leaders to actively participate in frontline processes, leading to more effective decision-making and problem-solving.
- Accountability and Visibility: The approach enhances accountability by making work processes visible, promoting organisational transparency and accountability.
- Adaptability and Flexibility: Leaders, through LSW, gain insights into operational dynamics, enabling quick adaptation to changing conditions and fostering organisational flexibility.
- Employee Engagement: By involving leaders in daily routines, LSW contributes to increased employee engagement, as team members feel supported and connected to leadership.
- Optimised Resource Utilisation: LSW facilitates the efficient use of resources by addressing gaps between standard and actual work, reducing waste and enhancing operational efficiency.
- Strategic Alignment: The practice aligns daily activities with organisational goals, contributing to strategic alignment and ensuring that efforts support broader objectives.
- Sustainable Excellence: LSW instils a mindset of sustained excellence, where leaders directly maintain and improve operational standards over time.
Schedule a Demo to find out how your Organisation can benefit from implementing LSW
Steps to Implement Leader Standard Work effectively
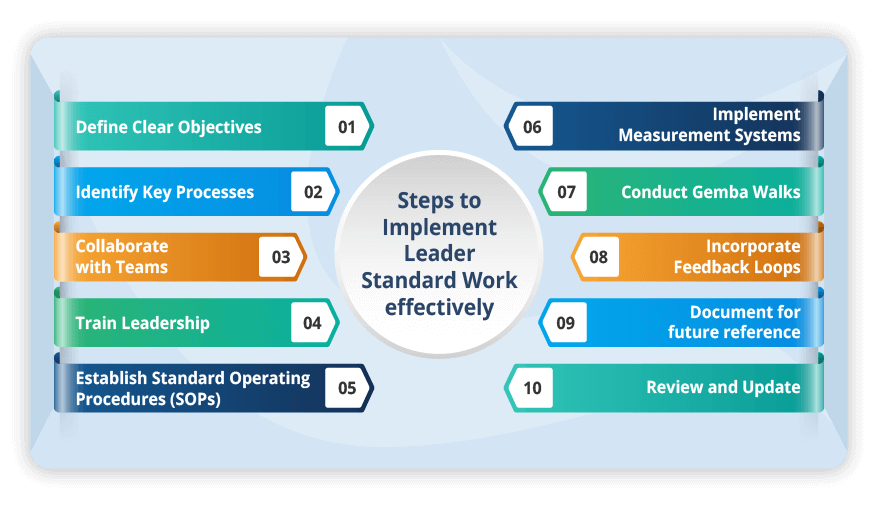
- Define Clear Objectives: Clearly articulate the objectives of implementing Leader Standard Work, aligning them with organisational goals and continuous improvement.
- Identify Key Processes: Identify critical processes directly impacting organisational success and performance.
- Collaborate with Teams: Engage with teams to develop standardised processes collaboratively, ensuring a shared understanding and commitment.
- Train Leadership: Provide comprehensive training to leaders on the principles and practices of Leader Standard Work, emphasising their role in daily routines.
- Establish Standard Operating Procedures (SOPs): Develop clear and standardised operating procedures, documenting each step of key processes to ensure consistency.
- Implement Measurement Systems: Integrate monitoring and tracking systems like T cards or Kanban boards to track performance metrics, allowing for data-driven insights and continuous improvement.
- Conduct Gemba Walks: Encourage leaders to actively participate in Gemba Walks, gaining firsthand observations of operational processes and challenges.
- Incorporate Feedback Loops: Establish regular feedback loops to capture insights from leaders and frontline workers, fostering continuous refinement.
- Document for future reference: Develop detailed documentation of Leader Standard Work (LSW) procedures to establish a reference resource for future guidance.
- Review and Update: Periodically review and update Leader Standard Work processes to adapt to evolving organisational needs and changes in the operational environment.
How Digital Solutions enhance the Implementation of Leader Standard Work?
Digital solutions help implement Leader Standard Work (LSW), providing efficiency, accessibility, and real-time insights. Here's how various digital tools contribute to Leader Standard Work:
- T Cards: Digital T Card streamline task management by digitising the visualisation of work processes. This improves transparency, facilitates quicker updates, and ensures that tasks are managed seamlessly.
- Kanban Board: Digital Kanban boards facilitate real-time updates, seamless task tracking, and efficient workflow management, contributing to the effective implementation of Leader Standard Work.
- Performance Analytics Software: Digital tools like Balanced Scorecard software enable leaders to efficiently analyse Key Performance Indicators (KPIs) related to their specific areas of responsibility. It allows leaders for data-driven decision-making and facilitates a deeper understanding of operational performance.
- Kamishibai Board: Digital Kamishibai boards confirm the prompt execution of shop floor processes and make it easy to schedule, track, and analyse process audits. This enhances visibility, ensures regular audit checks, and allows for prompt corrective actions if necessary.
( Checkout How to Streamline Leader Standard Work with Kamishibai Boards)
- Gemba Boards: Digital Gemba boards enable leaders to engage in Virtual Gemba, facilitating remote observations and discussions. It ensures that the principles of Gemba Walks are maintained, even in a digital environment.
- LSW Templates: Digital LSW templates streamline the creation and maintenance of standardised work procedures. They provide a centralised platform for leaders to access, update, and communicate Standardised Operating Procedures (SOPs), ensuring consistency and easy reference.
Key Practices within Leader Standard Work
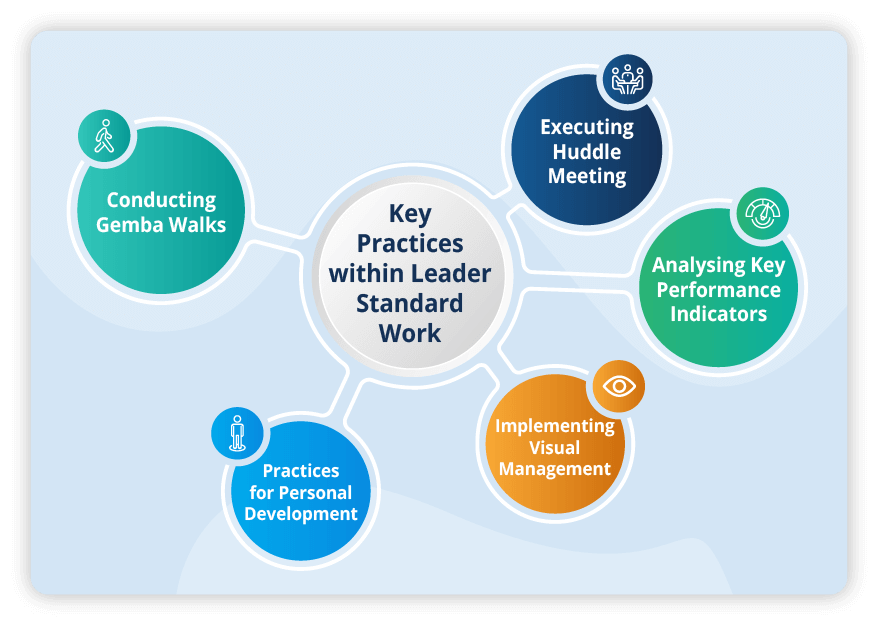
- Conducting Gemba Walks: Gemba Walks leaders actively engage with the actual workplace to observe, understand, and interact with daily operations. This practice provides first hand insights, fosters continuous improvement, and ensures leaders remain closely connected to frontline processes.
- Executing Huddle Meeting: Huddle meetings are regular gatherings where leaders and teams discuss progress, challenges, and action items. These short and focused meetings enhance communication, alignment, and the swift resolution of operational issues.
- Analysing Key Performance Indicators: Leaders regularly analyse Key Performance Indicators (KPIs) relevant to their areas of responsibility. It involves assessing metrics related to efficiency, quality, and other critical factors to make informed decisions and identify opportunities for improvement.
- Implementing Visual Management: Visual management involves using visual tools such as Kanban boards, Tcards or Kamishibai boards to understand shop floor processes and performance easily. This practice enhances transparency, allowing leaders to grasp the status of operations and make data-driven decisions quickly.
- Practices for Personal Development: Personal development is a key aspect of Leader Standard Work, focusing on continuous improvement for leaders themselves. With constant learning, skill development, and self-reflection to enhance leadership effectiveness and contribute to the organisation's overall growth.
How often should Leader Standard Work be performed?
The frequency of Leader Standard Work (LSW) execution depends on organisational needs and the nature of operations. Typically, LSW should be performed regularly, integrating it into daily, weekly or monthly routines to ensure consistent leadership engagement with frontline processes. This regularity allows leaders to maintain a real-time understanding of operational dynamics, address emerging issues promptly, and actively contribute to continuous improvement.
What are the Benefits of Standardising a Manager’s Daily Work?
Standardising a manager's daily work yields several advantages like fostering consistency, efficiency, and accountability.
- Enhances consistency and efficiency in daily operations.
- Facilitates clear expectations and responsibilities.
- Streamlines communication and decision-making processes.
- Establishes a foundation for continuous improvement and performance measurement.
- Promotes a structured approach to tasks and priorities.
Standardising Leadership Tasks involves several steps:
- Conducting Process Audits: Regular audits ensure adherence to standardised processes, identify deviations and provide insights for continuous improvement.
- Performing Daily Checks: Daily checks or proactive Gemba Walks allow leaders to observe operations firsthand, identify issues, and actively engage with frontline processes.
- Providing Training: Comprehensive training ensures leaders understand and consistently apply standardised procedures, enhancing overall effectiveness.
- Conducting Tiered Meetings: Implementing tiered meetings establishes a structured communication framework, promoting consistent information flow and alignment across different levels of leadership.
- Implementing Visual Management Tools: Visual management tools, such as performance dashboards or Kanban boards, enhance transparency, making standardised processes and performance metrics easily accessible and understandable for leaders.
Is Leader Standard Work Applicable for various Industries?
Yes, Leader Standard Work (LSW) has a versatile approach that transcends industrial boundaries and applies to various sectors. Its principles and practices can be effectively implemented in industries such as manufacturing, automotive, plant hire, service sectors, healthcare, pharmaceuticals, and more. The adaptability of LSW makes it a valuable tool for driving continuous improvement across diverse industries.
Is Leader Standard Work only for Top-level executives?
LSW is designed for leaders at all levels of the organisation, ensuring that everyone in a leadership role is actively engaged in supporting and driving continuous improvement. Leader Standard Work (LSW) is performed by leaders at various hierarchical levels having specific contributions to the process as it is a collective responsibility for achieving organisational success.
- Team Leaders: Team leaders actively engage in LSW by implementing and adhering to standardised processes, ensuring team members follow established procedures, and participating in Gemba Walks to observe and address operational challenges.
- Middle Managers: Middle managers conduct more comprehensive LSW, overseeing multiple teams or departments. They play a pivotal role in aligning operational activities with organisational goals, analysing performance indicators, and providing regular feedback to both team leaders and upper management.
- Executives: As top-level leaders, executives champion the integration of LSW into the organisational culture. They set the tone for a commitment to continuous improvement, regularly review Key Performance Indicators, and provide strategic guidance to middle managers and team leaders to ensure LSW aligns with the organisation's vision and goals.
Overcoming potential Challenges while Implementing Leader Standard Work
- Lack of Clear Documentation: Develop clear and accessible documentation for standardised processes, tasks, and expectations.
- Technological Barriers: Invest in user-friendly digital tools and provide training on their use. Ensure accessibility and support for employees adapting to new technologies.
- Lack of Measurement and Feedback Mechanisms: Implement robust measurement systems like T cards or Kanban boards to track the effectiveness of LSW. Establish feedback loops for continuous improvement and real-time adjustments.
- Failure to Align with Organisational Goals: Ensure LSW is directly aligned with organisational goals. Regularly review and adjust LSW practices to maintain alignment with strategic objectives.
Example for Leader Standard Work
Consider a scenario of Leader Standard Work (LSW) in a Manufacturing sector, specifically focusing on a production supervisor. The LSW for the production supervisor may involve the following step-by-step processes:
Morning RoutineObjective: Start the day prepared and informed.
- Tasks to be performed:
- Check the production schedule for the day.
- Review any overnight production reports.
- Conduct a brief team huddle to discuss daily goals and address any immediate concerns.
Objective: Engage with frontline processes and address real-time issues.
- Tasks:
- Conduct a Gemba Walk to observe production lines.
- Interact with operators to gather insights and address concerns.
- Document observations and identify opportunities for improvement.
Objective: Ensure product quality and compliance.
- Tasks:
- Review quality control metrics and reports.
- Conduct on-the-spot quality checks at different production stages.
- Collaborate with the quality assurance team to address any deviations.
Objective: Analyse Key Performance Indicators (KPIs).
- Tasks:
- Review production output against targets.
- Analyse efficiency metrics, such as downtime and cycle times.
- Identify trends and areas for improvement.
Objective: Foster team collaboration and communication.
- Tasks to be performed:
- Conduct regular tiered meetings with team leaders.
- Address concerns and challenges raised by team members.
- Recognise and celebrate achievements and milestones.
Objective: Address and resolve operational issues.
- Tasks to be performed:
- Hold a daily problem-solving session with relevant team members.
- Utilises root cause analysis to address recurring issues.
- Implement corrective actions and preventive measures.
Objective: Summarise the day's performance and plan for the next day.
- Tasks:
- Review end-of-day production reports.
- Conduct a brief team debrief to discuss successes and areas for improvement.
- Update the production schedule and plan for the next shift.
Ready to embed Leader Standard Work into your daily operations?
Streamline your processes, enhance team accountability, and sustain improvements with the right LSW tool.