How can Kanban reduce your Environmental Impact?
April 30, 2024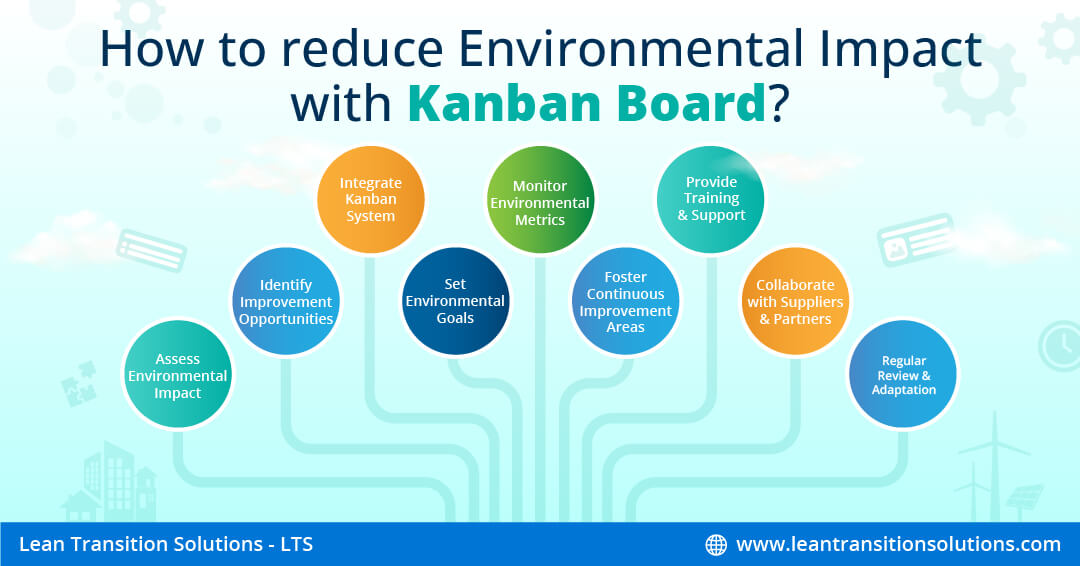
The Special Report on Global Warming of 1.5 °C assesses the impacts of greenhouse gas emission pathways and strategies to combat climate change in the context of sustainable development. As manufacturers are significant contributors to greenhouse gases, pollution, and waste that cause environmental impact, ongoing efforts must be made to combat climate change and transition towards more sustainable industrial practices.
In response to these sustainable efforts, businesses increasingly turn to methodologies such as Kanban, a cornerstone of lean management that prioritises process efficiency and waste reduction. Kanban principles can help companies optimise their resource utilisation, streamline workflows, and contribute to environmental sustainability when integrated into various operations.
Moreover, with the growing emphasis on achieving net zero emissions, the need for sustainable business practices has never been more pressing. Let's discuss the role of Kanban methodology in driving sustainable initiatives and explore how increased green awareness is changing modern business practices towards a more environmentally responsible future.
Environmental Impact of Traditional Workflows
Conventional workflows often result in inefficiencies and significant environmental impact, hindering progress towards achieving environmental goals and causing sustainability challenges. From excessive resource consumption to carbon emissions, these practices pose substantial environmental risks and hinder the efforts to achieve carbon neutrality, waste reduction or other sustainability objectives.
However, with the advent of digital tools and technologies, companies are increasingly adopting innovative solutions to mitigate their environmental footprint and advance sustainability in business. Tools like the Kanban Software offer efficient ways to streamline workflows, optimise resource utilisation, and support Sustainable Development Goals (SDGs). Using digital tools, companies can align their operations with sustainability goals, paving the way for a more environmentally conscious and sustainable future.
In what ways can Kanban reduce the environmental impacts?
Going Green with Kanban Boards offers a pathway to reducing environmental impact and advancing sustainability goals within your organisation. Let's explore how Kanban boards can contribute towards reducing the environmental impact and facilitating sustainability initiatives.
Reducing Overproduction: Implementing pull-based Kanban systems helps to minimise overproduction by producing goods only as needed, thus reducing waste and optimising resource utilisation.
Managing Excess Inventory Usage: Kanban boards strategically manage excess inventory to prevent waste and reduce storage costs, ensuring efficient use of resources.
Minimising Transportation: The Kanban system helps to develop efficient transportation strategies that minimise fuel consumption, reduce carbon emissions, and lower environmental impact by tracking the status of real-time operational processes.
Reducing Energy Consumption: Implementing a Kanban system promotes energy-efficient practices to decrease energy consumption and lower carbon footprint.
Streamlining Resource Usage: Optimising resource usage using Kanban systems can streamline processes to reduce waste and enhance efficiency, aligning with sustainable practices.
Improving Resource Allocation: Pull-based Kanban systems are utilised to optimise resource allocation, ensuring resources are allocated efficiently based on demand, thus minimising waste and enhancing productivity.
Minimising waste: Kanban boards help to reduce waste, promote sustainability, and optimise resource utilisation.
Limiting Work in Progress (WIP): Kanban helps set limits on WIP to prevent bottlenecks, improve workflow efficiency, and prioritise high-value tasks.
- Focusing on Continuous Improvement and sustainability: Kanban boards cultivate a culture of constant improvement and sustainability to drive ongoing process improvement, minimise environmental impact, and promote long-term success.
How to reduce environmental impact with Kanban Board?
Assess Environmental Impact: Begin by assessing current environmental impact areas within your operations, identifying factors contributing to waste, energy consumption, and carbon emissions.
Identify Improvement Opportunities: Identify specific areas where implementing Kanban can lead to environmental improvements, such as reducing overproduction, minimising waste, and optimising resource utilisation.
Integrate Kanban System: Incorporate Kanban principles into your operations to streamline processes, minimise waste, and enhance efficiency. Utilise Kanban boards and cards to visualise workflows and optimise resource allocation.
Set Environmental Goals: Establish clear environmental goals and targets aligned with your Kanban implementation, focusing on reducing carbon footprint, minimising waste generation, and promoting sustainability.
Monitor Environmental Metrics: Monitor and track environmental metrics such as Carbon Emissions, Energy Conservation, Environmental Compliance and Resource Conservation. Utilise Kanban information to measure progress, identify improvement areas, and make informed decisions.
Foster Continuous Improvement areas: Promote a culture of continuous improvement by encouraging employee involvement, inviting feedback, and implementing iterative changes to minimise environmental impact further.
Provide Training and Support: Provide employees with training and education on environmental sustainability practices and the role of Kanban in reducing environmental impact. Ensure everyone understands their responsibilities in achieving environmental goals.
Collaborate with Suppliers and Partners: Collaborate with suppliers and partners to extend environmental initiatives throughout the supply chain. Encourage sustainable practices and promote environmental stewardship among stakeholders.
Regular Review and Adaptation: Adapt your Kanban system and environmental initiatives based on changing requirements, feedback, and outcomes. Continuously strive for improvement and innovation in reducing environmental impact.
Monitoring Kanban Metrics to track Environmental Impact
Monitoring Kanban metrics such as Lead time, Cycle time, Work-in-Progress, and Throughput is essential for conducting Ecological Impact Assessment (EIA) within business operations. By analysing Kanban metrics, businesses can gain insights into process efficiency, resource utilisation, and waste reduction initiatives. Let’s understand the insights you can get from analysing each Kanban metrics:
The lead time metrics in Kanban facilitate sustainable practices by minimising waiting times and accelerating the delivery of products or services.
Cycle time is a Kanban metric, and improved cycle time signifies sustainability efforts by ensuring efficient workflow management, promoting a streamlined production process.
Work-in-Progress metrics enable organisations to minimise overproduction and optimise resource allocation.
Throughput metrics gauge overall productivity and environmental efficiency.
Kanban metrics empower businesses to make data-driven decisions, prioritise environmental initiatives, and drive sustainable practices for long-term environmental stewardship. The Green KPIs or Environmental KPIs such as Energy usage, Material usage, and Waste reduction, showed a positive impact, when Kanban and its related practices are applied in various operational processes.
Ensuring Sustainability with Kanban Board : Example
As part of the strategic initiatives to achieve sustainability goals, a manufacturing organisation recognised the need to reduce paper waste generation throughout their workflow stages. The use of paper-based documents hindered operational efficiency, causing a considerable negative impact on the environment. Therefore, the organisation is committed to minimising paper waste generation as a proactive step towards achieving its Sustainable Development Goals (SDGs) and fostering environmentally responsible practices across its operations.
Struggling with Challenges without an effective Solution!
Without a software solution, the manufacturing organisation faced several operational inefficiencies and productivity issues due to their reliance on paper-based systems. The specific challenges faced by such this manufacturing organisation include:
Inaccuracies in Data Entry: Without digitised solutions, manual data entry results in human error, leading to inaccuracies in record-keeping.
Time-consuming Paperwork: The manual paperwork handling consumes valuable time and resources, slowing down operational processes and hindering productivity.
Dependency on Manual Processes: Relying on manual processes increases the likelihood of inefficiencies, as tasks that could be automated require human intervention, leading to delays and errors.
Communication issues between Shifts: In a paper-based system, communication between shifts may be disjointed and prone to misunderstandings, impacting coordination and collaboration.
Data Presentation and Formatting Challenges: Presenting and formatting data in a paper-based system can be cumbersome and time-consuming, hindering the analysis and interpretation of critical information.
Implementing Kanban System for Overcoming Challenges
The implementation of a digital Kanban system proved instrumental in overcoming the challenges in paper-based workflows within the manufacturing industry. The digital Kanban system streamlined workflows, and the manufacturing operations experienced a powerful transformation, enabling them to embrace a productive environment and sustainability in their business landscape.
Counting Benefits after Kanban Implementation!
Enhanced visual clarity in workflow enables quick identification of task statuses and bottlenecks, enhancing overall operational transparency to prevent delays and optimise production schedules.
Improved communication and coordination among team members foster a collaborative work environment, leading to smoother workflows and higher productivity.
Minimised errors and delays result in improved product quality and customer satisfaction, reducing the need for rework and enhancing brand reputation.
Electronic task management eliminates the risk of lost or misplaced documents, ensuring critical information is always accessible and up-to-date.
Saved time and resources previously spent on printing and distributing paper documents translate into cost savings and increased operational efficiency.
Significantly reduced paper waste generation demonstrates a commitment to environmental sustainability and compliance with eco-friendly practices.
Real-time updates and adjustments enabled quick responses to changing market demands, ensuring optimal resource allocation and production efficiency.
Seamless adaptation to changing priorities allows manufacturing processes to remain flexible and responsive, maximising operational agility and competitiveness.
Thus, by adopting a Kanban tool, the manufacturing industry has effectively addressed the negatives of using a paper-based system, promoted environmental sustainability by reducing paper waste generation and avoided delays in deriving actionable insights.
Tips for incorporating Sustainability Goals with Kanban Practices
Visualise the workflow to identify environmental impact areas and optimise resource usage.
Limit Work In Progress (WIP) to minimise overproduction and reduce waste generation, aligning with sustainability goals.
Manage flow efficiently to streamline processes and minimise energy consumption and carbon emissions.
Make process policies explicit to ensure adherence to environmental regulations and promote sustainable practices.
Implement feedback loops to monitor environmental metrics and identify areas for improvement continuously.
Improve collaboratively by engaging team members in sustainability initiatives and fostering a culture of environmental stewardship.
Embracing Kanban methodologies presents a promising pathway for businesses to mitigate their environmental footprint and cultivate sustainable practices. Organisations can effectively reduce energy consumption, carbon emissions, and resource depletion by optimising workflows, minimising waste, and fostering continuous improvement.
The visual nature of Kanban boards facilitates the identification of environmental impact areas while limiting Work In Progress (WIP) and implementing feedback loops to ensure ongoing progress towards sustainability goals. With Kanban tool, businesses can enhance operational efficiency and contribute positively to environmental preservation, paving the way for a green manufacturing and more sustainable future.