
Schedule Your Work Orders with T Card Software
Visualise production plans and allocate work orders to machines automatically.
Start for free Get a DemoTrusted Partner for Businesses
Across the World
Irrespective of industries, Digital T Card Software enhanced their business processes.
Visualise Production Plans with Digital T Cards
Flexible | Visibility | Unlimited Cards | Web Based T Card | Activity Stream | Drag and Drop
T Card software is a web based solution for production planning, employee scheduling and production execution. This web based t card solution helps the manufacturer to transform the factory into an Industry 4.0 environment.
- Replace Physical T Cards
- T Card for Production Planning
- Simplified IT Administration
- Work Order Planning, Scheduling, Tracking and Execution
- Individual and Team Board View
- Detailed Card Information with Specifications
- Checklist for Each Process
- Easy to Reschedule the Tasks
Simple Dashboard View of Entire Production Plan
Machine Availability | Work Order Allocation | Scrap Analysis
Visualise your production plans with T card Software. Digital T card software accurately keeps track of the entire process, from work order planning to execution.
- Work Order Planning and Execution
- Optimise Overall Process
- Save Time and Reduce Confusions
- Allocate Machines for Each Work Order
- Records and Analyse Scrap
- Web t cards/Online T card system


Wrestling with Work Order Management?
Work Order | Timeline | Check sheets | Switch Process
T Cards online software effectively tracks and manages all work order information through a single dashboard and ensures all the processes are completed in the right way-every time. It provides a visual representation of the workflow, employee shift cycle, risk management, and downtime reporting. Our T cards systems allows manufacturers to quickly create a work order, timeline activities, work status, and check sheet to improve the production process by optimising the process.
- Visual Work Order Planning and Management
- Timeline Representation of the Workflow
- Check Sheets to Ensure Quality
- Work Order Status and Percentage of Completion
Automatically Allocate Work Orders!
OEE | Production Planning | Work Order Allocation
Digital T Card system software will track real-time information on machines available for production. A newly received work order can be easily allocated to machines. Machine availability in manufacturing denotes the efficiency of the machine that is run time vs planned production time.
- Machine Availability
- Real-Time Information
- Work Order Management
- Run Time vs Planned Production Time


Easily Track, Manage & Streamline Shift Management
Shift Type | Employee Shift Assign | Shift Duration | Shift Calendar
It is important to have a streamlined employee shift management process to ensure a smooth production flow in the factory. The employee shift management module enables the employer to effectively optimise their shift scheduling, planning, and shift calendar with utmost accuracy.
- Streamlined Shift Management
- Integrated Shift Planning and Scheduling
- Track Employees
- Work Shift Calendar
Measure OEE, the Heart of Manufacturing!
Best Manufacturing Practice | Measure Productivity and Effectiveness
Overall Equipment Effectiveness (OEE) is the standard for measuring manufacturing productivity. It helps manufacturers identify the percentage of manufacturing time that is truly productive.
- OEE Analysis
- OEE Reports
- Insights on Improving Manufacturing Process
- Productive Manufacturing

Start your TCard free trial today!
Experience the power of TCard software tailored for your manufacturing needs.

Maximise Efficiency, Stay on Track
Detailed Reports | Easy Analysis of Shifts | Identify Highly Productive Shifts
Shift Output Reports shows the productivity of different shifts. The efficiency of machines that work on each shift is analysed and reports are auto-generated. Manufacturers can identify the shifts that have high productivity levels and can allocate work orders.
- Real-Time Reports
- High Productivity
- Auto-Generated Reports
- Machine Efficiency

Real-Time Scrap Report Analysis
Scrap Analysis | Scrap Reason | Root-Cause Analysis |
The scrap reporting option in the T Cards systems provides the ability to record and analyse scrap reason that occurs during the production process.
- Recording Scrap Number and Scrap Reason
- Real-Time Scrap Reason Analysis
- Root-Cause Analysis
- Prevent Recurrence
Job History and Risk Management
Hazard Level | Risk Ranking | Track and Report Risk | Risk Duration
Job history provides a complete record of the job scheduled for each employee. A single click can quickly view shift patterns, working hours, and hazard level details. As the complexity of high risk level task grows, there is a critical need for efficient ways of structuring the risk landscape.
- Details of Scheduled Tasks
- Measure Hazard Level
- Real-Time Accessibility
- Risk Analysis and Control

Explore possibilities for Individual Improvement
Employee Skills | Competency Levels | Individual Improvement
An employee skills matrix gives an overview of a team’s skills, knowledge and competency levels. Using a skill-matrix, employers can quickly identify employee skill levels in different operations.
- Team’s Skill Overview
- Employee Appreciation
- Skill Identification
- Increase Competency Level


Easily Connect to MES & ERP Systems
Integrated Communication | Automation | Single Sign-On | Data Consistency | Rest API
Digital T card system software is dynamic as it will integrate with the other management information and ERP systems in the organisation. The Electronic T Card systems automatically receives all the departmental data from the ERP system using the REST API service.
- No Data Redundancy
- Increased Flexibility and Process Efficiency
- Centralised and Accessible Information
- Saves Data Entry Time and Cost
- Comprehensive Process Visibility
- Integrated Operation
Start your 14 days free trial and take the first step toward a smarter workflow today!
Dynamic Production Reports and Charts
Dynamic Reports | Graphical Representation | Detailed Analysis
Digital Tcard Reports give you a graphical overview of the production process. Customise multiple reports for the organisation to track and monitor overall performance. Generate your reports according to the requirements. It varies from OEE reports, shift output reports, scrap reports, and MPS reports to downtime reports.
Read More
Execute Manufacturing Production Plans and Digital Work Instructions with Digital T-cards!

Tcards are visual management tools that provide an overview of the manufacturing processes in the industry. Through the production scheduling overview and the workflow management determinants, Tcard provides room for continuous improvement. Digital T Cards offers an online solution for production planning and work order execution. The Manufacturing Order management attribute of the Tcard plans, allocates, tracks and improves the work order management system.
Elevate your manufacturing operations with Tcard softwareContents
- What services can Digital T card systems offer in the manufacturing or production, planning and execution?
- What is a Manufacturing order, and what does it contain?
- What are the benefits of using this Manufacturing order Management system in production, planning and execution?
-
Work Order Management System in Production
- 4.1What is a work order management system?
- 4.2Why is the work order management system important?
- 4.3What is a work order and the purpose of it?
- 4.4How is a work order management system managed?
- 4.5What are the types of work orders?
- 4.6What should a work order include?
- 4.7What are the benefits of using an effective work order management system?
- 4.8What is work order tracking, and why is it important?
- 4.9What is the difference between manufacturing order and work order?
- Why is Overall Equipment Effectiveness or OEE important in manufacturing?
- 5.1What is Overall Equipment Efficiency or OEE?
- 5.2What does Overall Equipment Effectiveness measure?
- 5.3How is overall equipment effectiveness used?
- 5.4Why is Overall Equipment Effectiveness(OEE) important?
- 5.5What are the three components of OEE?
- 5.6How is the Overall Equipment Effectiveness(OEE) calculated?
- 5.7What does an OEE of 100% refer to? What is a good OEE score?
- 5.8What is Overall Line Efficiency?
- 5.9What is Overall Process Efficiency(OPE)?
- 5.10What is the difference between OEE and OPE?
- 5.11What is Overall Labour Effectiveness(OLE)?
- 5.12What is OOE or Overall Operation Effectiveness?
- 5.13What is TEEP? How is it calculated?
- Shift Management in Manufacturing
- Develop Effective Work Force with Digital Work Instructions
- 7.1What are Digital Work Instructions?
- 7.2Why are Digital Work Instructions important?
- 7.3What are the benefits of using Digital Work Instructions in production?
- 7.4What makes an excellent digital work instruction?
- 7.5How do you create outstanding digital work instructions?
- 7.6What are the popular use cases of the smart work instructions?
What services can Digital T card systems offer in the manufacturing or production, planning and execution?
- Optimising workflow
- Production Scheduling Overview
- Track every order stage and Work In Progress(WIP)
- Order Prioritisation
- Task Visualisation
- Continuous improvement
- Just In Time(JIT) Manufacturing
- Inventory Management
- Time Management and planning ahead
- Agile Delivery
- Track Spare capacity
- Record slippages and bottlenecks
- Complex processes made simple
- Flexibility of the virtual system
- Shortening cycle time and overlapping the tasks
- Expediting critical tasks through collaboration
- Advanced Reporting and insightful analytics
Digital Tcard provides room for continuous improvement through the production scheduling overview and workflow management indicators. The Manufacturing Order Management attribute of the Tcard plans, allocates, tracks and improves the work order management system.
Read MoreWhat is a Manufacturing order, and what does it contain?
A document or schedule which contains the relevant details of the manufacturing of the specified parts or products in fixed quantities, manufacturing order constitutes the following:
- Manufacturing Order number and date
- Product Name
- Job Quantity or the order quantity
- Delivery date or the expected customer delivery date
- Process start date
- Raw material transportation and expected date of the transfer
- Finished product transfer date and the dispatch date
- Process end date
- Inspection and packing details include quantity, unit of measurement, internal process stage, accepted and rejected quantity and the total cost of the product.
The manufacturing order cycle manages the manufacturing order.
- Order Placement: As soon as the customer places the order, the details are automatically fed into the system.
- Order Fulfilment: The proceedings start with assigning the task to the corresponding department. An availability check for material requirements is done, and if it is available at the warehouse, the processing starts directly. If not, a material request is created, and the task continues as soon as the availability is fulfiled.
- Quality Inspection: The integrated quality inspection is done to check the quality of the deliverables if they are free from defects and comply with the predetermined criteria.
- GRN: When the items are out for delivery, the Goods Received Note, or the dispatch notes are generated.
- Inventory Updates: The inventory levels updated in case of any inventory moves provide accurate information about how much quantity of a particular item needs to be stocked.
- Reports and Dashboards: The combined data from the various departments in the production track, visualise and identify cost savings.
- Shipment: The order is dispatched, and the item will be recorded as the delivered order.
What are the benefits of using this Manufacturing order Management system in production, planning and execution?
- Efficiency: With less room for manual errors, increasing efficiency can beget greater attention to the industry's growth and greater customer satisfaction.
- Flexibility: An integrated order management system permits accessibility of the order details anywhere, at any time and on any device.
- Real-time data: Quick decisions and immediate solutions are the results of real-time data analysis of the process, the inventory or the product.
- Inventory management: The system is capable of enhancing the control of the inventory by providing real-time data about the stock levels, stock-outs, billed items, production items and others, which in turn can help to reduce both the under and overstocks.
- Productivity and Profitability: The increased productivity through real-time data analysis will increase the company's profitability.
Most of the time, the production order is used in place of the manufacturing order. More or less, it is the same. Production order acts as a check or a guide for the information about the lists of specific materials, parts, or inventory used in the process.
Work Order Management System in Production
What is a work order management system?
A systematic approach to processing and completing the work order on time to minimise asset downtime, a work order system depends on the availability of the other resources such as assets, parts, people and money for completion.
Why is the work order management system important?
Traditionally, the maintenance teams depended on the paper-based work order to assign the job assignments. Though it seemed easy to be created, the management of the paper-based work orders was labour intensive and often created problems like incorrect documentation and copies getting misplaced or lost.
Some maintenance teams then advanced to spreadsheet-based work order management, which also had limitations. It was to be modified by a single person at a time and hence could not provide the updated information. Even these work orders were required to be printed on paper, which repeated the disadvantages of the manual system.
With the advancement of time, the older versions of the work order management system proved inefficient and unfeasible. The additional focus on operational efficiency shifted the physical work order system into a digital one.
What is a work order and the purpose of it?
A work order is a formal document containing information about the maintenance work approved for execution or an approved work request, whether paper or digital. The staff or customers submit the work requests to the maintenance department depending on the type of businesses, industries and facilities they manage. In addition, the work orders also contain details about the work that needs to be completed, like the location, skill requirements and the tools required.
The work order's primary purpose or goal is to provide the details of the work performed. The data recorded on the work order allows the monitoring or analysis of the performance.
How is a work order management system managed?
A proper work order management system regulates the work order from the initial request stage to the conclusion.
- Work Request Approval: An approver reviews the service request and determines if it is ready to create a work order. If the request is valid, the work order is approved.
- Work Order Creation: The authorisation to perform the requested work is generated.
- Prioritisation: Prioritising is usually determined by the criticality of the job or the asset. For instance, the work orders relating to the safety of the site or the staff will be given a high priority.
- Scheduling: Priority acts as the key factor here. Emergency work orders are addressed without delays. Other factors include the availability of the technicians, spare parts, supplies and tools.
- Assignment: Every team consists of workers with varying skills and abilities, and the assignments are done accordingly.
- Execution: Task execution occurs here.
- Documentation: Whatever the outcome may be, all the work orders are documented. These documents contain information about how much time was spent, what parts were used and the other details which can help identify the areas of improvement and be used for further troubleshooting.
- Closure: When all the tasks have been performed, services delivered, and the job is completed, the work order is closed.
- Analysis: Collective work order history forms the foundation of analysis.
What are the types of work orders?
- Unplanned Work Order: The work order that has not been planned ahead of time, includes a machinery breakdown.
- Planned Work Order: The work recurs and can be scheduled ahead of time, such as preventative maintenance or other automatic updates.
- Internal Work Order: This type of work order is assigned within an organisation; it originates from someone in the organisation and is assigned to another person within the same organisation. Mainly the internal works are digital.
- External work order: When the work order originates outside the organisation, these are reviewed and scheduled before execution.
- Manual Work Order: Scheduling a work order by hand after receiving a work request. They can be both internal and external.
- Automatic work order: The work order can be set up to automatically schedule the assignments to corresponding employees through the software tools.
What should a work order include?
A good work order contains different sections to provide the essential information for an effective understanding. All the areas in the work order are interconnected and linked, which can cause a problem if one among the sections does not perform well.
The work order should include:
- Asset: The description of the equipment involved in this work order.
- Description of the work: A detailed specification of the customer's requirements or issues.
- Scope of work: What work is required to finish the job, and what skills are needed.
- Parts and tools required: Note any parts that need replacement or additional support.
- Health and safety note: A complete checklist of the safety procedures in the industry.
- Task checklist: Steps required to complete the work order.
- Priority: A note specifying the urgency of the task.
- Dates: When was the work order created and submitted? Expected and actual completion date. Expected and actual hours of work.
- Original Point of Contact:Reference of who created and submitted the work order
- Assigned to: To whom is the work order assigned, and how many persons are required to complete it? Is an outside contract required?
- Associated Documents: Relevant resources that can help complete the work order more efficiently. It includes the Standard Operating Procedures(SOP), manuals, diagrams, videos, asset and service histories, purchase orders and images.
- Notes: Any additional information or observations can help complete the work order. These can be the troubleshooting techniques that were made previously.
What are the benefits of using an effective work order management system?
A proper work order system helps simplify the work orders' planning and management. It assists the organisations in tracking, prioritising, and completing the work orders across the industry and in fact, it is vital for ensuring the organisation's smooth operation.
- Efficiency in management and communication
- Increase the performance of the equipment
- Boost employee productivity
- Reduce overtime
- Minimise paperwork
- Optimising preventive and corrective maintenance
- Improved safety
- Improved planning and budgeting with data and performance of the previous orders
What is work order tracking, and why is it important?
An efficient work order tracking system forms the backbone of an order management system that visualises the productivity data and tracks everything happening on the shop floor in real-time. A work order tracking system is a method for following the production process against a specific work order. It ensures that if each job is produced on time, the bottlenecks are identified and resolved at the earliest, all the concerned departments are working together as an organised whole, and visibility in the Work In Progress(WIP) is created. Tracking the work order is fundamental to the execution of a plan and to optimising the future planning strategies.
Tracking the work order help in the optimisation of the schedule, which can save both time and money. Real-time access to the work order through tracking can complete the tasks efficiently without losing time and resources on the inefficient processes.
Work order management tools help provide the work orders with updated information, increasing revenue and enhancing business agility. Even the customers will be provided with the updated invoice, and there will be a minor delay.
Inefficient work order tracking systems can lead to costly delays, poor customer experiences and time-consuming errors.
What is the difference between manufacturing order and work order?
- Creation:A manufacturing order is created when a request is placed for a product which has not yet been manufactured. On the other hand, a work order is completed when a customer requests a product already manufactured and in stock.
- Specifications:While the manufacturing order contains the product's specifications that need to be produced, the work order includes the specifications of the required quantities and delivery dates.
- Order: When a manufacturing order should be processed in the order it is received, a work order can be processed in any order.
Streamline your Work Orders Management for free!
Why is Overall Equipment Effectiveness or OEE important in manufacturing?
OEE forms one of the most crucial performance measurements in manufacturing. By optimising the Overall Equipment Effectiveness, the production lines can increase the capacity, reduce the costs and increase the efficiency.
What is Overall Equipment Efficiency or OEE?
Overall, Equipment Efficiency or OEE is a measure of manufacturing productivity. It is the estimated percentage of manufacturing time which is productive. It calculates how well a manufacturing operation is utilised to its full potential during its scheduled run time.
OEE measurement brings insights into how systematic improvements can be brought into the manufacturing process.OEE is an adequate standard for identifying losses, benchmarking progress, and improving manufacturing productivity.
An OEE score of 100 % indicates that the only good parts are produced at maximum speed with no stop time. In OEE, 100% quality indicates that only good parts are made, 100% performance means within minimum time, and 100% Availability means zero stop time.
What does Overall Equipment Effectiveness measure?
OEE provides an understanding of how the manufacturing process is running effectively and how the process can be improved. The three core components of OEE - Availability, Performance and Quality measure the Overall Equipment Effectiveness.
Availability considers both scheduled and unscheduled downtime. A score of 100% in availability means there was no stop time, and the process was always running during the scheduled production time.
The performance considers slow cycles and minor stops. The 100% performance score indicates that the process runs as fast as possible during the planned production time.
Quality indicates the defects or unusable products that need to be reworked or replaced. A 100% quality is an indication that there are no defective products produced and all the products made are in usable condition.
OEE considers all these losses, and if the score is 100%, it indicates that good products are produced with no stop time as soon as possible.
How is overall equipment effectiveness used?
Overall Equipment Effectiveness (OEE) is the most important benchmark for the manufacturing industry. It accesses the operational efficiency and points out the performance issues. It is the actual percentage of time the equipment is truly productive and generates revenue for the company. It is the calculation of the equipment's availability, performance and Quality.
Why is Overall Equipment Effectiveness(OEE) important?
Overall Equipment Effectiveness is the most crucial performance metric used in manufacturing facilities. By enhancing the OEE score, the capacity and efficiency can be increased, the cost reduced, and the Quality improved. Taking steps to improve the OEE always proves beneficial in the long and short or medium term. It is also cost-effective compared to the other alternatives like adding a new shift, increasing over time, purchasing new equipment, and outsourcing production.
What are the three components of OEE?
Three major components of OEE include Availability, Performance and Quality.
- Availability: It considers the events that stop the planned production for a long time, and an analysis is to be done to track the reason.
To calculate availability, you can use the formula of dividing the run time by the planned production time.
The run time is the difference between planned production and stop times. - Performance:It analyses anything causing the manufacturing process to run at a rate less than the maximum speed. It includes both slow cycles and minor stops.
Performance can be calculated as (Ideal cycle time* Total count)/ Run Time The Ideal Cycle Time is the cycle time the process can achieve in optimal conditions.
Performance can never be greater than 100; if it happens, it indicates that the Ideal cycle time is set too high. - Quality: Quality considers the manufactured parts that do not possess the quality standards and may include parts that need rework. Good parts successfully pass through the manufacturing process for the first time without requiring any rework.
Quality =It is the ratio of the fully productive time(Good products produced with maximum speed and no stop time) to Net Run Time( All products produced within maximum speed with no stop time).Good Count
Total count
OEE considers all losses, thereby measuring the truly productive manufacturing time.
OEE =Availability * Performance * Quality
How is the Overall Equipment Effectiveness(OEE) calculated?
OEE combines three factors: asset availability, asset performance and production quality.OEE formula is calculated as follows:
OEE is represented by the percentage.
Let's demonstrate the calculation of OEE with an example;
The first step in the analysis is the calculation of the Asset availability, which is calculated by
Total planned Production Time
For instance, if the machine were supposed to run for 10 hours, but it could only run for 9 hours, then the availability would be the asset availability would be only 90% or 0.9
The Asset performance is calculated by
Maximum PossibleThroughput
When the asset runs for 10 hours with a maximum production rate of 1000 units in one hour makes, the maximum throughput is 10000, but if the asset performs only 9000 units in that time, the performance score is 90% or 0.9
And finally, the Quality of the goods produced by the assets is determined,
the Quality is calculated as
Total Units started
If the asset produces 12000 units in a fixed production time frame and if some 100 pieces don't have the Quality and are defective, then the usable products would be 11900, and the quality score would be 99.1% or 0.991
Now the OEE can be calculated as = 0.9*0.9*0.991 = 0.802 or 80.2%.
What does an OEE of 100% refer to? What is a good OEE score?
A score of 100% in OEE is an indicator of perfect production where only good parts are produced as fast as possible with zero stop time.
A 60% score is a typical value that indicates substantial room for improvement. Processes for automatic optimisation and continuous system monitoring need to be implemented.
A 40% score is a low score, and in most cases, it can be improved through straightforward measures like tracking reasons for stop time and downtime.
What is Overall Line Efficiency?
Overall Line Efficiency is a metric in manufacturing which is not to be confused with OEE. It is a separate metric that analyses the current performance of the production line and contrasts it with how well it could be performing. Along with analysing data relating to machines or equipment, Overall Line Efficiency also considers the staff's productivity to optimise the relations between the data and human resources.
What is Overall Process Efficiency(OPE)?
Total Process Efficiency (TPM) or Overall Process Efficiency measures the effectiveness of a process in delivering products or services while minimising waste generation.
What is the difference between OEE and OPE?
When OEE measures the machine performance, OPE concentrates on the broad perspective, which accounts for what's happening around the machine. OPE accounts for variables and steps that impact the manufacturing process. It integrates what is happening around the machine, representing the human action and the machine's performance.
What is Overall Labour Effectiveness(OLE)?
OLE is a Key Performance Indicator(KPI) that measures the workforce's utilisation, performance, and quality and its impact on productivity. OLE also measures availability, performance and Quality.
- Availability: The percentage of time spent making effective contributions by the employees. It is the ratio of productive time of the workers divided by the amount of the scheduled time.
- Performance: The number of products delivered. It is the ratio of the actual output of the operators to the expected output or the labour standard.
- Quality: The percentage of perfect or saleable products produced, which is the ratio of the saleable parts divided by the total parts produced.
OLE allows the manufacturers to make operational decisions by giving them the ability to analyse the cumulative effect of the three workforce factors on productive output.
What is OOE or Overall Operation Effectiveness?
It is a lesser-used method of measuring production line availability. It is more or less the same as OEE with a slight variation that it distinguishes between the time your plant is operating and the time a machine is scheduled to run.OOE measures the availability from the start of the shift to its end.
What is TEEP? How is it calculated?
Total Effective Equipment Performance or TEEP measures the full potential for the equipment capacity. TEEP measures performance against the total capacity, enabling manufacturers to understand and improve utilisation.
TEEP is calculated by multiplying the performance, Quality and availability.
Shift Management in Manufacturing
A shift management system manages the various types of shifts and aids the organisation in organising and scheduling employee shifts. It is essential in allocation and optimising the resources and the team. A shift is a period allocated to an employee to handle the tasks. Shift management system makes sure that the smooth transitioning between the different shifts.
What is shift planning, and why is it important?
Shift planning is used in industries, especially those that rely on shift work, for example, hospitality, health and other service industries. A shift planning system must balance employee time off, overtime, vacation requests, leaves, and customer demands. The benefits of using shift planning include
- Increased productivity
- Control labour cost
- Increased flexibility
Develop Effective Work Force with Digital Work Instructions
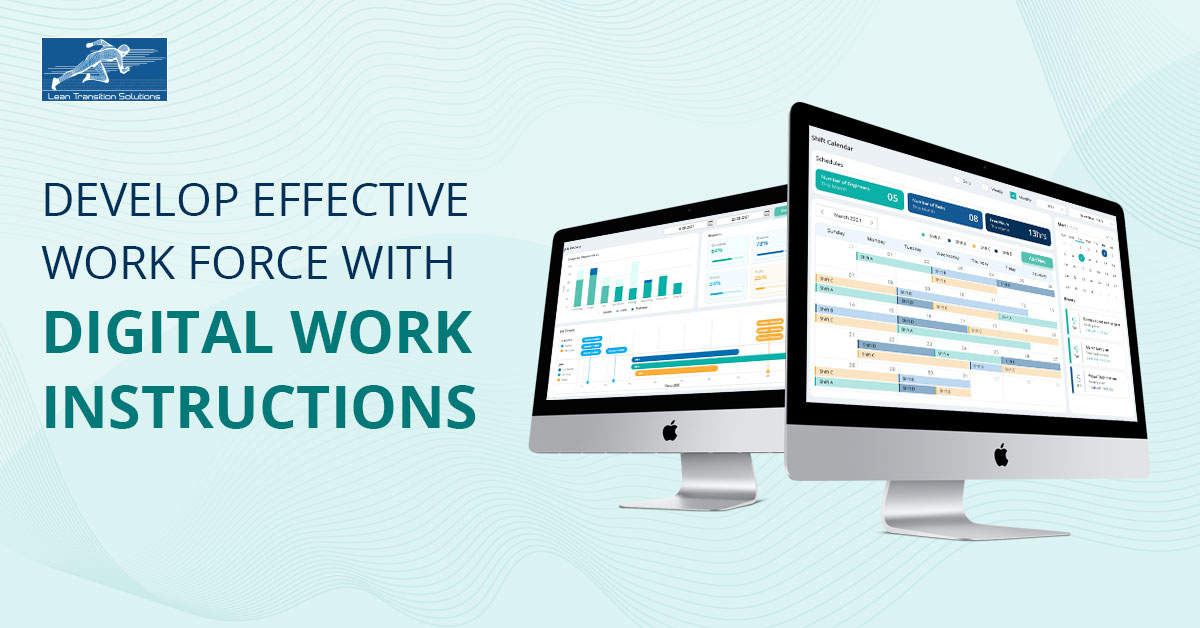
Is your industry facing the challenges of the widening skill gap, employee recruiting and retention? An increasingly hybrid and distributed workforce and loss of tribal knowledge due to the rapidly retiring labour force are forcing the companies to go digital. Boost the operational efficiency of your team using the Digital Work Instruction feature of our online T card software.
Digital versions of the interactive work instructions have a clear upper hand over the traditional paper instructions. As the production and the machines are getting intricate, it is crucial to deliver valid data at the right time to the frontline workers to ensure the plain sailing of the industry. Digital work instructions collect information from multiple production sources and provide it in a simple unified view so that the operators can make quick data-driven decisions.
Let us see what Digital Work Instructions are and how it works.
What are Digital Work Instructions?
Digital Work Instructions are the electronic versions of the work instructions, work order info, product specifications, quality manuals, and Standard Operating Procedure(SOP) in the software that provides visual aids and real-time contextual information to guide the workers through complex tasks.
The digital standard work instructions explain the perfect way to complete a procedure step by step in a digital format. They also translate the processes into a human-centred way of working that allows any employee on the shopfloor to complete the task with ease. The digital manufacturing work instructions connect humans with the machine data to increase quality, reduce scrap and improve safety standards.
The digital work instruction for manufacturing makes tracking the data around the production floor easier. This enables the operators to set more reasonable expectations and address the problem more quickly when the team is not fulfilling their goal. Digitising your work instructions will also create a few apparent opportunities for analytics.
When maintenance is needed, the previous history can be recorded in the system, enabling the next operator who works on that machine has complete clarity over the overall machine health and maintenance history.
Why are Digital Work Instructions important?
Traditional paperwork instructions have become obsolete. Lengthy, hard-to-produce manual entry of the work instruction can produce more troubles than solutions. Good actionable digital work instructions are essential for a company as they can list the best way to complete the procedure in a standardised way. They can translate the process into a human-centric way of understanding a system to complete a task on the shop floor efficiently and safely. From consolidating the work instructions and process data to eliminating instruction latency and increasing overall workforce flexibility and productivity, a digital workforce can optimise your workforce. It can empower the employees to innovate faster, collaborate effectively and make higher quality products at a minimal cost. Tracking data for every set of work instructions to learn how long each operator spends on tasks is also an effective factor in this.
What are the benefits of using Digital Work Instructions in production?
- Continuous improvement of the process and boosting of product quality
- Streamline process improvements and increase productivity
- Increased operational efficiency and safety
- Reduce occurrence of the machine changeover, downtime and production delays
- More effective training procedures & more motivated workforce
- Crowdsource knowledge and capturing the tribal knowledge-Turn the frontline team's expertise into shareable work instructions
- Standardised operating procedures
- Access operational knowledge
- Error-free version control
- Improvement in line efficiency
- Keep track of everything with traceability.
- Minimise risk and operational disruptions
- Collect real-time data to make informed decisions
- Decrease Documentation Efforts
- Allow visual instructions along with the written instructions.
- Stored in a central place which can be accessible from multiple sites
Once you have digitised your work instructions, you can also digitalise your workflow management using the digital T card systems and combine them into a single flow for the operator.
What makes an excellent digital work instruction?
Key considerations to be made while creating standard Digital Work Instructions include:
- Ensuring the proper structure and clarity of the instructions
- Effectiveness and comprehensibility
- User-centric and task-oriented
- Easy to be authored and published
- Available and easily accessible from multiple sites
- User-friendly format
- Visual information along with short action-oriented snippets of text in each step
How do you create outstanding digital work instructions?
- Specifying the goal of the work instructions
- Design the steps to reach the goal
- Add clear visuals of each step
- Adding a short snippet of action-oriented text to each step
- Share your digital work instructions with the end user
- Ensuring that the required workers have the most up-to-date information.
What are the popular use cases of the smart work instructions?
Industries commonly use digital work instructions to connect, support, and optimise frontline processes for the below-mentioned use cases.
- Safety
- Quality
- Maintenance
- Operations
- Training & Workforce Development
- Employee Engagement
- Continuous Improvement
More digital makes you more connected. Digital work instructions serve as interactive training material. In a period of adversity- shortage of skilled workers, smaller batch sizes and a rising number of product variants, precise work instructions are vital in production. Digital work instructions ensure that process knowledge remains in your company and can be further refined based on analysis of the gathered process data.
Ready to enhance your manufacturing efficiency?
Explore how TCard software can simplify your work order management, reduce downtime, and optimise your production processes.