Improving Quality Inspection Results through Layered Process Audits
February 24, 2025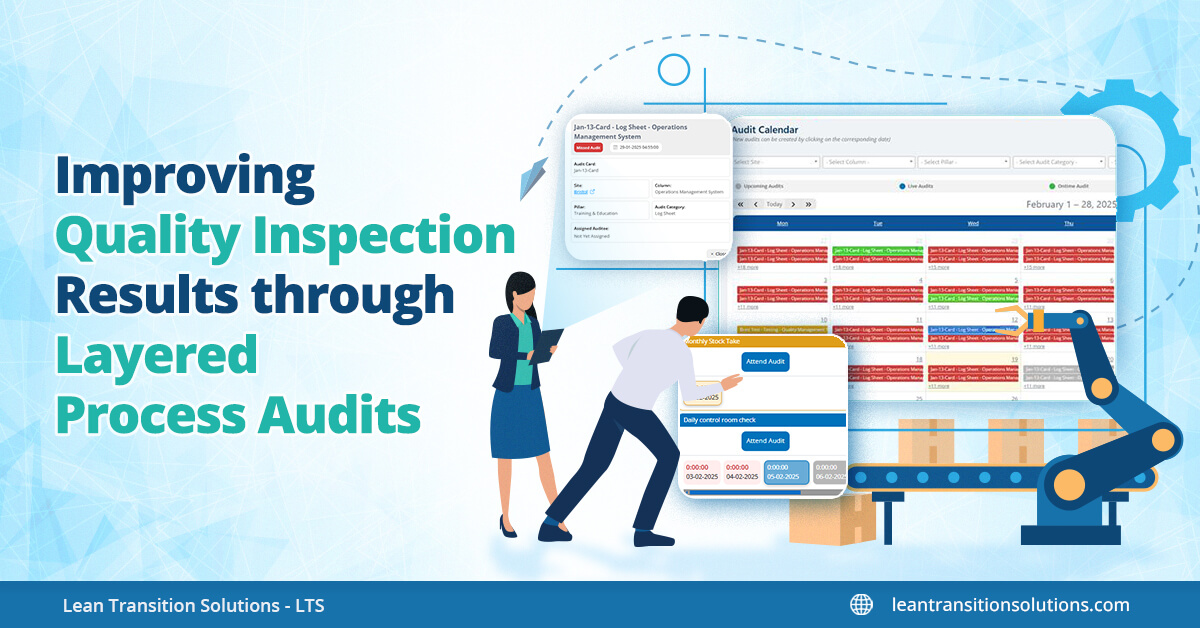
That last twirl of the ladle in the soup and the final check of the spice trail and peppery goodness is not the only quality check that ever gets plated! Quality inspection is the bread and butter of every product and service distributor, bringing out the “true essence” of your deliverables. Just like the layering of flavours and textures is the secret to a great soup, the final aroma and taste depend on the herbs, sauce, vegetables, pasta, beans, and fresh spinach, and how well they are boiled and cooked together at each layer.
Similarly, every technical ingredient and process recipe must be effective, efficient, and aligned with the organisation's strategic goals and values at every layer. Is this as visible as “sputtering mustard”? Hopefully so! But as we know, every process is like an onion, with many layers, and the deeper you go, the more intricate it becomes. Want to know how to improve quality inspection results through layered process audits? If achieving process consistency and discipline through layered process audits is in your thoughts, read along!
Similarly, every technical ingredient and process recipe must be effective, efficient, and aligned with the organisation's strategic goals and values at every layer. Is this as visible as “sputtering mustard”? Hopefully so! But as we know, every process is like an onion, with many layers, and the deeper you go, the more intricate it becomes. Want to know how to improve quality inspection results through layered process audits? If achieving process consistency and discipline through layered process audits is in your thoughts, read along!
What are Quality Inspection Results?
Before marching ahead into a full-swing quality inspection ritual, we all need an audit checklist to check the critical components and assess how well they contribute to the overall quality of the product. A routine Gemba walk or a detailed fishbone diagram (painstakingly created if done manually) can help derive valuable quality inspection results.
Quality inspection results are the documented outcomes of examining products, processes, or services to ensure they meet specified standards or requirements. These results typically include details about compliance with quality criteria, any defects or non-conformities found, and recommendations for corrective actions if necessary. They serve as a critical tool for maintaining quality assurance, tracking performance trends, and making data-driven decisions to enhance production efficiency and customer satisfaction.
Once you arrive at the quality inspection results, how effectively will you put the suggestions and deductions into an actionable plan at every process layer? Will a quick meeting suffice? (We know the backstory, don’t we?). Determined to bridge the gap between productivity and inefficiency (remember, we are the lean experts!), we went the extra mile and created a digital process confirmation tool, complete with digital audit checklists, quality inspection results, audit schedules and prioritisation, process confirmation reports, and much more. How layered process audits ensure compliance at multiple organisational levels is just a quick read away. Want to know how our TCards for process confirmation help improve quality inspection results through layered process audits?
Quality inspection results are the documented outcomes of examining products, processes, or services to ensure they meet specified standards or requirements. These results typically include details about compliance with quality criteria, any defects or non-conformities found, and recommendations for corrective actions if necessary. They serve as a critical tool for maintaining quality assurance, tracking performance trends, and making data-driven decisions to enhance production efficiency and customer satisfaction.
Once you arrive at the quality inspection results, how effectively will you put the suggestions and deductions into an actionable plan at every process layer? Will a quick meeting suffice? (We know the backstory, don’t we?). Determined to bridge the gap between productivity and inefficiency (remember, we are the lean experts!), we went the extra mile and created a digital process confirmation tool, complete with digital audit checklists, quality inspection results, audit schedules and prioritisation, process confirmation reports, and much more. How layered process audits ensure compliance at multiple organisational levels is just a quick read away. Want to know how our TCards for process confirmation help improve quality inspection results through layered process audits?
Why Should You Choose Layered Process Audits for Better Process Confirmation Results?
Are you at a crossroads, deciding between the traditional process audit you’ve been following and “layered process audits”? The role of layered process audits in quality management systems is remarkably high. Wondering which technique yields better results? Here’s why you should choose layered process audits for your organisation:
TCard Features Table
This distinction ensures that process audits focus on a deep dive into individual processes, while layered process audits sustain overall process consistency and organisational commitment to quality. Manually executing layered process audits can leave you in a pickle, with half-said project logs and forgotten details compounding the issues. Digital process confirmation tools for layered process audits can significantly improve quality inspection results. Start using layered process audits to drive continuous improvement in manufacturing.
Aspect | Process Audit | Layered Process Audit (LPA) |
---|---|---|
Objective | Evaluates a single process to ensure compliance with standards. | Verifies adherence to standards at multiple organisational levels. |
Focus Area | Specific areas of the process being audited. | Repeated checks across various layers for consistency. |
Frequency | Conducted periodically (e.g., monthly, quarterly). | Conducted more frequently (e.g., daily, weekly). |
Participants | Performed by quality or technical experts. | Performed by personnel from different organisational levels (e.g., supervisors, managers, operators). |
Depth of Inspection | In-depth review of process specifics. | Broader, focusing on key checks rather than exhaustive details. |
Quality Inspection Results | Results detail specific process non-conformities and improvement suggestions. | Results identify recurring compliance trends and opportunities for training or reinforcement. |
Purpose | Detects and corrects process flaws to improve overall quality. | Drives accountability and consistent execution across teams. |
Outcome | Detailed corrective actions tailored to the process. | Continuous improvement and reinforcement of process discipline. |
This distinction ensures that process audits focus on a deep dive into individual processes, while layered process audits sustain overall process consistency and organisational commitment to quality. Manually executing layered process audits can leave you in a pickle, with half-said project logs and forgotten details compounding the issues. Digital process confirmation tools for layered process audits can significantly improve quality inspection results. Start using layered process audits to drive continuous improvement in manufacturing.
How Do Digital Process Confirmation TCards Help Improve Quality Inspection Results in Layered Process Audits?
Reducing non-conformities through consistent layered process audits helping in improving the process quality. Improving accountability in layered process audits with digital process confirmation tools is an easy business with TCards! Are you still in search for digital tools for conducting layered process audits effectively? Choose TCards!
- Automation of Checks: Digital TCards provide real-time, automated prompts for conducting LPAs, ensuring no critical checks are missed, even during high workloads or shift transitions. Creating effective checklists for layered process audits can help in planning and executing the layered audits effectively.
- Consistent Execution: With predefined checklists and digital tracking, TCards standardise the auditing process, reducing variability and ensuring consistent execution across layers.
- Enhanced Accountability: Each TCard is assigned to specific personnel, creating a transparent record of who performed each audit, which step they audited, and the outcomes.
- Real-Time Reporting: Results from digital TCards are instantly captured and transmitted to central dashboards, enabling immediate identification of trends, recurring issues, or areas of non-compliance. Real-time reporting in quality inspection through layered audits helps in early identification of critical issues.
- Efficient Escalation: Non-conformities logged via TCards trigger automatic alerts to the relevant team or management, facilitating faster corrective actions and reducing downtime.
- Data-Driven Insights: Digital TCards aggregate data from LPAs, offering analytics that help identify patterns, recurring problems, or training gaps to enhance overall process quality.
- Adaptability and Integration: These tools can be customised for different processes and integrated into broader quality management systems, making them adaptable to evolving requirements.
Boost Process Efficiency and Quality—Master Layered Process Audits Today!
Layered Process Audits (LPAs) are a game-changer for improving quality inspection results, fostering consistency, and reinforcing process discipline. Unlike traditional audits, LPAs bring accountability across organisational levels, ensuring everyone, from operators to senior management, plays an active role in maintaining quality standards. By leveraging tools like digital process confirmation TCards, LPAs enable real-time tracking, instant reporting, and efficient escalation of issues, transforming how organisations detect and address non-conformities. The result? Enhanced compliance, fewer defects, and a culture of continuous improvement. Elevate your quality game—make LPAs your secret to sustained excellence!
FAQs
1. What is a Layered Process Audit (LPA)?
A Layered Process Audit (LPA) is a structured approach to quality inspection where multiple layers of management or team members conduct regular audits on a process. Each layer focuses on different aspects of the process, ensuring continuous improvement and higher-quality results through collaborative oversight.
2. How do LPAs improve quality inspection outcomes?
LPAs improve quality by providing frequent, in-depth audits at various levels of the organization. This multi-layered approach increases accountability, helps identify potential issues early, and ensures that quality standards are consistently met across all stages of production.
3. What are the key benefits of using Layered Process Audits?
The main benefits of LPAs include improved consistency in quality inspections, faster identification of process weaknesses, enhanced communication between teams, and continuous improvement in production standards. LPAs also support compliance and increase the likelihood of identifying root causes of defects.
4. How often should Layered Process Audits be conducted?
LPAs should be conducted regularly, with the frequency depending on the process's complexity and industry requirements. Typically, audits are carried out on a daily or weekly basis to ensure ongoing monitoring and improvement, but this can vary based on the organization’s needs.
5. Who should be involved in conducting Layered Process Audits?
LPAs involve multiple levels of the workforce, including supervisors, managers, and team leads. The goal is to have individuals from different departments and roles participating to ensure a comprehensive audit that considers different perspectives and areas of expertise.
A Layered Process Audit (LPA) is a structured approach to quality inspection where multiple layers of management or team members conduct regular audits on a process. Each layer focuses on different aspects of the process, ensuring continuous improvement and higher-quality results through collaborative oversight.
2. How do LPAs improve quality inspection outcomes?
LPAs improve quality by providing frequent, in-depth audits at various levels of the organization. This multi-layered approach increases accountability, helps identify potential issues early, and ensures that quality standards are consistently met across all stages of production.
3. What are the key benefits of using Layered Process Audits?
The main benefits of LPAs include improved consistency in quality inspections, faster identification of process weaknesses, enhanced communication between teams, and continuous improvement in production standards. LPAs also support compliance and increase the likelihood of identifying root causes of defects.
4. How often should Layered Process Audits be conducted?
LPAs should be conducted regularly, with the frequency depending on the process's complexity and industry requirements. Typically, audits are carried out on a daily or weekly basis to ensure ongoing monitoring and improvement, but this can vary based on the organization’s needs.
5. Who should be involved in conducting Layered Process Audits?
LPAs involve multiple levels of the workforce, including supervisors, managers, and team leads. The goal is to have individuals from different departments and roles participating to ensure a comprehensive audit that considers different perspectives and areas of expertise.