Strategies for Lead Time Reduction in Manufacturing Processes
June 26, 2023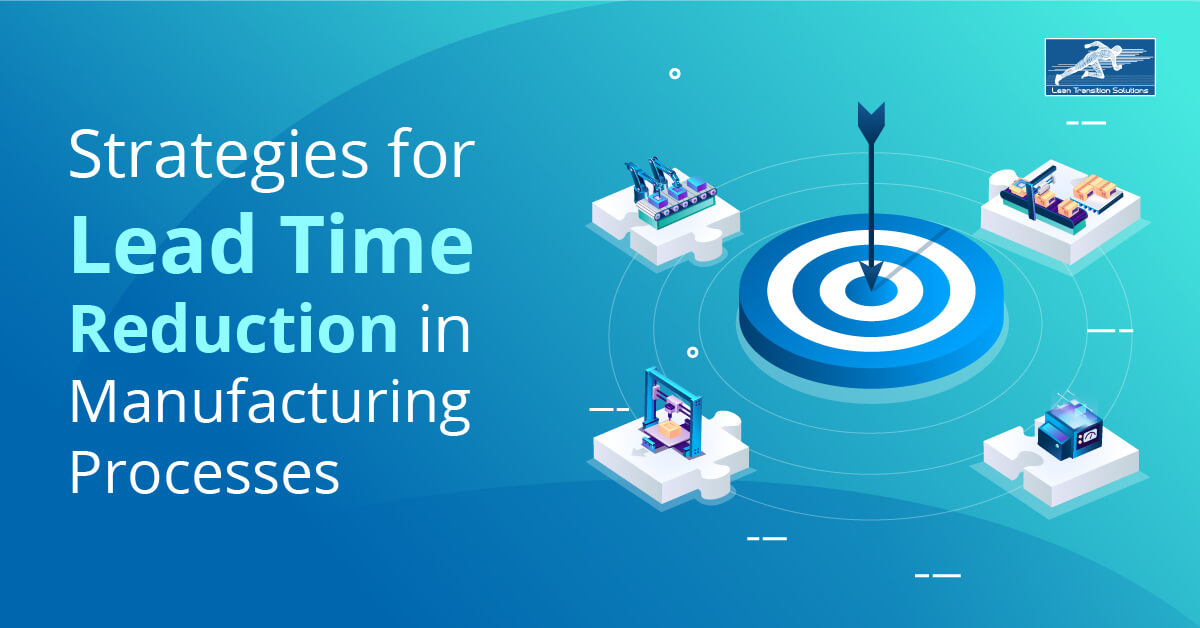
In an era of increasing customer demands and intense market competition, organisations constantly seek ways to improve manufacturing processes and deliver products faster than their competitors. As businesses strive to meet customer demands while maintaining profitability, reducing lead time has become a top priority. By reducing lead time in manufacturing processes, companies can enhance operational efficiency, meet customer expectations, and gain a competitive edge in the industry. In this blog, we will explore how to reduce lead time using effective strategies and drive business success.
What is Lead Time?
Lead time in manufacturing refers to the total duration it takes for a product to move through the entire manufacturing process, from the production phase to its completion and delivery to the customer. It involves stages like material sourcing, production, assembly, quality checks, and shipping. Lead time is a critical metric for manufacturers as it directly impacts customer satisfaction, production planning, and overall operational efficiency. By understanding and effectively managing lead time, organisations can streamline their processes, reduce delays, and meet customer demands more efficiently.
Types of Lead Time
Customer Lead Time: Customer lead time is the total duration from when an order is placed to when the customer receives the final product. It encompasses order processing, production, and delivery activities to meet customer expectations.
Material Lead Time: Material lead time refers to the time required to procure raw materials, components, or parts needed for production. It includes order placement, supplier processing, transportation, and inventory replenishment.
Production/Manufacturing Lead Time: Production or manufacturing lead time represents the time taken to manufacture a product from production phase to its completion. It includes activities such as processing, assembly, quality control, and packaging.
Cumulative Lead Time: Cumulative lead time is the sum total of material lead time and production lead time.
Delivery lead time: Delivery lead time refers to the time it takes for a product or service to be delivered to the customer's location. It is a key metric in logistics and supply chain management, influencing customer satisfaction and operational efficiency.
Components of Lead Time
Processing Time: It is the time required for manufacturing or processing the product. It includes material sourcing, fabrication, assembly, testing, and quality control.
Setup Time: The time needed to prepare the machinery, equipment, and tools for producing a specific batch or product. It includes machine setup, calibration, and configuration.
Queue Time: Queue time is the duration a product spends waiting in a queue or line before it can be processed. It occurs when other products or orders are ahead in the production line.
Waiting Time: Waiting time refers to when a product is waiting for the availability of resources, materials, or information necessary for its production. It can occur when there are delays in the supply chain, unavailability of raw materials, or waiting for feedback or approvals.
Transportation Time: If a product needs to be transported between different stages of the manufacturing process or between different facilities, transportation time becomes a lead time component. It includes the time spent in transit, loading and unloading and time associated with other logistics activities.
Inspection Time: The time required for inspecting and verifying the quality of the product during various stages of the manufacturing process is known as inspection time. Inspections may include visual checks, measurement tests, or performance evaluations.
Rework Time: Rework time is the time spent on reworking or repairing defective or non-compliant products. It occurs when issues are identified during inspection or quality control, requiring additional work to rectify the problems and bring the product up to the required standards.
Administrative Time: Administrative time encompasses the non-production tasks associated with processing orders, managing documentation, generating reports, coordinating with suppliers, and other administrative activities related to the manufacturing process.
These are some of the primary components that contribute to the overall lead time in manufacturing. Identifying and minimising delays in each component can help optimise the production process and reduce lead times, improving efficiency and customer satisfaction.
Lead Time Vs Cycle Time
Lead time and Cycle time are two important metrics in manufacturing. Lead time refers to the total duration from order initiation to delivery, including all the activities involved in the manufacturing process. On the other hand, Cycle time refers to the time required to complete one cycle of a specific task or operation within the manufacturing process. It represents the time taken to complete a single unit or batch of products.
Lead Time Vs Takt Time
The Lead time focuses on the end-to-end duration of the manufacturing process, while Takt time determines the required production rate to meet customer demand. Takt time sets the pace at which products or services should be produced to match customer requirements within a given timeframe. It helps optimise production flow, avoid overproduction, and achieve a balanced workload.
Differentiating Lead Time and Throughput Time
Lead time and Throughput time are two important concepts in operations and production management. Lead time refers to the total time a product or service takes to move through the entire process. On the other hand,Throughput time represents the actual time it takes to complete a specific activity or process. It focuses on the time spent actively working on a task or the time it takes to produce a unit.
Factors affecting Lead Time in Manufacturing
1. Supply Chain Management
Supplier performance: Delays or disruptions in the supply chain can extend lead time.
- Transportation and logistics: Inefficient transportation routes or delays in shipping can impact lead time.
2. Production Efficiency and Capacity
Equipment reliability: Breakdowns or maintenance issues can delay production and extend lead time.
Labour availability and skills: Insufficient skilled labour or staffing shortages can affect production capacity and lead time.
3. Inventory Management
Stock levels: Poor inventory management can result in stock-outs or excess inventory, impacting lead time. By analysing historical data and patterns of inventory usage, Digital T card systems can provide insights into demand forecasting. Teams can identify trends, seasonality, and variations in demand, enabling them to make informed decisions about inventory levels and optimise procurement or production processes accordingly.
- Just-in-Time (JIT) systems: Implementing JIT practices can reduce lead time by ensuring the availability of materials when needed.
4. Communication and Collaboration
Internal communication: Ineffective communication between departments can lead to delays and misalignment, prolonging lead time.
Supplier and customer collaboration: Lack of collaboration with suppliers or customers can result in miscommunication, affecting lead time.
5. External Factors
Supplier delays: Late deliveries or supplier quality issues can extend lead time.
- Market demand fluctuations: Rapid shifts in market demand can lead to challenges in meeting production requirements, affecting lead time.
Significance of Lead Time Reduction in Manufacturing processes
Shorter lead times enable businesses to respond swiftly to market changes and take advantage of opportunities. It reduces inventory holding costs as products spend less time in the production pipeline, resulting in improved cash flow and reduced working capital. Lead time optimisation also enhances operational efficiency by identifying bottlenecks, reducing idle time, and streamlining processes.
This ultimately leads to improved productivity, reduced waste, and lower production costs. Shorter lead times provide a competitive advantage by enabling faster time-to-market, facilitating quicker response to customer needs, and outperforming competitors. Optimising lead time in manufacturing processes leads to improved customer satisfaction, cost savings, operational efficiency, and a competitive edge in the market.
Benefits of Lead Time Reduction
Increased customer satisfaction: Reduced lead time allows for faster order fulfilment, leading to happier customers who receive their products or services promptly.
Improved competitiveness: Shorter lead times enable manufacturers to respond more quickly to market demands, giving them a competitive edge over rivals with longer lead times.
Enhanced cash flow: Reduced lead time means faster conversion of raw materials into finished goods, allowing manufacturers to generate revenue and cash flow more rapidly.
Lower inventory costs: With shorter lead times, manufacturers can maintain lower inventory levels by producing and delivering goods on a Just-in-Time (JIT) basis, minimising storage costs and the risk of obsolete inventory.
Improved quality control: Shorter lead times provide manufacturers with more frequent opportunities for quality checks and inspections, enabling them to identify and rectify issues promptly, resulting in higher product quality.
Faster time to market: By reducing lead times, manufacturers can accelerate their product development and launch cycles, allowing them to introduce new products or versions to the market more rapidly.
- Increased productivity: Streamlining processes to reduce lead times often involves identifying and eliminating non-value-added activities, increasing productivity and efficiency throughout manufacturing operations.
Key Strategies for Reducing Lead Time in Manufacturing processes
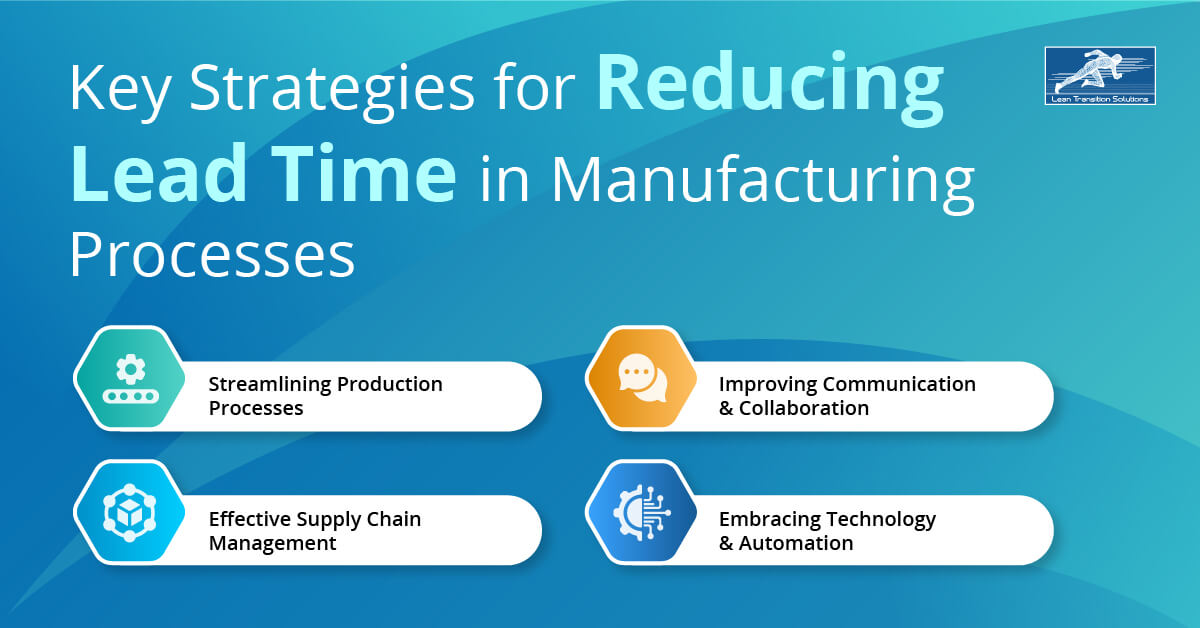
Are you wondering how to reduce lead time in your manufacturing processes? Here are some key strategies to help you achieve that goal!
1. Streamlining Production Processes
Optimising workflow and eliminating non-value-added activities: Identifying and eliminating unnecessary steps, bottlenecks, and inefficiencies in the production process can help streamline operations and reduce lead time.
Implementing lean principles in procurement and logistics: Lean principles, such as Just-in-Time (JIT) and Kanban systems, can be applied to improve the efficiency of procurement and logistics processes. By closely aligning the timing and quantity of material deliveries with production needs, manufacturers can minimise inventory holding time and reduce lead time.
Just-in-Time (JIT) aims to produce and deliver products or components precisely when needed, reducing inventory holding time. Kanban systems help maintain optimal inventory levels by signalling the need for replenishment based on actual usage. Digital T Cards are typically used in Lean Daily Management Systems, providing real-time visibility into each task's status and progress, allowing teams to identify bottlenecks and address them promptly. With a clear workflow overview, teams can identify areas where lead time can be minimised and make informed decisions to optimise processes.
- Minimising setup/changeover times: Streamline and optimise equipment setup and changeover procedures to reduce downtime between production runs, enabling faster processing and shorter lead times.
2. Effective Supply Chain Management
Collaborating closely with suppliers: Building strong relationships with suppliers and actively engaging in collaborative efforts can help optimise the supply chain, leading to shorter lead times.
Ensuring efficient logistics and transportation processes: Streamlining logistics and transportation operations, such as optimising routes, improving delivery schedules, and utilising efficient transportation modes, can help reduce lead time by ensuring the timely delivery of goods.
Implementing Vendor-Managed Inventory (VMI): VMI improves coordination between suppliers and customers. Suppliers can proactively plan production and shipments by having access to inventory data, aligning them with the customer's demand. This reduces the need for back-and-forth communication and speeds up the procurement process.
3. Improving Communication and Collaboration
Implementing effective Project management methodologies: Adopting project management methodologies such as Agile or Lean can improve communication, streamline processes, and ensure efficient coordination among teams, leading to reduced lead time.
Enhancing communication and coordination between departments: Facilitating regular and clear communication between different departments involved in the manufacturing process helps identify and resolve issues promptly, minimising delays, and ultimately reducing lead time.
Utilising Electronic Data Interchange (EDI) for seamless communication: Implementing EDI systems allows for automated and standardised exchange of information between suppliers, manufacturers, and customers, enabling faster and more accurate communication, order processing, and coordination.
- Enhancing cross-functional communication and coordination: Promoting effective communication and collaboration across different departments within the organisation, such as production, procurement, and logistics, helps in aligning goals, sharing information, and coordinating activities, resulting in shorter lead times.
4. Embracing Technology and Automation
Automation, machine learning, and advanced analytics for process optimisation:
- Implementing automation technologies such as robotics and AI-driven systems can streamline manufacturing processes, reduce human error, and increase production efficiency, ultimately leading to lead time reduction.
- Leveraging machine learning algorithms and advanced analytics can help identify bottlenecks, optimise scheduling, and improve overall process performance, reducing lead time. Digital T cards provide valuable insights into task durations, completion rates, and cycle times. By analysing this data, teams can identify areas of inefficiency, process bottlenecks, or tasks that consistently take longer than expected.
- Implementing automation technologies such as robotics and AI-driven systems can streamline manufacturing processes, reduce human error, and increase production efficiency, ultimately leading to lead time reduction.
Adopting Technological solutions like Enterprise Resource Planning (ERP) and Manufacturing Execution Systems (MES)
- Implementing robust ERP systems enables better coordination and management of resources, including materials, equipment, and labour, resulting in improved production planning and reduced lead time.
- Utilising MES software allows real-time monitoring of production processes, facilitates data-driven decision-making, and enhances communication and collaboration among different manufacturing functions, all of which contribute to lead time reduction.
- Implementing robust ERP systems enables better coordination and management of resources, including materials, equipment, and labour, resulting in improved production planning and reduced lead time.
Reducing lead time in manufacturing processes requires a holistic approach encompassing process improvement, demand forecasting, lean principles, automation, and collaboration. Conducting a thorough process analysis is essential to identify bottlenecks and areas of inefficiency. By understanding the root causes of delays, organisations can implement targeted solutions for improvement. Embracing lean principles, such as Just-in-Time production, Kanban systems, continuous improvement, and waste reduction, can reduce lead time, improve operational efficiency, and ultimately enhance competitiveness in the market.