Why TCards are the perfect partner for your Standard Operating Procedures (SOP) ?
March 17, 2025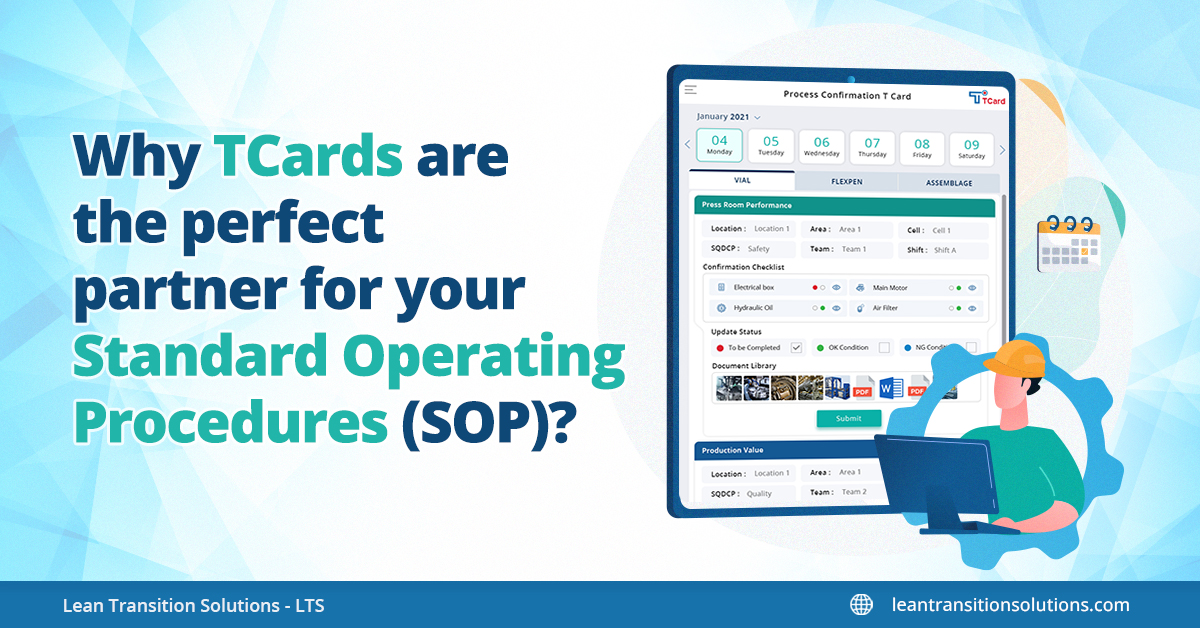
There are many ways to do a task, but there is one proven, efficient way to achieve the best outcomes. We call it the process we can rely on, repeat, and standardise across the board. But getting there isn't always straightforward. After several quality audits, daily workflow management, and optimisation, we eventually pinpoint the right set of operations and procedures that best align with your operational excellence and strategic goals. It’s clear that every operations manager or shift operator can benefit from a digital process confirmation tool like TCards to identify, creating, and define standard operating procedures. Keep reading to discover why TCards are the perfect partner for your SOPs.
What is a standard operating procedure? Why is it necessary?
A Standard Operating Procedure (SOP) is a detailed, written document that outlines the specific steps and processes required to perform a task or operation consistently and efficiently. On a shop floor, SOPs are vital to ensure uniformity in production, maintain quality standards, enhance safety, and reduce errors by providing clear instructions for workers. They also serve as a training tool for new employees, aid in regulatory compliance, and improve overall operational efficiency, enabling smooth day-to-day operations. Ever heard of leader standard work? Find the most unexpected ways to sustain the continuous improvement measures with us! Read along to know why TCards are essential for SOP creation and implementation.
Decode the unusual productivity hack – uniformity with TCards!
We believe uniformity should go beyond just uniforms and safety measures. It should also extend to "how the machines are operated," "troubleshooting procedures," "how to prioritise and allocate resources for critical tasks," or "how to handle emergencies like engine breakdowns." This is when the need for a "standard operating procedure" becomes crystal clear. In the age of Industry 4.0, the best way to achieve this is through digital process confirmation combined with workflow automation. We've put together a perfect guide to help you define your SOP effectively and seamlessly with our digital solutions. Using TCards to standardise and automate SOP creation is just a quick read away!
Comprehensive guide to creating a Standard Operating Procedure (SOP) with TCards
A Standard Operating Procedure (SOP) ensures consistent execution of tasks by providing clear instructions. Using our TCards software, a visual and systematic approach, simplifies SOP creation, execution, and tracking. Gain a better understanding of how TCards provide workflow visualisation for SOP implementation. How TCards improve task tracking and accountability in SOPs is literally visible over a single dashboard, (yeah, we have done some lean work back there...) Below is a quick list of how TCards improve task tracking and accountability in SOPs:
1. Define the purpose and scope of the SOP
2. Analyse the task in detail
3. Structure TCard categories
4. Create TCards for each step
5. Organise TCards on a board
6. Test the SOP with TCards
7. Train Employees
8. Monitor SOP execution
9. Update the SOP
10. Document and centralise access
11. Conduct regular reviews
1. Define the purpose and scope of the SOP
- Purpose: Identify why the SOP is needed. Is it to enhance safety, maintain quality, improve efficiency, or standardise processes? This purpose sets the tone for your SOP.
- Scope: Clearly define the boundaries of the SOP. Specify the tasks it covers, the personnel involved, and the expected outcomes.
2. Analyse the task in detail
-
Break the process into individual steps:
- Observe how the task is performed by employees.
- Identify key actions, decision points, and potential challenges.
-
Involve workers and supervisors who perform or oversee the task to ensure the process is accurately documented.
3. Structure TCard categories
- Decide on the specific data fields for each TCard.
Examples :- Step Title: Short description of the action (e.g., "Start Machine").
- Details:: A detailed explanation of the step, including "how" and "why."
- Tools/Resources:: Equipment or materials required (e.g., "Calibration tool").
- Assigned Personnel:: Who performs this step?
- Completion Status:: Use colour-coded markers or labels for "Pending," "In Progress," or "Completed."
- Time Estimation:: Approximate duration to complete the step.
4. Create TCards for each step
- Use a single TCard for every action or task within the process.
- Provide clear and concise instructions. Avoid jargon unless necessary, and include any safety precautions or compliance notes.
- Step Title: Start Machine
- Details : "Turn the main power switch to 'ON,' then press the green start button. Wait for the indicator light to stabilise before proceeding."
- Tools/Resources : None
- Assigned Personnel : Operator
- Time Estimation : 2 minutes
5. Organise TCards on a board
- Use a physical TCard board or a digital TCard system for organisation.
Arrange the TCards in sequential order:- Group steps into phases (e.g., preparation, execution, quality check).
- Use columns or swim lanes for different categories like "Pending," "In Progress," and "Completed."
6. Test the SOP with TCards
- Conduct a trial run using the TCards with employees:
- Check if instructions are clear and easy to follow.
- Identify bottlenecks or unclear steps.
- Collect feedback on potential improvements.
7. Train Employees
- Train all relevant personnel on using the SOP and the TCard system. Provide hands-on practice to ensure they understand:
- How to read and execute tasks using TCards.
- How to update the status of each TCard as they progress.
8. Monitor SOP execution
- Regularly observe how the SOP is used in real-time:
- Check if tasks are being executed in sequence.
- Ensure TCards reflect the current status of work.
- Identify recurring issues or deviations from the process.
9. Update the SOP
- SOPs should evolve with process changes or new insights:
- Update TCards to reflect any procedural modifications.
- Add new TCards if new steps are introduced.
- Remove obsolete TCards or combine redundant ones.
10. Document and centralise access
- Maintain a central repository for SOPs:
- For physical TCards, keep a master copy of the SOP in a binder or file.
- For digital systems, ensure the SOP is accessible via a shared drive or software platform.
11. Conduct regular reviews
- Periodically review the SOP to ensure its relevance and effectiveness:
- Schedule team meetings to discuss challenges or improvements.
- Use data from the TCard system to identify inefficiencies.
Example use case: Cleaning and maintenance SOP for a shop floor
How TCards help in creating standard operating procedures (SOP) seems clear now. But we would love to help you with a quick example from the shop floor.
- Define Purpose: To ensure all equipment is cleaned daily to prevent contamination and maintain efficiency.
- TCard Steps :
- TCard 1 : Prepare Cleaning Materials : "Gather all cleaning tools and solutions."
- TCard 2 : Turn Off Equipment : "Switch off all machines and unplug them."
- TCard 3 : Clean Equipment : "Wipe surfaces with a cleaning solution and cloth."
- TCard 4 : Inspect Equipment : "Check for damage or wear during cleaning."
- Board Layout :
- Columns: "Pending," "In Progress," "Completed"
- Arrange TCards in sequential order.
How TCards support SOP creation in shop floor workflow automation ?
Wondering how TCards streamline SOP workflows on the shop floor? We have compiled quick facts on how to use TCards for efficient SOP tracking and execution. How TCards streamline SOP workflows on the shop floor?
TCard Features Table
Identify and evaluate how TCards enhance task execution in Standard Operating Procedures with us. Using TCards to standardise and automate SOP creation is seamless, sustainable, and scalable.
Workflow Stage | How TCards Support? | Benefits of using TCards for SOP management | Example |
---|---|---|---|
Data Capture | - TCards record step-by-step instructions, responsible personnel, and required tools. | - Ensures accurate and consistent data collection. - Reduces human error. |
A TCard for "Machine Calibration" includes fields to record time, operator name, and equipment status. |
Task Assignment | - Assign tasks to specific personnel or teams using TCards. | - Enhances accountability. - Streamlines task allocation. |
A "Maintenance Checklist" TCard is assigned to a technician and marked "Pending" until the task is initiated. |
Workflow Visualisation | - Organise TCards on a board to display task progression (e.g., Pending, In Progress, Completed). | - Provides real-time visibility. - Simplifies tracking for supervisors and workers. |
A TCard board shows the cleaning tasks at different stages, allowing supervisors to monitor progress at a glance. |
Real-Time Updates | - Update the status of TCards as tasks are completed. | - Enables dynamic tracking. - Keeps all stakeholders informed. |
A TCard moves from "Pending" to "In Progress" when an operator starts a task and to "Completed" upon verification. |
Error Detection | - Use TCards to document deviations or issues encountered during task execution. | - Improves process reliability. - Facilitates quick troubleshooting. |
A TCard for a machine start-up process includes a section to report errors like "Low Pressure Warning" or "Sensor Failure." |
Standardisation | - Use TCards to define and enforce uniform procedures for repetitive tasks. | - Ensures consistency. - Maintains quality standards. |
A "Daily Equipment Cleaning" TCard includes exact instructions and materials required for cleaning, ensuring all operators follow the same process. |
Data Logging | -Automatically or manually record task completion times, outcomes, and operator feedback on TCards. | - Supports compliance. - Creates an audit trail. |
TCards for a welding process capture timestamps and output quality, helping meet safety and quality compliance requirements. |
Reporting | - Aggregate data from TCards for analysis and reporting. | - Simplifies performance tracking. - Provides actionable insights. |
Weekly reports generated from TCard data highlight completed tasks, time taken, and unresolved issues, helping supervisors identify bottlenecks. |
Decision-Making | - Use insights from TCards to identify workflow inefficiencies or training needs. | - Improves operational efficiency. - Informs strategic adjustments. |
Analysis of TCard data reveals repeated delays in a specific task, prompting management to invest in faster tools or operator training. |
Continuous Improvement | - Update TCards based on feedback and performance data to refine the SOP. | - Enhances adaptability. - Promotes a culture of continuous improvement. |
Feedback from operators leads to revisions in a "Material Handling" TCard, adding clearer instructions for heavy lifting equipment usage. |
Identify and evaluate how TCards enhance task execution in Standard Operating Procedures with us. Using TCards to standardise and automate SOP creation is seamless, sustainable, and scalable.
Key features of TCards in SOP automation:
- Modular and scalable : TCards can be adapted to processes of any complexity.
- User-Friendly interface : Physical or digital TCards simplify access and use for all team members.
- Integration capability : Digital TCards integrate with reporting and analytics systems for seamless workflow optimisation.
Challenges in defining a SOP on a shop floor and how TCards help solve them
The role of TCards in SOP standardisation and consistency is non-negotiable. Digital process confirmation with TCards for SOP compliance has its own share of challenges. See for yourself Why TCards simplify procedure management for SOPs.
- Inconsistent task execution
- Challenge : Variations in task execution by different workers lead to inefficiency and quality issues.
- Solution: : TCards provide step-by-step instructions, ensuring standardised and consistent processes across the workforce.
- Communication gaps
- Challenge : Miscommunication between departments or teams causes delays and operational errors.
- Solution: : TCard boards visually display task status, bridging communication gaps by offering real-time updates accessible to all teams.
- Complex processes
- Challenge : Multi-step or dependent tasks are challenging to document and manage.
- Solution: : TCards break down complex workflows into manageable, clearly defined steps, simplifying task execution and management.
- Resistance to change
- Challenge : Employees resist adopting new procedures, especially when unclear or overwhelming.
- Solution: : The intuitive and visual nature of TCards makes new processes easy to understand, encouraging faster adoption and reducing resistance.
- Lack of real-time tracking
- Challenge : Supervisors face difficulty in monitoring the status of ongoing tasks, leading to inefficiencies.
- Solution: : TCards track progress dynamically, moving through stages like "Pending," "In Progress," and "Completed," allowing real-time visibility of task statuses.
- Difficulty in identifying errors
- Challenge : Errors go unnoticed without a structured tracking mechanism, delaying resolutions.
- Solution: : TCards include fields to report issues during execution, enabling quick detection and corrective action.
- Data overload or loss
- Challenge : Important data can be overlooked or lost in traditional paper-based or unorganised documentation.
- Solution: : Digital TCards securely store and organise data, while physical TCards provide a tangible, accessible record for reference.
- Inadequate training
- Challenge : New employees struggle to grasp tasks due to insufficient or unclear instructions in the SOP.
- Solution: : TCards act as practical guides, offering detailed instructions that help new employees quickly understand and perform tasks.
- Inefficient updates
- Challenge : SOP updates are cumbersome and slow when processes change frequently.
- Solution: : TCards are easy to modify, allowing SOP updates to be implemented seamlessly without disrupting ongoing workflows.
- Limited accountability
- Challenge : Undefined responsibilities in the SOP make it hard to track who is responsible for specific tasks.
- Solution: : TCards assign tasks to specific individuals or teams, ensuring clear accountability for each step of the workflow.
Streamline, standardise and succeed with Digital TCards
Tired of the chaos and inefficiencies in your shop floor workflows? TCards make defining and implementing Standard Operating Procedures simple, effective, and scalable. With features like real-time task updates, accountability tracking, and easy customisation, TCards empower your team to achieve operational excellence effortlessly. Contact us today to learn more or sign up for a free trial to see the difference TCards can make for your business. Your streamlined operations are just a click away!
FAQs
1. What are TCards, and how do they work with SOPs?
TCards are visual management tools that help organise and track workflows. They ensure SOP steps are followed systematically by providing clear task visibility.
2. Can TCards improve team collaboration on SOPs?
Yes, TCards enhance collaboration by enabling teams to monitor progress in real-time, ensuring everyone stays aligned with the SOPs.
3. Are TCards suitable for industries with complex SOPs?
Absolutely! TCards are highly adaptable, making them ideal for industries like manufacturing, healthcare, or logistics where SOP compliance is crucial.
4. How do TCards help maintain compliance with SOPs?
TCards create a structured process flow, making it easier to document and monitor compliance, reducing the risk of errors or missed steps.
5. Are TCards easy to integrate into existing processes?
Yes, TCards are simple to implement and can seamlessly integrate into your existing workflows, whether digital or manual.
TCards are visual management tools that help organise and track workflows. They ensure SOP steps are followed systematically by providing clear task visibility.
2. Can TCards improve team collaboration on SOPs?
Yes, TCards enhance collaboration by enabling teams to monitor progress in real-time, ensuring everyone stays aligned with the SOPs.
3. Are TCards suitable for industries with complex SOPs?
Absolutely! TCards are highly adaptable, making them ideal for industries like manufacturing, healthcare, or logistics where SOP compliance is crucial.
4. How do TCards help maintain compliance with SOPs?
TCards create a structured process flow, making it easier to document and monitor compliance, reducing the risk of errors or missed steps.
5. Are TCards easy to integrate into existing processes?
Yes, TCards are simple to implement and can seamlessly integrate into your existing workflows, whether digital or manual.