What is the Kamishibai Audit System?
August 30, 2023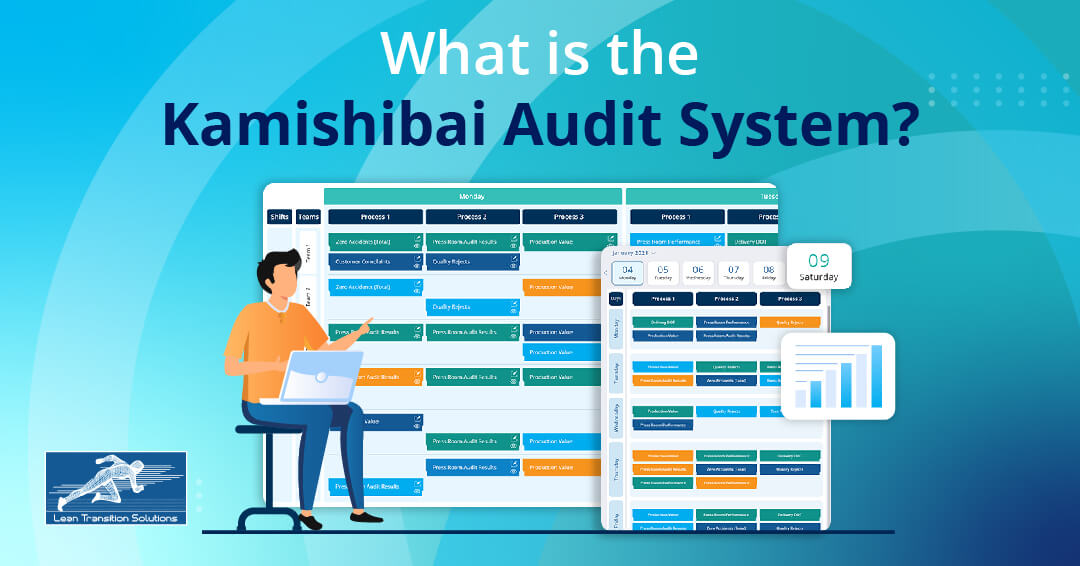
Process audits hold immense significance in organisations as they ensure operational excellence and maintain quality standards. These systematic evaluations within the shop floor processes help identify inefficiencies, bottlenecks, and opportunities for improvement. Process audits contribute to optimised workflows, reduced risks, and elevated product and service quality, ultimately driving the organisation towards sustained growth and success.
Kamishibai boards are an efficient tool for process confirmation and auditing within organisations. These visual management systems utilise cards to facilitate regular checks of processes, ensuring adherence to standards and identifying deviations. Kamishibai boards promote real-time visibility, accountability, and swift issue resolution, improving process accuracy, efficiency, and quality on the organisation's continuous improvement journey. Let's understand how the Kamishibai Audit System will benefit your organisation.
Understanding the Kamishibai Audit System
The Kamishibai Audit System is based on core principles that promote visual management and continuous improvement. This system ensures regular process audits that align with standard work procedures by utilising visual cues like Kamishibai cards. Its goals encompass enhancing process transparency, maintaining accountability, promptly addressing deviations, and cultivating a culture of continuous learning and refinement. Through these principles and objectives, the Kamishibai Audit System empowers organisations to optimise operations, streamline workflows, and achieve sustained excellence.
T cards and Kamishibai Boards
In the Kamishibai system, Tcards enable process confirmation and enhancement. These T shaped cards visually represent tasks, processes, or checkpoints that require regular audits. In the context of process confirmation, Tcards guide auditors through systematically reviewing each step, confirming adherence to standards, and identifying areas for enhancement. As part of the Kamishibai system, these cards are organised on a board, with auditors selecting and moving them through columns to track progress, document findings, and ensure ongoing process excellence. Tcards effectively combine visual management and accountability to foster a culture of continuous improvement in the organisation's operations.
Components of the Kamishibai Audit System
- Kamishibai Cards: Kamishibai cards are at the heart of this system, functioning as visual cues that guide process audits. These cards detail specific tasks, standards, and checkpoints, ensuring consistent procedure adherence. Through regular card rotations and audits, Kamishibai fosters accountability, encourages timely corrective actions, and enables the visual tracking of processes. This tangible tool actively engages teams in maintaining process excellence.
- Leader Standard Work: Leader Standard Work (LSW), an integral component, defines the responsibilities and routines of leaders within the Kamishibai system. By aligning their tasks with Kamishibai card rotations, leaders set an example, promote discipline, and ensure the entire team follows the audit process diligently. This synchronisation reinforces a culture of process ownership and continuous improvement.
- Gemba Walks: Gemba walks involve leaders and employees going to the "actual workplace" to observe and engage with ongoing processes. Integrated with Kamishibai, Gemba walks validate the accuracy of audits, provide insights for improvement, and encourage collaboration between leaders and team members. This hands-on approach nurtures a deeper understanding of processes and enhances problem-solving by addressing challenges at the source.
The Kamishibai Audit Process
The frequency of Kamishibai audits varies depending on the criticality of the audited process. Critical processes require daily audits, while less critical processes can be audited weekly or monthly. This systematic and visual approach ensures that operations are regularly reviewed, deviations are swiftly addressed, and a culture of continuous improvement is fostered within the organisation.
1. Planning and Preparation
- Determine the scope of the audit, including the processes or tasks to be audited.
- Create Kamishibai cards for each process/task, outlining standards and checkpoints.
- Set the frequency of audits based on the criticality of the process and the organisation's needs (e.g., daily, weekly, monthly).
2. Setting up the card
- Arrange the Kamishibai cards on the Kamishibai board.
- Ensure the cards are organised according to their audit frequency.
3. Executing the Audit Process
- An auditor (usually the responsible team member) selects the top red coloured card from (To Do) the Kamishibai board at the scheduled time.
- The auditor proceeds to the relevant area (Gemba) to perform the audit.
4. Standardising Process Checks
- The auditor checks the process against the standards outlined on the red coloured Kamishibai card.
- This involves confirming that tasks are performed correctly, equipment is in good condition, and safety protocols are followed.
5. Observing the Deviations
- While performing the audit, the auditor observes the process closely.
- Any deviations from the standards are noted on the card.
6. Immediate Actions
- If any issues or deviations are identified, the auditor takes immediate corrective actions if possible.
- These actions may include addressing minor defects, adjusting processes, or escalating significant issues to appropriate personnel.
7. Documenting the Audit findings
- The auditor documents the audit findings on the Kamishibai card, including any deviations and actions taken.
8. Finding resolutions and Initiating follow-ups
- If deviations are noted, responsible individuals are notified for resolution.
- The card may be moved to a designated column indicating that action is required.
9. Audit Status Update
- When the audit is completed, the green side of the card is placed back on the Kamishibai board indicating its process completion status.
- If the goal is not achieved, the card's red side is placed on the board to indicate the incomplete status due to deviation from the standard processes.
10. Continual Improvement
- Feedback from audits is used to drive continuous improvement efforts.
- Patterns of deviations and issues are analysed to identify root causes and implement preventative measures. Document the audit findings for future reference.
Benefits of Implementing the Kamishibai Audit System
- Visual Accountability and Transparency: Kamishibai's visual nature ensures that processes and audits are readily visible to all stakeholders. This transparency enhances accountability as teams can easily track progress, identify discrepancies, and address deviations from standards.
- Continuous Improvement Culture: Kamishibai fosters a culture of ongoing enhancement by making improvement efforts visible and actionable. Regular audits prompt discussions and adaptations, promoting a mindset of continuous learning and refinement.
- Timely identification and Resolution of issues: Through frequent audits, Kamishibai enables swift detection of process deviations and issues. This early identification leads to prompt corrective actions, minimising disruptions and preventing larger problems from arising.
- Employee Engagement and Empowerment: Kamishibai engages employees by involving them in the audit process. Employees can actively contribute insights, ideas, and solutions, fostering a sense of ownership and pride in their work.
- Data-Driven Decision-Making: Kamishibai generates valuable audit data that can be analysed to inform decision-making. This data-driven approach supports informed choices for process optimisation and strategic planning.
Process Confirmation Kamishibai Audit Checklist for Industries
Industries can use this Kamishibai audit checklist to ensure process adherence, maintain quality standards, and drive continuous improvement.
- Process Identification: Verify that the correct process or task is selected for the audit and that the Kamishibai card corresponds accurately.
- Standard Documentation: Ensure the process standards, procedures, and checkpoints outlined on the Kamishibai card match the official documentation.
- Audit Frequency: Confirm that the audit is being conducted at the appropriate frequency based on the criticality of the process.
- Audit Date: Check that the audit date aligns with the schedule and is within the designated frequency.
- Task Sequencing: Verify that tasks are executed in the correct sequence as defined by the standards.
- Adherence to Standards: Review each checkpoint on the Kamishibai card and assess whether the process adheres to the outlined standards.
- Visual Cues: Ensure that any visual cues or signals indicated on the Kamishibai card are present and accurate.
- Equipment Condition: Check the equipment, tools, and resources used. Ensure they meet the required standards.
- Safety Protocols: Verify that safety protocols, procedures, and protective measures are followed correctly.
- Material Usage: Evaluate the proper usage and handling of materials, ensuring they align with standards.
- Quality Assurance: Assess the quality of outputs or products generated by the process, confirming they meet the specified criteria.
- Action Plans: If deviations are identified, ensure that immediate corrective actions are taken as appropriate.
- Documentation: Document any audit findings, deviations, corrective actions, and additional notes accurately on the Kamishibai card.
- Follow-Up: Review any follow-up actions initiated based on previous audits and ensure their completion.
- Feedback Loop: Consider whether feedback from previous audits has been effectively communicated and integrated into the process.
Example of Kamishibai Audit Process
The Kamishibai audit process for the Vehicle Assembly Line Inspection involves a structured sequence of steps executed by the Assembly Line Supervisor. Firstly, the supervisor selects the designated "Vehicle Assembly Inspection" card from the Kamishibai board- Quality Inspection, initiating the audit procedure. This card serves as a guide and checklist for the subsequent stages.
The supervisor then starts the audit preparation phase by thoroughly reviewing the card, acquainting themselves with the precise inspection criteria and standards that pertain to the vehicle assembly process.
Afterwards, the supervisor transitions to the audit execution stage. This involves moving to the assembly line where the vehicles are being produced. Here, the supervisor systematically executes the inspection, meticulously examining each checkpoint as outlined on the Kamishibai card.
The focus is on verifying the accurate installation of components, proper alignment of parts, and precise torque settings. In the event of any deviations from the established standards, such as misaligned parts or absent components, the supervisor meticulously notes these on the card.
For any critical issues that arise during the audit, immediate actions are initiated by the supervisor. These actions could entail halting the assembly line, revisiting and validating the process, or involving specialised technicians. The audit findings, documented deviations, and subsequent actions are diligently recorded on the Kamishibai card.
Following this documentation phase, the supervisor oversees initiating corrective measures in response to identified deviations. These corrective actions might encompass process adjustments, component replacements, or notifications to maintenance teams.
Once the audit concludes, the "Vehicle Assembly Inspection" card is returned to the Kamishibai board with its green side (Done side) facing forward, indicating completion. This card movement visually signifies the successful execution of the audit. Subsequently, a continuous improvement approach is embraced, involving the analysis of audit findings and trends over time.
This analysis identifies recurring issues that prompt strategic process adjustments and targeted training initiatives to avert future deviations. Through this systematic Kamishibai audit process, the assembly line team ensures consistent quality, early issue detection, and an ongoing commitment to enhancement within the vehicle assembly process.
The application of Kamishibai methodology in daily vehicle assembly line inspections yields significant benefits. This approach ensures a consistent level of quality and facilitates early detection of assembly issues. Beyond its tangible impact, the Kamishibai system nurtures a culture of continuous improvement within the assembly line team. Its visual and structured approach empowers team members to take ownership of the process and actively contribute to the pursuit of operational excellence.
The Kamishibai board's transformative impact lies in its ability to revolutionise processes through visual management and accountability. By using Kamishibai cards to conduct audits, teams gain real-time insights into process adherence, identify areas for improvement, and swiftly address deviations. This fosters a culture of continuous improvement, empowers employees to take ownership of their work, and drives efficient, quality-focused operations. Ultimately, the Kamishibai board catalyses positive change, optimising workflows and propelling organisations towards sustained excellence.
Organisations can embrace and implement the Kamishibai Audit System as a pathway to improve their internal audit processes. Kamishibai boards enhance efficiency, improve quality, and cultivate a proactive problem-solving culture by integrating visual management, continuous improvement, and accountability. Embracing the Kamishibai system helps teams optimise processes and achieve excellence in their operations.