Gemba Walk Frequency and Focus: Setting an Optimal Schedule for Continuous Improvement
February 10, 2025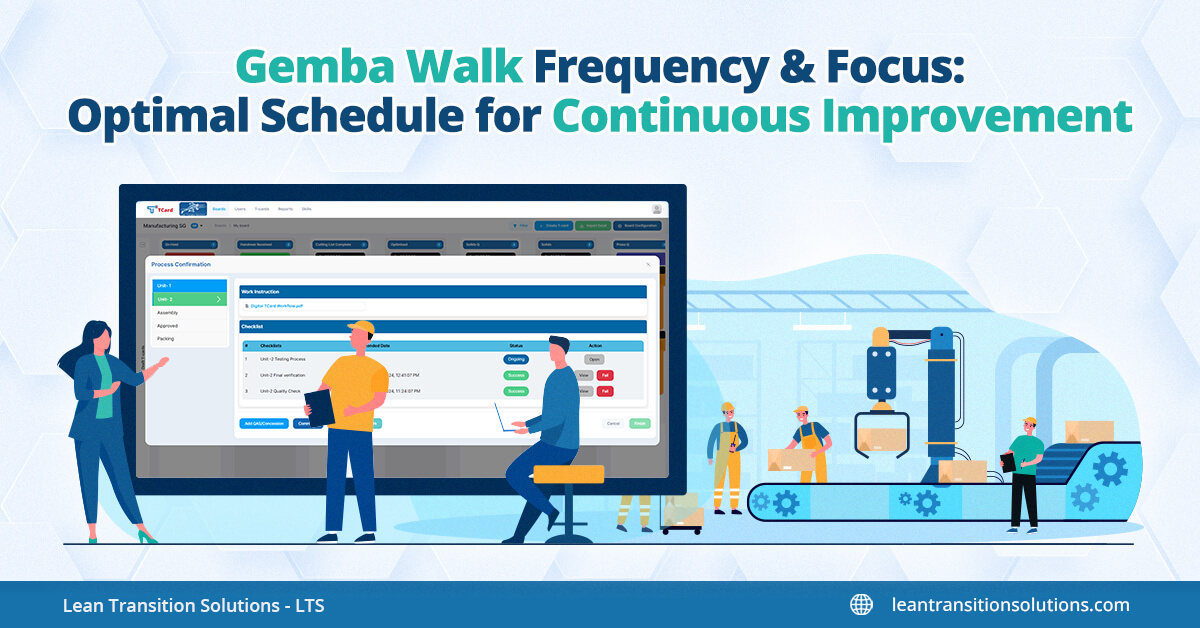
Stopping by Mr. Grey and his chirpy sparrow to ask if he’s booked his doctor’s appointment for next week, waving at Mrs. Cookies and telling her loudly, “The banana pancakes smell extra special today,” checking for seating inquiries, buying the daily milk carton, and checking on the dog food for Bolt – these are the daily huddles Mrs. Updated has to do. Or we could call it the most informal version of a Gemba Walk we could come up with, on a lighthearted note. But seriously, how often do you ask for task updates or project statuses on your shopfloor or work unit? Or better yet, how often should you check in with your teammates to ensure a hassle-free shopfloor management? Find the best frequency for Gemba walks in continuous improvement.
Purpose, Process, and People: The Magical Bonds of a Successful Gemba Walk for Superior Process Efficiency, Advanced Product Quality, and Smart Workflow Management
Every shopfloor witnesses a sequence of actions classified by priority, deadlines, and pipeline stages. These small tasks build together, stage by stage, across departments to create the entire process that yields results. And what holds them together is constant, collaborative communication, consistent updates, and timeline checks. Shift managers walking around the shopfloor collecting updates on project cycles completed, dependencies, blockages, downtime risks, and machine condition updates is how we traditionally see a Gemba Walk.
However, missing details, forgetting questions to raise, or action plans to initiate can go unnoticed – and it’s just human. Developing solutions that enhance efficiency and minimise waste (whether time or effort) lies at the core of our work philosophy (since we’re lean experts). That’s why we’ve gone the extra mile and developed virtual Gemba Walks with Gemba Boards that can save you a day and spearhead sprint workflow management without a single step (literally speaking).Want to get more insights on virtual Gemba Walks and the optimal Gemba walk frequency for process efficiency in the UK? Get all your doubts on scheduling Gemba walks for successful project management clarified with us.
However, missing details, forgetting questions to raise, or action plans to initiate can go unnoticed – and it’s just human. Developing solutions that enhance efficiency and minimise waste (whether time or effort) lies at the core of our work philosophy (since we’re lean experts). That’s why we’ve gone the extra mile and developed virtual Gemba Walks with Gemba Boards that can save you a day and spearhead sprint workflow management without a single step (literally speaking).Want to get more insights on virtual Gemba Walks and the optimal Gemba walk frequency for process efficiency in the UK? Get all your doubts on scheduling Gemba walks for successful project management clarified with us.
How Often Should You Do Gemba Walks?
How to set a Gemba walk schedule for operational efficiency? We will help you sort this out. Gemba Walks should be conducted regularly, depending on your organisation’s goals and the areas being assessed. For manufacturing or operational settings, weekly or bi-weekly Gemba Walks are ideal to maintain oversight and foster continuous improvement. For project-specific or strategic goals, monthly walks may suffice. The key is consistency to build trust, identify bottlenecks, and ensure processes align with organisational objectives. Learn how to improve product quality with Gemba walks.
How Often Should You Do Virtual Gemba Walks?
Following effective Gemba walk strategies for improving workflow management rewards in process improvement. The frequency of virtual Gemba Walks depends on your organisation’s goals, operational needs, and the areas you want to address. However, here are some general guidelines:
- Daily or Weekly – For dynamic environments such as manufacturing or service operations, frequent virtual Gemba Walks (daily or weekly) help maintain process control, address immediate issues, and ensure continuous improvement.
- Bi-Weekly or Monthly – For less dynamic settings or strategic reviews, bi-weekly or monthly walks may suffice to monitor progress and identify long-term improvement opportunities.
- Project-Based – For specific projects or new initiatives, schedule virtual Gemba Walks at critical milestones to review progress and align efforts.
- On-Demand – Use virtual Gemba Walks as needed to address specific challenges, resolve issues, or provide leadership presence in dispersed teams.
Features of Virtual Gemba Walks for Remote Teams in Continuous Improvement
Are you aware of the Gemba walk checklist for a successful Gemba? Explore our digital process improvement tools that help you meet the checklist requirements. We offer advanced virtual Gemba Walk solutions designed to enhance efficiency and engagement:
- Real-Time Collaboration: Allows team members and leaders to interact live via video, ensuring immediate feedback and discussions.
- Digital Process Mapping: Visual tools to document workflows and identify inefficiencies during the walk.
- Data-Driven Insights: Integrated dashboards provide real-time performance metrics for informed decision-making.
- Cross-Location Engagement: Enables participation across multiple locations simultaneously, fostering inclusivity and collaboration.
- Documentation and Reporting: Automated recording of observations, action points, and follow-ups for streamlined implementation of improvements.
Virtual Gemba Walk Best Practices for Lean Management and How TCard Supports Them
1. Set Clear Objectives for Each Walk
⮚ TCard Feature: Goal Tracking
Allows users to set specific goals for each virtual Gemba walk, ensuring clarity and alignment with lean management principles.
2. Schedule Regular Walks
⮚ TCard Feature: Automated Scheduling and Notifications
Ensures walks are planned consistently, with reminders to keep teams on track and avoid missed sessions.
3. Engage Team Members Actively
⮚ TCard Feature: Collaborative Workspaces
Facilitates real-time discussions and task assignments, fostering active participation from all team members.
4. Focus on Data-Driven Insights
⮚ TCard Feature: Integrated Data Dashboards
Displays real-time performance metrics, helping leaders make informed decisions during the Gemba walk.
5. Document Observations and Follow-Ups
⮚ TCard Feature: Observation Logs and Action Plans
Provides tools for recording observations and creating actionable follow-ups directly linked to specific tasks.
6. Address Issues Immediately
⮚ TCard Feature: Issue Reporting and Tracking
Enables quick reporting of issues and monitors their resolution, ensuring timely interventions to prevent delays.
7. Ensure Process Visibility
⮚ TCard Feature: Digital Process Mapping
Offers visualisation tools for workflows, helping teams identify inefficiencies and optimise processes during virtual walks.
8. Foster Cross-Location Collaboration
⮚ TCard Feature: Multi-Location Integration
Supports engagement with dispersed teams by connecting multiple sites through a unified virtual platform.
9. Review and Optimise Workflows Continuously
⮚ TCard Feature: Continuous Improvement Tools
Tracks progress and evaluates workflow changes over time, aligning with lean management's continuous improvement goals.
10. Ensure Follow-Up Accountability
⮚ TCard Feature: Task Assignment and Monitoring
Assigns tasks with deadlines and tracks their completion, ensuring accountability and sustained improvements.
By integrating these features, TCard empowers organisations to conduct effective virtual Gemba walks that align with lean management practices, enhancing efficiency, collaboration, and overall process optimisation.
⮚ TCard Feature: Goal Tracking
Allows users to set specific goals for each virtual Gemba walk, ensuring clarity and alignment with lean management principles.
2. Schedule Regular Walks
⮚ TCard Feature: Automated Scheduling and Notifications
Ensures walks are planned consistently, with reminders to keep teams on track and avoid missed sessions.
3. Engage Team Members Actively
⮚ TCard Feature: Collaborative Workspaces
Facilitates real-time discussions and task assignments, fostering active participation from all team members.
4. Focus on Data-Driven Insights
⮚ TCard Feature: Integrated Data Dashboards
Displays real-time performance metrics, helping leaders make informed decisions during the Gemba walk.
5. Document Observations and Follow-Ups
⮚ TCard Feature: Observation Logs and Action Plans
Provides tools for recording observations and creating actionable follow-ups directly linked to specific tasks.
6. Address Issues Immediately
⮚ TCard Feature: Issue Reporting and Tracking
Enables quick reporting of issues and monitors their resolution, ensuring timely interventions to prevent delays.
7. Ensure Process Visibility
⮚ TCard Feature: Digital Process Mapping
Offers visualisation tools for workflows, helping teams identify inefficiencies and optimise processes during virtual walks.
8. Foster Cross-Location Collaboration
⮚ TCard Feature: Multi-Location Integration
Supports engagement with dispersed teams by connecting multiple sites through a unified virtual platform.
9. Review and Optimise Workflows Continuously
⮚ TCard Feature: Continuous Improvement Tools
Tracks progress and evaluates workflow changes over time, aligning with lean management's continuous improvement goals.
10. Ensure Follow-Up Accountability
⮚ TCard Feature: Task Assignment and Monitoring
Assigns tasks with deadlines and tracks their completion, ensuring accountability and sustained improvements.
By integrating these features, TCard empowers organisations to conduct effective virtual Gemba walks that align with lean management practices, enhancing efficiency, collaboration, and overall process optimisation.
Key Focus Areas for Gemba Walks in Manufacturing Environments
- Process Observation: Assess the current workflow and identify inefficiencies, bottlenecks, or unnecessary steps that could be improved.
- Safety and Compliance: Ensure that safety protocols and regulatory requirements are being followed, and check for any potential hazards.
- Employee Engagement: Observe worker engagement, morale, and challenges to address concerns and foster a culture of continuous improvement.
- Quality Control: Monitor product or service quality to identify any defects or areas for improvement in processes or training.
- Waste Identification: Look for waste in terms of time, resources, and energy, and explore opportunities for lean practices to streamline operations.
- Performance Metrics: Check key performance indicators (KPIs) or other data to verify if processes align with organisational goals and targets.
- Customer Impact: Ensure that processes and operations are directly aligned with customer needs, focusing on delivering value.
Steps to Take When You Start Losing Focus
- Pause and Refocus: Take a step back and reflect on the purpose of the Gemba Walk. If necessary, reframe the focus to avoid distractions.
- Set Clear Objectives: Before each walk, establish specific goals or questions to guide your observation, ensuring the walk remains purposeful.
- Involve Team Members: Engage with the team on the floor and ask targeted questions to ensure you're capturing relevant insights.
- Use Data: Lean on performance data, reports, and KPIs to ground your focus and direct your attention to the most critical areas.
- Take Notes: Document observations and thoughts as you go along to help refocus when the walk begins to veer off track.
- Review and Adjust Focus Mid-Walk: If attention starts to drift, re-evaluate the key areas you need to focus on based on immediate findings or feedback.
How Virtual Gemba Walks Can Help Maintain Focus
- Data-Driven Insights: Virtual Gemba Walks often integrate real-time data dashboards, which help keep the focus on key metrics and performance indicators, preventing distractions.
- Clear Agenda: Virtual Gemba Walks can be pre-scheduled with a specific agenda that participants can refer to, ensuring everyone stays on track.
- Remote Collaboration: Through video conferencing tools, team members and managers can engage in focused discussions without physical distractions, enhancing clarity and purpose.
- Visual Monitoring Tools: Virtual tools such as cameras, sensors, and digital process mapping provide a focused view of the operational environment, guiding attention to the most critical aspects.
- Documenting Insights: Virtual platforms allow for easy note-taking and immediate documentation, ensuring that observations are captured without losing focus during the walk.
Action Plan for Missed Gemba Walks
Step | Corrective Action | Recommendations |
---|---|---|
1. Identify the Cause | Determine why the Gemba Walk was missed (e.g., scheduling conflicts, lack of prioritisation, or emergencies). | Review the calendar and establish a clear understanding of obstacles to prevent recurrence. |
2. Reschedule Promptly | Set a new date for the missed Gemba Walk as soon as possible to maintain momentum. | Notify all relevant stakeholders about the new schedule and ensure their availability. |
3. Review Missed Insights | Gather reports, logs, or updates from the missed period to identify any potential issues or changes. | Leverage data or feedback from team members to fill the gap caused by the missed walk. |
4. Adjust Future Plans | Update the Gemba Walk schedule to accommodate additional time or focus on areas neglected during the missed walk. | Consider increasing the frequency temporarily to ensure all processes are adequately monitored. |
5. Enhance Communication | Inform teams of the missed walk and reassure them of continued management commitment to improvement. | Reinforce the importance of regular Gemba Walks to all stakeholders, emphasising their role in success. |
6. Analyse Impact | Evaluate whether the missed walk led to unresolved issues, delays, or reduced efficiency. | Use this analysis to prioritise areas for improvement in the rescheduled walk. |
7. Implement Preventive Measures | Develop strategies to avoid missing future Gemba Walks, such as setting reminders or assigning backups. | Incorporate Gemba Walks into routine processes and appoint a deputy leader to conduct walks in emergencies. |
By following this structured approach, organisations can minimise the impact of missed Gemba Walks and maintain their commitment to continuous improvement.
Unlock Operational Excellence: Find the Right Frequency & Focus for Your Gemba Walks!
Consistency is key when it comes to Gemba Walks but so is focus. Whether you’re tackling immediate issues or working on long-term improvements, finding the right balance in frequency and focus is crucial for sustained success. Frequent Gemba Walks ensure you're always in touch with what's happening on the ground, while targeted focus helps you zero in on the areas that truly need attention. Don’t miss out on the opportunity to drive continuous improvement—start scheduling your Gemba Walks with purpose and precision today!
FAQ's
1. What is a Gemba Walk, and why is it important?
A Gemba Walk is a management practice where leaders visit the actual workplace (the "Gemba") to observe processes, engage with employees, and identify opportunities for improvement. It fosters collaboration, uncovers inefficiencies, and promotes a culture of continuous improvement.
2. How often should Gemba Walks be conducted?
The frequency of Gemba Walks depends on the organisation’s size, goals, and industry. Typically, weekly or bi-weekly walks are recommended for sustained improvement, but the schedule can be adjusted based on specific needs or ongoing projects.
3. What should be the main focus during a Gemba Walk?
The focus should be on understanding workflows, identifying bottlenecks, and gathering input from frontline employees. It’s crucial to observe without interrupting work and to ask open-ended questions to encourage insights and feedback.
4. How long should a Gemba Walk last?
A Gemba Walk usually lasts 30 minutes to an hour, depending on the complexity of the process being observed. The key is to ensure thorough observation and meaningful interactions without overburdening employees.
5. What are the common mistakes to avoid during a Gemba Walk?
Avoid turning the walk into an inspection, making assumptions without data, or providing immediate solutions. The purpose is to observe, listen, and gather insights for collaborative problem-solving rather than assigning blame or micromanaging.
A Gemba Walk is a management practice where leaders visit the actual workplace (the "Gemba") to observe processes, engage with employees, and identify opportunities for improvement. It fosters collaboration, uncovers inefficiencies, and promotes a culture of continuous improvement.
2. How often should Gemba Walks be conducted?
The frequency of Gemba Walks depends on the organisation’s size, goals, and industry. Typically, weekly or bi-weekly walks are recommended for sustained improvement, but the schedule can be adjusted based on specific needs or ongoing projects.
3. What should be the main focus during a Gemba Walk?
The focus should be on understanding workflows, identifying bottlenecks, and gathering input from frontline employees. It’s crucial to observe without interrupting work and to ask open-ended questions to encourage insights and feedback.
4. How long should a Gemba Walk last?
A Gemba Walk usually lasts 30 minutes to an hour, depending on the complexity of the process being observed. The key is to ensure thorough observation and meaningful interactions without overburdening employees.
5. What are the common mistakes to avoid during a Gemba Walk?
Avoid turning the walk into an inspection, making assumptions without data, or providing immediate solutions. The purpose is to observe, listen, and gather insights for collaborative problem-solving rather than assigning blame or micromanaging.