Setting up a Lean Daily Management System
August 21, 2023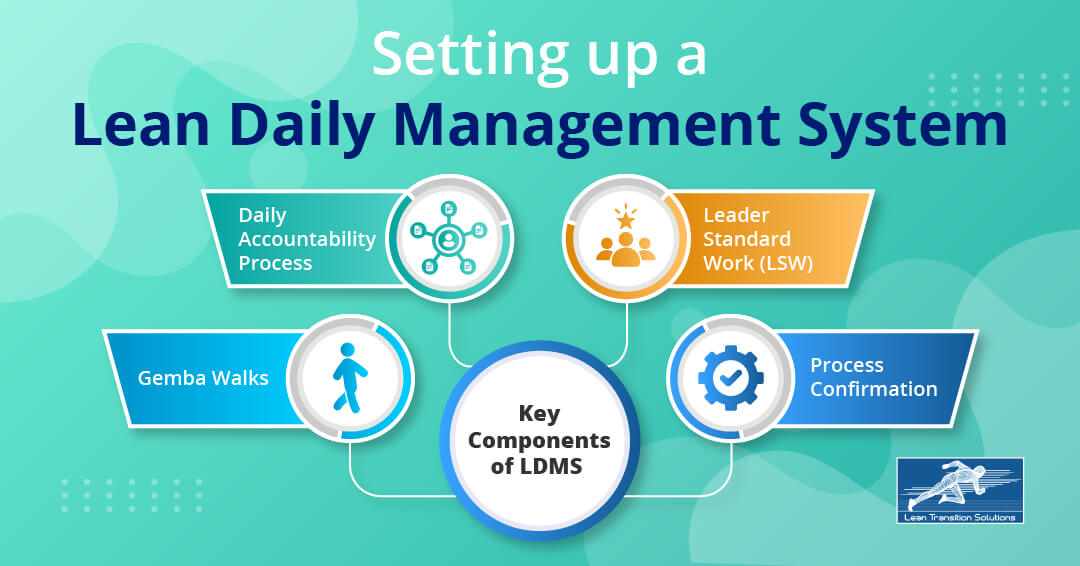
Lean principles aim to improve efficiency and reduce waste to streamline operations. Establishing a Lean Daily Management System (LDMS) is crucial for fostering an organisation's continuous improvement culture. LDMS provides a structured framework that enables teams to monitor performance, identify issues, and implement immediate corrective actions.
Organisations can optimise processes and enhance accountability, contributing to sustained growth and operational excellence. Let’s understand how you can implement a Lean Daily Management System in your organisation for improved problem-solving ability and increased productivity.
What is a Lean Daily Management System (LDMS)?
A Lean Daily Management System (LDMS) integrates lean principles into daily operations through an organised approach. It involves processes and tools for tracking, managing, and improving performance at all levels of an organisation. The LDMS aims to create a culture of continuous improvement by promoting transparency, accountability, and effective communication, ultimately driving operational excellence and sustainable growth.
Understanding key Components of LDMS
Key components of a Lean Daily Management System (LDMS) encompass the Daily Accountability Process, which ensures transparency and ownership, Leader Standard Work that sets expectations and routines, Gemba Walks enabling direct observation and improvement, and Process Confirmation verifying adherence. These components collectively empower organisations to streamline operations, enhance communication, and continuously elevate performance through systematic and data-driven practices.
- Daily Accountability Process: The Daily Accountability Process within a Lean Daily Management System (LDMS) provides a structured approach to monitoring and tracking daily tasks and progress. The Daily Accountability system fosters transparency, giving teams a clear view of ongoing activities. It also promotes ownership, encouraging individuals to take responsibility for their tasks. The daily accountability process can be considered as a fundamental pillar for ongoing organisational improvement.
- Leader Standard Work (LSW): Leader Standard Work (LSW) is a pivotal element of LDMS, encompassing the routines and expectations for leaders throughout the organisation. LSW defines consistent routines, outlining specific tasks and priorities that leaders engage in daily. This practice ensures leaders allocate time effectively, engage with teams, and focus on strategic initiatives. By adhering to LSW, leaders establish a foundation of reliability, effective communication, and strategic alignment within the organisation.
- Gemba Walks: Gemba Walks, a fundamental aspect of LDMS, holds a significant purpose in fostering direct observation, engagement, and continuous improvement. These walks involve leaders and managers engaging with the shop floor or work areas to gain firsthand insights. Gemba walks offer a unique opportunity to identify improvement opportunities, address challenges, and enhance communication between leadership and frontline teams. By actively participating in Gemba walks, organisations harness real-time information to drive informed decision-making and cultivate a culture of collaboration.
- Process Confirmation: Process Confirmation serves as a vital quality assurance component within LDMS. It involves systematically verifying adherence to standard work processes. This practice ensures consistency and identifies any deviations from established procedures. By promptly detecting deviations, teams can take immediate corrective actions to prevent potential issues and maintain process integrity. Process Confirmation contributes to overall process efficiency, supports continuous improvement efforts, and upholds the organisation's commitment to delivering high-quality products or services.
Utilising Tools to enhance LDMS effectiveness
- Kamishibai Board: The Kamishibai board stands as a powerful visual management tool that amplifies the effectiveness of the Lean Daily Management System (LDMS). Its visual management concept provides a clear overview of tasks and processes. The Kamishibai board guides Leader Standard Work (LSW), and Gemba walks through scheduled audits, ensuring that leaders engage with critical activities, verify adherence to standards, and address process gaps. This powerful tool enhances accountability, improves processes, and facilitates communication, increasing efficiency and engagement for LDMS.
- Role of T Cards in structuring and organising daily tasks: T cards represent individual tasks or activities and are systematically arranged to create a visual schedule. By assigning tasks on T cards, teams gain a tangible representation of their workload, promoting better time management and efficient task execution. The structured arrangement of T cards provides clarity, enhances coordination, and empowers teams to prioritise tasks effectively, ultimately contributing to the seamless implementation of LDMS principles.
- Kanban Boards as a Lean Daily Management System: Integrating Kanban boards into the Lean Daily Management System enhances its capabilities by introducing a visual method for mapping workflows and managing tasks. These boards offer a comprehensive visual representation of work processes, aiding in identifying bottlenecks, optimising flow, and facilitating real-time decision-making. Aligning Kanban principles with LDMS principles augments transparency and responsiveness, enabling teams to quickly adapt to changes, allocate resources efficiently, and promote a culture of continuous improvement. Kanban boards thus become a perfect tool for LDMS, amplifying its impact on operational excellence.
5 Steps for Implementing Lean Daily Management System (LDMS) effectively
- Defining LDMS Objectives and Goals: The initial step in implementing an effective Lean Daily Management System (LDMS) involves clearly defining the objectives and goals you intend to achieve. Establishing these goals provides a strategic direction for LDMS implementation, aligning the system with the organisation's overall vision. Whether it's enhancing productivity, reducing waste, or improving quality, articulating specific objectives sets the stage for a focused and successful LDMS rollout.
- Mapping Processes and Identifying Key Metrics: Mapping your organisational processes and identifying Key Performance Indicators (KPIs) are fundamental to LDMS implementation. To identify areas for improvement, it is crucial to have a clear understanding of how work flows within your organisation. Identifying relevant metrics ensures that you track the right data to measure progress and success. This step lays the foundation for a data-driven approach to LDMS, enabling informed decision-making and targeted improvements.
- Creating Leader Standard Work (LSW) and Gemba Walk Plans: Leader Standard Work (LSW) and Gemba Walk plans are integral to LDMS. Developing LSW involves outlining leaders' daily tasks, routines, and responsibilities at all levels. Gemba Walk defines how leaders engage with the shop floor to observe processes, interact with employees, and identify improvement opportunities. Creating comprehensive LSW and Gemba Walk ensures that leadership practices align with LDMS principles, fostering accountability and continuous improvement.
- Designing and implementing Kamishibai Boards and T Cards: The Kamishibai boards and T Cards provide a visual management structure necessary for LDMS success. Kamishibai boards visually guide audits and tasks, ensuring that processes are audited, and leaders engage with essential activities. T Cards organises daily tasks, promoting efficient time management and task prioritisation. Designing and implementing these tools effectively enables teams to visualise their work, track progress, and maintain alignment with LDMS objectives.
- Integrating Kanban Boards and sustaining LDMS: Integrating Kanban boards into LDMS further enhances its capabilities by visualising workflows and facilitating adaptive, real-time decision-making. This step ensures that work processes are transparent and responsive, aligning with LDMS principles. Sustaining LDMS involves continuous improvement and refinement, ensuring the system evolves to meet changing needs.
Implementing these steps with precision and dedication lays the groundwork for a successful Lean Daily Management System (LDMS) that drives continuous improvement, enhances efficiency, and cultivates a culture of excellence within the organisation.
Benefits of LDMS Implementation
Implementing a Lean Daily Management System (LDMS) can have multiple benefits, including enhancing operational efficiency and productivity by fostering structured processes and accountability. LDMS promotes improved communication and collaboration, creating a platform for seamless information exchange. By embracing data-driven decision-making, LDMS empowers proactive problem-solving. Additionally, LDMS cultivates a culture of continuous improvement that drives lasting enhancements and positions the organisation for sustained success.
Overcoming Challenges and Pitfalls while implementing LDMS
Implementing a Lean Daily Management System (LDMS) may encounter obstacles, but comprehensive change management and tailored education initiatives can mitigate common challenges such as resistance to change or insufficient training. Proactive measures such as continuous reinforcement of LDMS principles, regular performance reviews, and fostering a culture that embraces adaptability and improvement can ensure sustainability and help organisations fully reap the benefits of an effective LDMS.
A Lean Daily Management System (LDMS) integrates Lean principles into daily operations, fostering transparent communication and collaboration. It identifies inefficiencies, addresses challenges, and capitalises on opportunities for excellence, accountability, and alignment, optimising operational efficiency and fueling growth and innovation.
Implementing a Lean Daily Management System (LDMS) is crucial for sustained growth and continuous improvement in your organisation. The LDMS framework equips you with powerful tools and practices that harmonise your operational landscape, cultivate a culture of accountability, and empower data-driven decision-making.
By embracing LDMS, you lay the foundation for a dynamic ecosystem where every aspect of your organisation becomes a canvas for improvement. From streamlining processes to fostering collaboration, LDMS provides a roadmap to unlock untapped potential and drive lasting change.
Take advantage of this chance to lead a change that boosts efficiency, productivity, and innovation. Taking the initial steps towards LDMS can position your organisation for continuous growth and improvement, redefining your industrial landscape.