What is a Daily Management System (DMS)?
Utilising a Daily Management System boosts efficiency, enhances communication, and promptly addresses shop floor issues.
Get Started with DMS Schedule a DemoContents
- What is a Daily Management System (DMS)?
- What are the benefits of implementing a Daily Management System in various organisations?
- Significance of TCards in a Lean Daily Management System (LDMS)
- How do you create an effective Daily Management System?
- Best practices for setting up and maintaining an effective Daily Management Board
- How can Daily Management Systems be adapted for virtual teams?
- Visual Management vs. Traditional Methods
- What are the Key metrics and indicators organisations should track on their Daily management boards?
- What are the key components of a Daily Management Board?
- How can organisations integrate the Daily Management System with Quality Management Systems (QMS)?
- Tools and Techniques in Daily Management System
- How does a Daily Management System (DMS) enhance the effectiveness of Layered Process Audits (LPAs)?
- How do Daily Management Systems support environmental initiatives and contribute to sustainability goals?
- Must have features while selecting a Daily Management System for your organisation
- How does the Daily Management System contribute to continuous improvement in an organisation?
- Example of Daily Management System implementation
What is a Daily Management System (DMS)?
A Daily Management System (DMS) is an organised and structured approach to organisational management that focuses on real-time, daily operational control and continuous improvement. Unlike traditional management approaches, the Daily Management System prioritises using visual management tools, daily huddles, and standardised processes to enhance communication, identify and resolve issues promptly, and promote a culture of accountability. Key components of a Daily Management System include:
- Daily Accountability Process
- Leader Standard Work
- Gemba Walks
- Process Confirmation
The primary objectives of the Daily Management System are to drive operational excellence, reduce variation, and foster a proactive problem-solving culture, enabling organisations to adapt swiftly to changes and consistently meet performance targets. Key principles of Daily Management Systems include:
- Visual Management: Utilise visual tools like charts and boards to display Key Performance Indicators and real-time information, enhancing transparency and facilitating quick decision-making.
- Employee Engagement: Foster active participation and commitment from team members through daily huddles and collaborative problem-solving, promoting a sense of ownership and accountability.
- Problem-Solving: Encourage a proactive approach to identifying and resolving issues at their root causes, driving continuous improvement and preventing recurring problems.
- Communication and Collaboration: Establish regular team communication channels, such as daily huddles, to facilitate open dialogue, share updates, and align priorities, promoting a culture of collaboration.
- Continuous Improvement: Cultivate a mindset of ongoing enhancement by systematically identifying areas for improvement and implementing changes to optimise processes and performance.
What are the benefits of implementing a Daily Management System in various organisations?
The Daily Management System (DMS) is a versatile tool across industries, optimising operations and promoting continuous improvement. In the Manufacturing industry, it enhances production efficiency through real-time monitoring. Automotive industries use DMS for streamlined supply chains. DMS ensures project timelines through task visibility in the Plant hire industry and Construction sector. The Pharmaceutical sector relies on DMS for quality control and compliance standards. The Daily Management System also finds its application in the Healthcare industry, Service sector, HVAC industry, Marine industry, Aerospace and many more.
- Improved Visibility: Enhances visibility into daily operations through visual tools, allowing teams to monitor performance and identify issues promptly.
- Enhanced Communication: Facilitates regular communication through daily huddles and standardised processes, ensuring that information flows effectively within the organisation.
- Proactive Issue Resolution: Encourages a proactive problem-solving culture, enabling teams to address issues at their root causes and prevent recurring problems.
- Increased Employee Engagement: Engages employees in decision-making, fostering ownership and accountability for daily tasks and overall performance.
- Standardised Work Practices: Promotes the adoption of standardised work processes, reducing variability and ensuring consistency in operations.
- Faster Decision-Making: Provides real-time information, enabling quicker decision-making and response to changes in the operational environment.
- Continuous Improvement: Contributes to a culture of continuous improvement, allowing organisations to adapt swiftly to changing conditions and consistently refine their processes for optimal efficiency.
- Goal Alignment: Aligns daily activities with organisational goals, ensuring that daily tasks contribute to the overall success and strategic objectives of the organisation.
- Increased Accountability: Establishes a framework for accountability, as teams regularly review and discuss performance metrics, making it clear who is responsible for specific tasks and outcomes.
- Quality Management: Ensures adherence to quality standards and compliance requirements within the organisation. For example, Daily Management Systems (DMS) in the pharmaceutical sector play a crucial role in maintaining and improving quality control processes.
Significance of TCards in a Lean Daily Management System (LDMS)
T-Cards play a crucial role in a Lean Daily Management System (LDMS) by serving as visual tools for tracking and managing workflow. Tcards are typically colour-coded for different tasks or stages, and are placed on a T card board to represent work status in real time. The significance lies in their ability to provide instant visual cues, allowing teams to identify bottlenecks, monitor progress, and address issues promptly. Tcards enhance transparency, facilitate quick decision-making, and contribute to the overall efficiency and effectiveness of LDMS by promoting visual control and standardised communication within the organisation.
How do you create an effective Daily Management System?
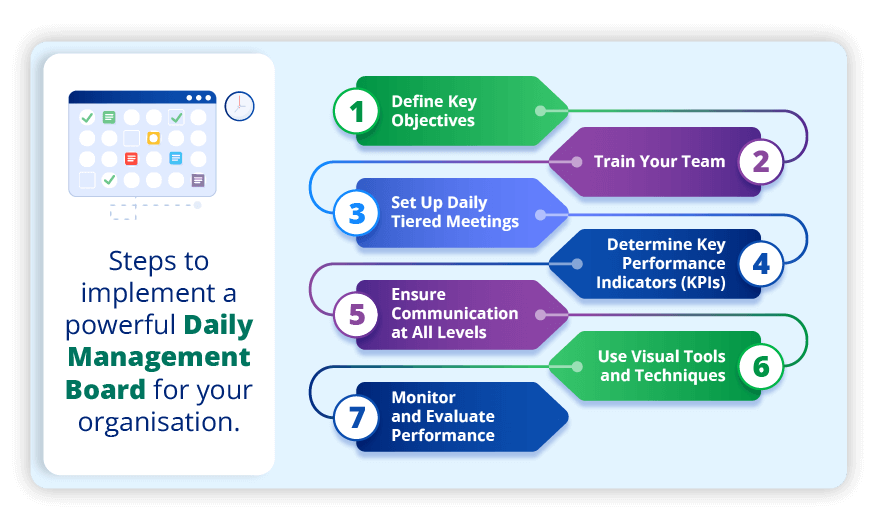
Here are the steps you should take to implement a powerful Daily Management Board for your organisation.
- Define Key Objectives: Clearly articulate the organisation's goals and objectives that the Daily Management System (DMS) aims to support, ensuring alignment with overall strategic priorities.
- Train Your Team: Train employees at all levels on the principles and processes of DMS, ensuring a shared understanding and commitment to the system.
- Set Up Daily Tiered Meetings: Establish daily huddles or tiered Meetings where teams can discuss progress, address challenges, and align priorities to enhance communication and collaboration.
- Determine Key Performance Indicators (KPIs): Identify and define relevant KPIs that align with organisational objectives, enabling teams to measure and track performance consistently.
- Ensure Communication at All Levels: Establish clear communication channels from top management to frontline employees, fostering an environment where information flows seamlessly and issues are addressed promptly.
- Use Visual Tools and Techniques: Implement visual management tools such as boards, charts, and cards to make data and progress visible, enhancing transparency and facilitating quick decision-making.
- Monitor and Evaluate Performance: Regularly review and assess the effectiveness of the DMS, collecting feedback and data to identify improvement areas and ensuring continuous system enhancement.
Best practices for setting up and maintaining an effective Daily Management Board
- Clear Layout with Visuals: Design an organised Daily management board using colour-coded sections, labels, and visuals to easily comprehend task status and KPIs, promoting clarity and reducing misinterpretation.
- Real-Time Updates Culture: Foster a culture of real-time updates on the Daily management board to maintain accurate task and progress information, facilitating prompt decision-making and preventing operational disruptions.
- Standardised Formats: Use standardised formats for data representation, task cards, and Key Performance Indicators to maintain consistency and make it easy for team members to interpret information uniformly.
- Daily Team Huddles: Conduct daily huddles or tiered meetings around the Daily management board to encourage open communication, discuss updates, address challenges, and collectively problem-solve, reinforcing a sense of responsibility and engagement.
- Feedback for Improvement: Establish a continuous improvement feedback loop by regularly reviewing the Daily management board's effectiveness. Encourage team input on layout, content, and usability, using feedback to make iterative enhancements and maintain the board's value.
How can Daily Management Systems be adapted for virtual teams?
Adapting Daily Management Systems for virtual teams involves utilising digital tools and fostering online collaboration. Implement virtual dashboards or project management platforms like Tcards to replace physical boards, ensuring real-time visibility of Key Performance Indicators. Conduct daily virtual huddles using video conferencing to facilitate team communication, alignment, and issue resolution. Emphasise using shared digital documents for standardised work procedures and collaborative problem-solving. Maintain a focus on visual management through online charts and graphics. Regularly assess the effectiveness of virtual systems, seeking feedback to optimise communication and performance tracking for dispersed teams continually.
Visual Management vs. Traditional Methods
Visual Management differs from traditional management methods by employing visual aids such as charts, dashboards, and Kanban boards, enabling a real-time and intuitive approach to monitoring and managing daily operations. Unlike conventional text-based reports, Visual daily management enhances transparency, accelerates decision-making, and facilitates quick issue identification. This paradigm shift promotes collaboration, engages teams through accessible data, and fosters a culture of continuous improvement. The dynamic visual representation of Key Performance Indicators in visual management boards replaces the dependence on manual tracking, contributing to increased efficiency within the organisational framework.
What are the Key metrics and indicators organisations should track on their Daily management boards?
The key metrics and indicators organisations should track on their Daily Management Boards can vary depending on the industry, goals, and specific needs of the organisation.
It's important to have a balanced combination of leading and lagging indicators to gain a thorough understanding of the performance of an organisation. These metrics should be consistent with the organisation's strategic objectives and must be reviewed and updated to make sure they stay relevant to the changing requirements of the business. However, some common metrics that the organisation tracks include:
- Production Metrics
- Daily production output
- Cycle time
- Scrap or defect rates
- Quality Metrics
- First-pass yield
- Customer complaints or returns
- Defect rate
- Safety Metrics
- Number of accidents or incidents
- Safety training completion rates
- Delivery Metrics
- On-time delivery
- Order fulfilment cycle time
- Financial Metrics
- Daily sales
- Cost of goods sold
- Revenue and profit margins
- Inventory Metrics
- Inventory levels
- Stockouts or excess inventory
- Employee Performance Metrics
- Work completion rates
- Attendance and punctuality
- Employee engagement or satisfaction
- Customer Satisfaction Metrics
- Customer feedback
- Net Promoter Score (NPS)
- Service response times
- Process Efficiency Metrics
- Downtime
- Equipment utilisation rates
- Process cycle time
- Continuous Improvement Metrics
- Number of implemented improvement ideas
- Kaizen events or initiatives
Get a Personalised Demo to understand which metrics need to be tracked on your DMS Board!
What are the key components of a Daily Management Board?
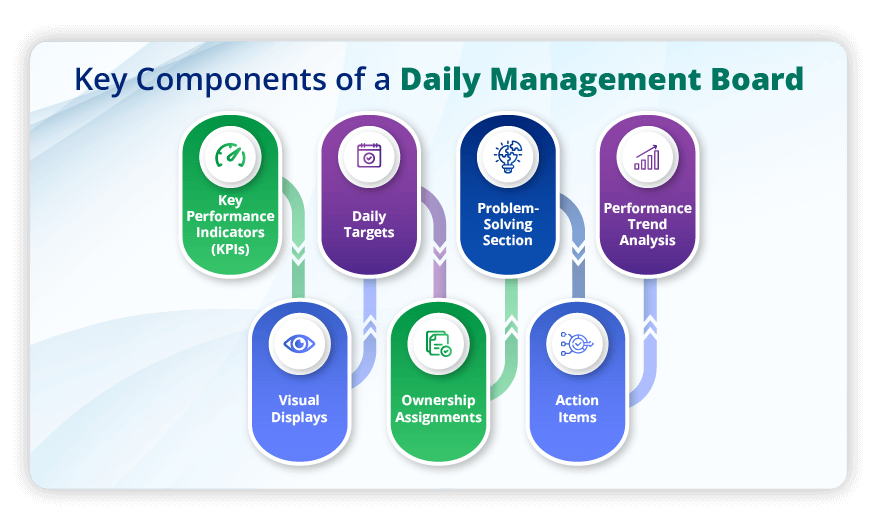
- Key Performance Indicators (KPIs): Identify and display the critical metrics that align with organisational goals and objectives. These include production output, quality metrics, safety records, and customer satisfaction indices.
- Visual Displays: Visual displays enhance the quick absorption of information and facilitate faster decision-making.
- Daily Targets: Set clear and achievable daily targets for each key metric. These targets provide a benchmark for performance and help teams understand their daily objectives.
- Ownership Assignments: Assign responsibilities for each KPI to specific individuals or teams. This fosters accountability and ensures someone is accountable for monitoring and improving each metric.
- Problem-Solving Section: Allocate space for addressing issues or challenges encountered during daily operations. This section can include notes on problems, their root causes, and proposed or implemented solutions.
- Action Items: Outline specific actions that need to be taken to address issues or improve performance. Assign responsible parties and deadlines to ensure timely resolution and continuous improvement.
- Performance Trend Analysis: Include historical data reports or performance trends to provide context and enable comparing current performance against past benchmarks. This aids in identifying patterns and areas for improvement.
How can organisations integrate the Daily Management System with Quality Management Systems (QMS)?
Organisations can seamlessly integrate Daily Management Systems (DMS) with their existing Quality Management Systems (QMS) by establishing clear alignment between daily operational activities and overarching quality objectives. Incorporating relevant quality metrics into Daily Management Systems ensures that routine tasks contribute directly to quality standards and compliance requirements. By leveraging visual tools, teams can monitor Key Performance Indicators in real-time, identify deviations, and promptly initiate corrective actions. This integration promotes a proactive quality culture, synchronising continuous improvement efforts with daily operations and reinforcing adherence to established quality processes.
Tools and Techniques in Daily Management System
- Andon Systems: In manufacturing, visual signalling systems often alert teams to real-time issues or abnormalities, facilitating immediate responses to production problems.
- Visual Management Tools: Various tools like visual cues, labels, and colour-coded systems enhance communication and understanding in the workplace. Visual Management boards like Kanban boards, T cards and Kamishibai boards contribute to the visual aspect of daily management, making information more accessible.
- Gemba Walks: A technique where managers or team leaders observe operations firsthand in the actual work environment (Gemba) to gain insights, identify opportunities for improvement, and engage with frontline employees.
- 5S (Sort, Set in order, Shine, Standardise, Sustain): 5S is a structured and systemic approach to workplace organisation and standardisation. Involves organising the workplace for efficiency, cleanliness, and safety, leading to improved productivity and reduced waste.
- Daily Huddles or Stand-up Meetings: Brief, regular team meetings held at the beginning or end of the day to discuss goals and priorities and address any immediate issues. It promotes communication and alignment in organisations at every level. Huddle Boards can help teams with daily huddle meetings, ensuring consistency at every stage.
- A3 Problem Solving: A3-sized structured problem-solving approach involving documenting problems, analysis, proposed solutions, and action plans on one sheet.
- PDCA (Plan-Do-Check-Act) Cycle: A continuous improvement cycle that involves planning a change, implementing it, checking the results, and acting on the lessons learned. Iterative use of the PDCA cycle drives ongoing improvement.
- Standard Work: Document the best-known practices for a particular process, ensuring consistency and efficiency. Standard Work serves as a baseline for continuous improvement efforts.
- Root Cause Analysis: It is a systemic methodology identifying the fundamental reasons behind problems or deviations. Common techniques include the "5 Whys" and fishbone diagrams, assisting teams to address issues at their source.
How does a Daily Management System (DMS) enhance the effectiveness of Layered Process Audits (LPAs)?
A Daily Management System (DMS) enhances Layered Process Audits (LPAs) by fostering a continuous improvement culture. Regular Daily Management System integration makes LPAs seamlessly embedded into daily operations, ensuring consistent monitoring and corrective actions. Daily Management System's real-time visibility enables swift identification of potential issues, allowing proactive responses and minimising the risk of process deviations. Leader standard work further amplifies this effectiveness, providing a structured framework for leaders to actively participate in and support the integration of LPAs into daily routines. This synergy between DMS, LPAs, and leader standard work promotes operational excellence, quality assurance, and sustained process improvement within the organisation.
Streamline your LPAs with Daily Management Boards!
How do Daily Management Systems support environmental initiatives and contribute to sustainability goals?
The Daily Management System (DMS) is pivotal in supporting environmental initiatives and contributing to sustainability goals through efficient digitalisation. Daily Management System reduces environmental impact by transitioning to digital platforms from traditional paper-based processes, thereby minimising deforestation. This shift towards digital practices enhances operational efficiency and aligns with sustainability objectives, promoting a greener and eco-friendly approach. In essence, DMS stands as a key enabler in pursuing environmentally responsible practices and attaining sustainability targets.
Must have features while selecting a Daily Management System for your organisation
- User-Friendly Interface: A Daily Management System should have an user-friendly interface, ensuring easy adoption across all levels of the organisation. This feature promotes widespread engagement and efficient system use without extensive training.
- Customisation Capabilities: The ability to customise workflows, forms, and reports is crucial to tailor the Daily Management System to the specific needs and processes of the organisation. This ensures flexibility and adaptability to evolving business requirements.
- Real-Time Data Visibility: Providing real-time data visibility is essential for effective decision-making. A robust Daily Management System should offer dashboards and analytics tools with instant insights into Key Performance Indicators, enabling timely and informed actions.
- Mobile Accessibility: Accessing the Daily Management System from mobile devices is crucial for a modern workplace. This feature lets users stay connected and manage tasks from anywhere, boosting productivity and responsiveness.
- Integration with Existing Systems: Compatibility and integration with existing software systems (e.g., CRM, ERP) are vital for a smooth implementation. This feature streamlines processes, reduces data silos and ensures a cohesive digital ecosystem within the organisation.
- Security Measures: Robust security features, including data encryption, access controls, and authentication protocols, are imperative to safeguard sensitive organisational information. A secure Daily Management System instils confidence in users and protects against potential cybersecurity threats.
- Scalability: As organisational needs evolve, the Daily Management System should be scalable to accommodate growth. This ensures the system can adapt to increased data volumes, additional users, and expanding functionalities without compromising performance.
- Comprehensive Training and Support: A reliable Daily Management System should have comprehensive training materials and ongoing support to facilitate a smooth implementation process. This feature ensures users can maximise the system's potential and troubleshoot issues effectively.
- Audit Trail and Compliance: The system should maintain a detailed audit trail to track changes and user activities, ensuring accountability and compliance with industry regulations. This feature is crucial for organisations operating in regulated environments.
How does the Daily Management System contribute to continuous improvement in an organisation?
The Daily Management System (DMS) serves as a catalyst for continuous improvement within an organisation by providing a structured framework for monitoring, analysing, and enhancing daily operations. By providing real-time visibility into data, the DMS helps teams identify inefficiencies, bottlenecks, and areas for improvement daily. The system facilitates swift problem-solving and decision-making by offering immediate insights into Key Performance Indicators. Additionally, the Lean Daily Management System (LDMS) supports a culture of accountability and transparency, fostering collaboration among team members. The DMS creates a dynamic environment that encourages continuous improvement initiatives by automating workflows, streamlining communication, and promoting data-driven decision-making. Overall, the Daily Management System (DMS) is a systemic and structured approach that enhances organisational efficiency and facilitates continuous improvement.
Example of Daily Management System implementation
A hospital experienced frequent delays in patient discharge, leading to extended wait times for incoming patients and potential overcrowding in the emergency department. The healthcare sector implemented a Daily Management System to address this challenge and enhance patient care and operational efficiency.
The Daily Management System included features such as:
- Real-time tracking of patient flow
- Customised workflows for discharge processes
- Displays key metrics like bed turnover times and discharge rates.
By implementing the Daily Management System, the hospital staff collaboratively:
- Identifies bottlenecks in the discharge process
- Minimises delays caused by paperwork
- Ensure communication and coordination between departments.
For example, a digitalised discharge checklist is introduced to streamline record keeping, and a communication protocol is established to enhance interdepartmental coordination.
As a result, the hospital experiences a significant reduction in patient discharge times, leading to increased bed availability and improved emergency department flow.
Take Control of your Daily Management Process
Get started with your own Daily Management System today to boost productivity and streamline operations.